A compass providing direction with mix design and quality control
It takes the right tools and a thorough understanding of how to use those tools to get any job done right. Asphalt mix designs and quality control management tasks are no different. Having personnel equipped with experience and training makes the difference when it comes to time, quality and profitability in our industry.
Let’s ask: What tools are available to mix designers when they are faced with a design with new materials, an unfamiliar specification or within a new area with unfamiliar aggregate sources? Oftentimes, it is trial and error, word of mouth and a spreadsheet trying to get an aggregate blend to meet a specification band. And once a blend is developed, how does one predict field performance? Will it be prone to segregation? How sensitive will volumetric results be to production variability? These are all questions mix design practitioners face in their everyday responsibilities. One tool many in the industry use to help provide answers to these types of questions and problems is the Bailey Method.
What is the Bailey Method?
The Bailey Method is a systematic approach that reduces time required to develop an acceptable design while minimizing risk associated with production, placement and performance. The Bailey Method was developed in the early 1980s by Robert D. Bailey, Materials Engineer (retired) with the Illinois Department of Transportation. It is a procedure in which aggregate packing characteristics are evaluated. We often think of aggregate blending by weight. This tool helps practitioners understand the individual aggregates and final blends by volume and by weight. Using both measures, mix designers develop a better understanding of what influences Voids in the Mineral Aggregate (VMA), which is a critical volumetric property that directly ties to mixture durability.
“Anyone can design a mix in the lab that meets all the requirements, but designing one that works in the field and maximizes pay factors is another story. Whether it is to get a good starting point for doing mix designs with new aggregates or analysis of existing designs, the Bailey Method allows insight to the inherent characteristics of your designs, whether it’s susceptible to segregation, instability or compaction issues,” said Pat Koester, Vice President of Production with Howell Paving in Mattoon, Illinois.
The space between
To appreciate the value the Bailey Method can offer to users, one must have a clear understanding of VMA. What is VMA? Conceptually, imagine a volume of compacted mixture and visually remove the effective asphalt from the mix. The volume or the space between the compacted aggregates particles is the VMA. Mathematically, VMA is equal to the volume of air voids (Va) plus the volume occupied by effective asphalt (Vbe), or the asphalt that surrounds the aggregate particles in the mixture, as shown in the phase diagram.
VMA is a function of the properties of the aggregate in the mix and the type and amount of compaction. There are four primary properties that ultimately affect aggregate particle packing and resulting VMA. The gradation of the blend and the shape, strength and texture of the individual particles. It is important to recognize that the Bailey Method cannot ultimately “fix” aggregate characteristic issues, but it certainly can help designers understand and define issues with their materials. The Bailey Method can help mix designers evaluate adjustments to alter VMA with use of the loose and rodded unit weights per AASHTO T 19, in addition to aggregate gradation and specific gravity of each aggregate in the blend.
The importance of being earnest with VMA
There is a wise proverb that states, “To understand where one is going, he must know where he is starting.” Understanding VMA is no different. VMA is readily calculated with the following equation:
Where Gmb is the bulk specific gravity of the compacted mix, Ps is the percentage of aggregate by total weight of mix and Gsb is the bulk (dry) specific gravity of the aggregate. The key to accurately determining VMA is proper testing and determination of the Gsb of the aggregate blend. Values that are either incorrectly high or low will result in a VMA value that does not accurately reflect the volume of space available between the compacted aggregate particles. During the design process when the mix designer makes adjustments to asphalt content to achieve the required air voids, the resulting effective asphalt content may either be too low – which could lead to mix durability issues – or too high – which could lead to mix stability issues. If the combined blend Gsb (virgin and recycled) is inaccurate, the volume of effective asphalt is inaccurate. Some specifications allow the use of Gse (effective specific gravity of the aggregate) for recycled products and in some cases for the entire aggregate blend. Gse excludes the volume of absorbed asphalt, which means that it is included in the volume of effective AC (asphalt cement), resulting in an erroneously high calculated VMA value.
How does the Bailey Method work?
The Bailey Method starts with defining the Nominal Maximum Aggregate Size (NMAS) of the mix. The commonly used definition is “one sieve larger than the first sieve to retain more than 10 percent of the aggregate.” However, for the Bailey Method, NMAS was redefined in 2006 to use 15 percent. Knowing the NMAS, the user can then determine the “break” between the coarse and fine fractions in a combined blend gradation: the Primary Control Sieve (PCS). The PCS is determined by multiplying the NMAS by 0.22 and then using the closest sieve to that resulting value (see table below).
