As the asphalt paving industry moves toward more sustainable paving processes, pavement design remains the most important role in building sustainable pavement systems. The FHWA has laid out four pillars that define sustainable pavements: performance, environment, economy and social.
These four pillars are closely intertwined. It is important to recognize that three of these pillars are dependent on performance. This article will focus on the economic and performance pillars by discussing a few noteworthy design elements to consider as pavement designers navigate through the design process. Increasing the performance of asphalt pavement will increase the success of achieving the economic, environmental and social goals.
LCCA – New pavements
When an agency is planning a pavement project, a Life Cycle Cost Analysis (LCCA) should first be conducted. A LCCA is used to compare different rehabilitation strategies or pavement types using a present worth analysis. LCCA uses the initial project cost and future expenditures for a fixed period of years to calculate the Net Present Value (NPV) of different design alternatives which is then used to compare the design alternatives. Initial costs are relatively easy to determine based on current market prices. Future expenditures, however, are difficult to predict and yet are extremely important when conducting an analysis.
The National Highway System (NHS) Designation Act of 1995 required LCCA to be implemented on all NHS projects over $25,000,000. The FHWA’s Interim Technical Bulletin published in 1998, followed by the Life-Cycle Cost Analysis Primer published in 2002 both established guidance and parameters for accurately instituting the LCCA process.
One major element to consider in performing an LCCA is selecting an appropriate analysis period to be evaluated. The 2002 FHWA Primer states, “Transportation assets are constructed to provide service for generations. Competing design alternatives may each have a different service life, which is the time period that the asset will remain open for public use. Life-cycle cost analysis (LCCA), however, uses a common period of time to assess cost differences between these alternatives so that the results can be fairly compared.” The primer goes on to state that “… the analysis period should be long enough to include the initial construction or major rehabilitation action and at least one subsequent rehabilitation action for each alternative.”
To properly conduct an LCCA, the pavement designer must determine the initial design cost and the anticipated rehabilitation activities that are expected to occur over the analysis period. These future rehabilitation activities play a very important role in the final LCCA determination. When analyzing LCCA results, it is readily apparent that the time to the first overlay of an asphalt pavement significantly affects the outcome of the analysis. When discount rates are used to determine the NPV, the impact of the first overlay timing supersedes the impact of later rehabilitation activities and the salvage value that occurs late in the life cycle. Maximizing the time to first overlay is the most effective way to minimize the present worth determined in a typical LCCA.
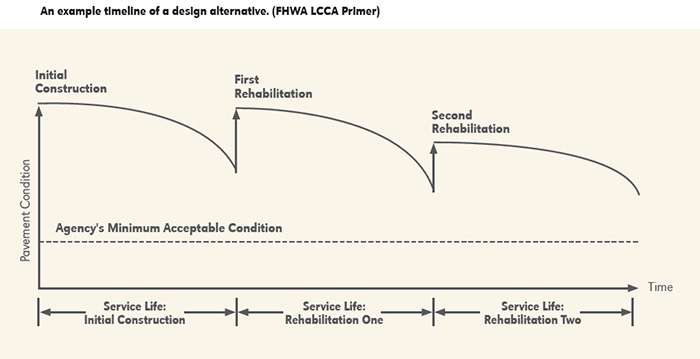
Looking beyond the analysis period
Another issue that deserves the designer’s attention is what will occur after the analysis period has expired. As noted in the FHWA Primer – transportation assets are constructed to provide service for generations. A pavement owner should look beyond the LCCA analysis period to consider the future for the corridor if they wish to minimize the impact on those future generations. The corridor will continue to be refurbished as the population and accompanying economic activity increases. Calculating the present worth of something 50 years into the future has little or no impact on LCCA today. However, after those 50 years pass, the next generation is required to deal with the ramifications of today’s LCCA results. An excellent example of these ramifications was detailed in an Asphalt magazine article entitled “Maximizing Pavement Life” in the Spring 2020 edition.