Mixture NMAS | NMAS x 0.22 | Primary Control Sieve |
37.5 mm (1-1/2”) | 8.250 mm | 9.5 mm (3/8”) |
25.0 mm (1”) | 5.500 mm | 4.75 mm (#4) |
19.0 mm (3/4”) | 4.180 mm | 4.75 mm (#4) |
12.5 mm (1/2”) | 2.750 mm | 2.36 mm (#8) |
9.5 mm (3/8”) | 2.090 mm | 2.36 mm (#8) |
4.75 mm (#4) | 1.045 mm | 1.18 mm (#16) |
Four principles work together to help users better understand aggregate packing while knowing which fraction (coarse or fine) is in control of the overall aggregate blend. The four principles are summarized here.
1. Volume of Coarse Aggregate
The first principle is driven by the user’s decision for the mix to be coarse- or fine-controlled. This is a function of the volume of coarse aggregate used in the design, which is called the Coarse Aggregate Chosen Unit Weight, (CA CUW). The Bailey Method is a “unit volume” method. The user chooses a volume of CA (coarse aggregate), which contains the resulting volume of voids. The CA voids are filled with an equal volume of fine aggregate. The remaining voids make up most of what is considered to be VMA. The figure shows a schematic of a fine-graded and a coarse-graded mixture based on volume expressed as a percent of CA Loose Unit Weight (LUW). Based on the volume of CA in the blend (as reflected by the percent CA LUW) one can visualize how interlock and load will be controlled within the compacted mix. Within the coarse-graded mix, the CA CUW is typically equal to or greater than 100 percent CA LUW. This will create some particle-to-particle contact in the coarse fraction that will create most of the load-carrying capacity of the mixture.
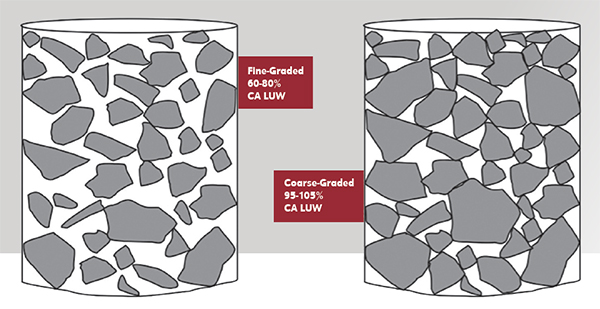
Conversely, for fine graded mixtures the CA CUW is less than the CA LUW. As shown in the figure, there is little to no contact of the coarse aggregate particles. This means that the fine fraction of the aggregate blend (minus PCS) carries most of the load in the structure, this expectation requires increased strength and texture in the fine fraction.
2. Coarse Aggregate Ratio
The second principle characterizes the coarse fraction of the aggregate blend (the aggregate retained on the PCS). The coarse fraction is split into two portions by defining the “half” sieve, which is equal to 0.50 x NMAS. The particle size distribution of the coarse fraction controls the packing characteristics of the coarse fraction (the aggregate retained on the PCS) and influences the packing achieved in the fine fraction (aggregate passing the PCS). Visualize the large (plus “half” sieve – “pluggers”) and small (“half” sieve to PCS – “interceptors”) portions of the coarse fraction. The focal point of this principle as it pertains to aggregate packing is that none of the small coarse fraction particles fit into the voids of the large coarse fraction particles. When it comes to understanding mix constructability, blends with high CA ratios may be difficult to compact in the field, whereas blends with low CA ratios may be prone to segregation.
3. Fine Aggregate Coarse (FAc) ratio
The third principle is the first of two principles that consider the aggregate packing characteristics of the fine fraction. Unlike the coarse fraction, the fine fraction (minus PCS) contains a broad enough range of particle sizes that it can be a blend of coarse and fine in itself. When viewing the fine fraction as its own “blend”, the PCS generally serves as both the Maximum and NMAS sieves. Therefore, we can determine the Secondary Control Sieve (SCS) by using the equation, SCS equals 0.22 x PCS. The FAc ratio is the percent passing the SCS divided by the percent passing the PCS, which is the “fine” portion of the overall fine fraction relative to the total fine fraction. The FAc ratio is critical to understand and depending on where the ratio lies; a change in the FAc ratio can impact the directional change in VMA. In other words, it matters whether the overall fine fraction is coarse-graded or fine-graded when it comes to adjusting the FAc ratio to alter VMA.
4. Fine Aggregate Fine (FAf) ratio
The final principle is the FAf ratio, which considers the packing characteristics of the fine portion of the fine fraction (minus SCS). Like the minus PCS, the minus SCS can also be viewed as a blend of coarse and fine. The Tertiary Control Sieve (TCS) is determined by multiplying the SCS by 0.22 and using the sieve that is closest to the resulting value. The FAf ratio is the percent passing the TCS divided by the percent passing the SCS. It is this ratio where one considers how materials like baghouse dust are contributing to aggregate packing and VMA. As a rule of thumb, as the FAf ratio decreases, the compactability of the fine portion of the fine fraction decreases. This can be problematic for field operations, as low FAf values may lead to mixture tenderness.