The salvage value of pavement at the end of life is severely discounted when conducting an LCCA. In fact, it is so discounted that it is common for salvage value to be assumed as zero. The real value of those salvaged materials can easily be seen in the savings incurred with the use of recycled asphalt pavement (RAP). RAP materials being repurposed in today’s pavements were purchased at a fraction of their current value. Aggregate in the 1970s was more than likely less than $10 per ton, with asphalt binder being under $100 per ton. It could be argued that the future value of in-place pavement material appreciates over time. Unfortunately, appreciating asset values are not adequately captured in current day LCCA processes.
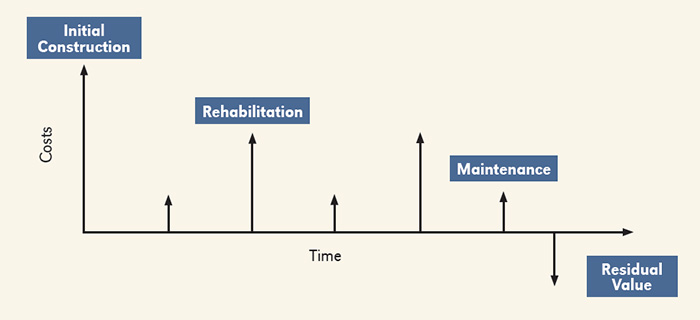
Binder specification influence on pavement performance
New pavement designs and materials are available today that outperform traditional design guidelines and recommendations. The 1992 Superpave binder specification (AASHTO M320), developed during the Strategic Highway Research Program, was a game-changer for the asphalt industry. The high and cold temperature binder performance parameters specified in M320 laid the groundwork for tremendous advances in the ability to prevent permanent deformation and thermal cracking. It is, however, crucial to remember that the research conducted when developing M320 relied on unmodified “neat” asphalt binder. The Multiple Stress Creep Recovery specification (AASHTO M332) rolled out in the early 2000’s further increased the ability of binder specifications to identify the permanent deformation advantages of polymer modified binders.
Industry design standards regarding binder grade selection are centered around the climatic conditions of the project location, as well as the traffic load rate, which is outlined in AASHTO M323 “Standard Specification for Superpave Volumetric Mix Design.” The standard asphalt binder grade is based on the high temperature and low temperature conditions of the project location. This “standard” binder grade is meant to serve as the minimum grade necessary to resist rutting and thermal cracking for the design climate under low to medium traffic conditions, at normal highway speeds. This standard grade is often altered or “grade-bumped” to account for project specific loading conditions, such as heavy or very heavy traffic loads, as well as slow or standing traffic patterns. Any of these conditions may require stiffer high temperature binder characteristics than what is required for “standard” free flowing traffic conditions.
The binder requirements for many projects exceed the performance limits of traditional neat binders. As a result, modifiers are incorporated to bolster the binder performance to meet these project specific conditions. Polymer modifiers are often utilized to meet demanding design requirements, especially on heavy traffic routes that require -28 or -34 binders. The spread between the high and low temperature thresholds in a PG binder grade is referred to as the Useful Temperature Interval (UTI). The greater the UTI, the more modification is typically required.
Pavement designers have a large array of binder grades at their disposal to meet any project conditions encountered. “FAA Specification P601 For Fuel Resistant Hot Mix Asphalt Pavement” makes use of polymer modified binders with over 7% polymer and high temperature grades, as high as PG 92. More information on these specialty mixtures can be found in a fuel resistant asphalt article published in the Spring 2021 issue of Asphalt magazine.
Asphalt binders with a greater UTI are an important design tool to consider when mixture performance parameters fail to meet project design requirements. There are two important benefits available to designers considering the use of higher modified binders: decreased rutting and increased crack resistance.
Less rutting
When using an asphalt binder with a greater high temperature binder grade, the risk of permanent deformation is greatly reduced. For example, when a binder grade of PG 76 or higher is utilized in a PG 64 climate with high quality aggregate and good construction procedures, rutting should not be a concern. Mixtures with very stiff binders have always been rut resistant but have been typically susceptible to thermal cracking. However, when those binders are stiffened with an elevated amount of polymer modifier, the cracking threat is greatly reduced, if not eliminated.
More resistance to thermal cracking
The stiffness of highly modified asphalt binder allows mixtures to be produced at lower design air void levels, which greatly increases crack resistance while maintaining low rut resistance. Pavements with regressed air void content (mixtures designed at 4.0% air voids but constructed at 3.0% design air voids) have been built in many areas of the US for years using traditionally specified binders. Air void regression can allow 0.3 to 0.5% additional asphalt binder in a mix, which will improve crack resistance.
The use of highly modified binders can allow mixes to be designed with very low air voids while maintaining excellent performance. The Utah DOT is rapidly expanding the use of very highly modified binders in mixtures containing design air voids as low as 1 to 1.5%, in single lifts, placed from 2” to 6” thick. Although these binders are very stiff, the lubricative properties of a mix with elevated binder content allows excellent laydown and compaction results.
Documenting pavement performance
A Pavement Management System (PMS) is an excellent tool that provides critical information to the pavement designer during the design process and provides a library for past and future pavement performance. When a pavement deteriorates to the point where it needs rehabilitation, the pavement designer needs to know what is currently on the roadway. Factors such as condition, thickness, age and existing in-place material, along with current and future traffic loading needs to be determined before rehabilitation strategies can be developed. If available, a PMS is an excellent source for that information.
Example use of a PMS
Fatigue cracking in the wheel path is typically the result of insufficient pavement thickness for the underlying subgrade and base. If the pavement is relatively new, serious analysis of the last project design or construction process needs to be undertaken to design a future rehabilitation strategy. If the condition has occurred over a long period of time, (much longer than the period assumed in the original design), a different course of action may be warranted. Pavement management data is crucial in determining the appropriate design strategy going forward. Including pavement material records in PMS data, can provide additional information to help the designer refine inputs to meet or exceed pavement life expectations. Increasing binder performance is a major parameter that can be modified to increase pavement life.
Are better performing mixtures cost effective?
When new materials are first considered, there is a high probability that existing PMS data will not be available. Mixture performance testing can give the designer the opportunity to see relative differences in laboratory mixture performance. Seeing those differences can provide some level of comfort in selecting higher performing materials, but the absolute outcome will not be known for certain until time has passed, and actual pavement performance data is gathered and recorded – hopefully, in a PMS.
An alternative thought process may be to calculate what a reasonable increase in pavement life would be needed to justify an increase in construction material cost. For example – assume an overlay project utilized air void regression as a design strategy, which resulted in a 0.4 percent increase in binder content. The pavement should be expected to last an additional length of time to justify the increased expenditure. The table above summarizes publicly posted bid tab data for a very recent bid letting on a state route in the Midwest. This state pays for binder and mixture items separately.
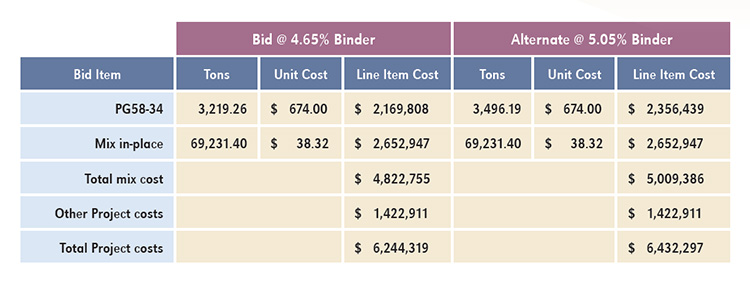
The chart above shows a differential of $187,979 (or 3.01%) increase in the original project cost. The question then becomes, how many years (or months) does the project need to last to justify the increase in cost? That would depend on the expected life of the overlay. If the pavement owner expects a 7-year life span, the pavement should last at least 3% longer which is 2.5 months. A 15-year expected life would have to last 5.4 months longer. Laboratory mixture performance testing could hint if that extended life estimate is reasonable, pavement management data will prove if it is successful. This thought process can be extended to other mixture parameters such as grade bumping into higher performance binders.
Conclusion
The importance of good pavement management data cannot be overlooked. As sustainability initiatives move into the pavement design community, the use of pavement management systems and thoughtful pavement design is crucial in designing sustainable pavement. Thankfully, the pavement design community has the tools needed to forge ahead in producing the longest lasting pavements possible to benefit future generations.
Blow is an Asphalt Institute Senior Regional Engineer based in South Dakota.