Putting the principles together for mix design development
There are many moving parts to this process. Mix designers know one decision to adjust a material in the blend translates to an impact elsewhere. How does one put it all together? It is the power of the Bailey Method (and corresponding spreadsheets) that can stitch it all together, run the calculations and decipher the interactions for the users. Based on the experience and mixture analysis by developers and users of the Bailey Method, each of the four principles has a recommended range for mix designers and will inform when a decision might have a negative effect on performance and constructability. After the designer gets results from the first trial batch, the Bailey Method can be used to predict VMA for any additional design trials.
“The Bailey method has helped our operations understand how to best design their mixes to align with their pit balance, aggregate properties and a number of other factors considered in the optimization process. Understanding these items and ensuring the mix type (coarse- or fine-graded) is properly accounted for in the design process has led to the development of optimized mixes that can be more readily produced to meet project specifications. In addition to optimization, being deliberate in the mix design phase has allowed the quality teams to know what the ‘right changes’ are when volumetrics indicate a change is needed,” said Marty McNamara, Director of Materials Quality, with Granite Construction in Reno, Nevada.
Operational support tool: making mix adjustments that make sense
Does the Bailey Method offer additional value once the mix design is complete and the mixture fits within the recommendations and specifications? Absolutely, as it is also a tool for use during production.
“It’s an indispensable tool during production, allowing the technician an estimation of change in volumetrics from aggregate adjustments. It gives one a better understanding of the role each aggregate plays. Too many times in the past we have adjusted the wrong direction because of the old thought process that manufactured sand creates voids, when in some mixes the natural sand does. It allows insight to mix characteristics to maximize pay factors,” said Koester.
What Koester is describing is the ability of Bailey Method user to be able to track volumetric properties of mixtures during production and understand the directional change in volumetric properties with blend adjustments. With accurate quality control (QC) data including combined blend Gsb, gradation, mix bulk and maximum specific gravity and AC content, the quality control staff can analyze blend adjustments (prior to making the change) and use the Bailey Method to predict VMA. One cannot overestimate the importance of representative samples and accurate data. When VMA changes, air voids also change the same amount, unless there is a change in volume of effective asphalt as well. This can be an extremely beneficial tool as many current specifications, including percent within limits, consider accuracy and variability in values like air voids. A good rule of thumb for QC personnel to recognize is that approximately 75 percent of the variability in air voids is the direct result of VMA variability.
The figure shows data where the changes observed in VMA during production clearly reflect the directional change in air voids. Recall the phase diagram of mix volumetrics, as the total space (volume) between the aggregate changes with production variability (from changes in gradation, shape, strength or texture of the aggregates), the available volume for effective asphalt and air voids changes.
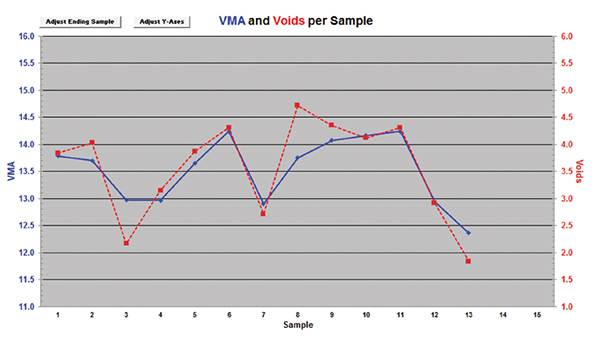
Future focus of the Bailey Method
Can the Bailey Method help designers with the increased focus and implementation of balanced mix design (BMD) concepts? Absolutely.
The Bailey Method may be a more effective compass moving forward. As various BMD-related mix tests are being implemented in mix design specifications to understand a mixture’s rutting and cracking resistance, the understanding of aggregate packing and optimizing volume for effective asphalt is critical.
For rutting tests, understanding which aggregate particles are in control of providing shear resistance and strength is critical. Think back to the portion of fine-graded control versus coarse-graded control. Effective asphalt content is a major driver in obtaining better cracking resistance results. Understanding how to ensure the compacted mixture has sufficient volume for adequate effective asphalt can be a powerful compass to provide direction of mix adjustments to meet requirements.
Ultimately, Koester sums it up best, “If a proportioning technician uses this method, it will reduce his time to acquire knowledge by years. There is no question the Bailey Method has saved our company money. It is a tool that works.”
Pine is Quality Control Director of Asphalt Technology at Heritage Construction and Materials. Wielinski is an Asphalt Institute Regional Engineer based in Ohio.
Learn more about the Bailey Method at the Asphalt Institute Feb. 12-16, 2024.