Historic project converted concrete pavements to asphalt
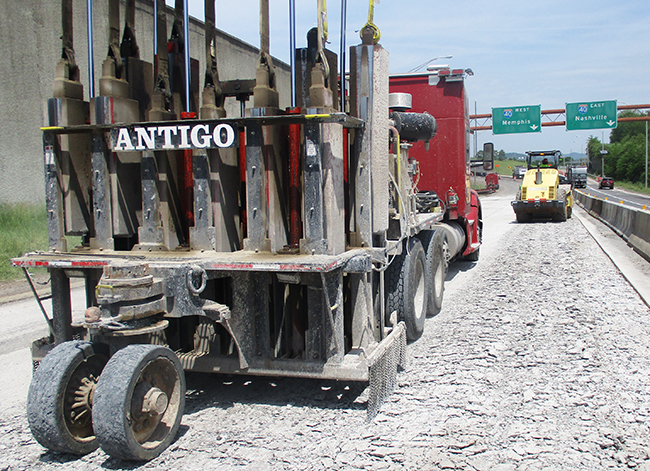
A reconstructed section of the I-440 corridor which is part of the loop around Nashville, Tennessee from I-40 to I-24 was opened in July 2020 – a full month ahead of schedule.
That was very good news for the approximately 110,000 drivers that use this roadway daily as it is now safer and less congested than the old roadway. The cost of the design-build project was $154 million which made it the largest reconstruction project ever by the Tennessee Department of Transportation (TDOT).
The project successfully converted a deteriorated concrete pavement to new asphalt pavement and was completed in one year and nine months.
According to Clayton Markham of TDOT’s Region 3 Innovative Delivery Division, the goals of the I-440 project were to:
• Address the deteriorated concrete pavements
• Improve safety
• Address congestion
This section of the I-440 corridor was originally built in the 1980s and therefore the concrete pavement was over 30 years old. The original structural section consisted of 10 inches of plain jointed concrete pavement on 5 inches of cement treated base (CTB). The pavement was badly deteriorated and needed major rehabilitation.
From a safety standpoint, the corridor was experiencing roughly 1.8 times the state crash rate standards. The project included provisions to dramatically improve safety for the traveling public.
As for congestion, the project was originally designed to carry 64,000 vehicles per day. With the current traffic volumes exceeding 100,000 vehicles per day, there was a need to increase capacity by adding lanes to mitigate traffic congestion. This project added two new traffic lanes and an occasional accessory lane.
The project was a design-build and the winning contractor was the one that offered the best value based on the total cost of the project and the target completion date. The contract required the contractor to both design the pavement section to meet TDOT structural requirements and to construct the project in a limited amount of time.
TDOT selected Kiewit Infrastructure South (KIS) as the general contractor for the project. Based on Kiewit’s proposal, the project would be completed no later than 708 calendar days after the project started in August of 2018.
Jordan Gregg of Kiewit Infrastructure South described the design-build approach like this: “This was an A (cost) plus B (time) design-build project with the B component equal to $100,000/day which means that both the project cost and schedule were critical factors in the selection process. This type of contract allows the contractor to consider innovative approaches to both accelerate construction as well to provide the most cost-effective way to accomplish the work.”
Structural sections
After looking at several options, the contractor decided on a pavement reconstruction approach that consisted of rubblizing the old concrete pavement and constructing a new asphalt pavement on top of the rubblized material on the existing lanes. To construct the new lanes, KIS placed an aggregate base layer topped with a cement treated aggregate base underneath multiple layers of asphalt pavement.
TDOT provided a minimum structural number that the contractor could use to design the pavement materials and thicknesses to be used on the projects. They also provided structural numbers for each of the paving layers (including rubblized concrete – 0.22 and existing cement treated base materials – 0.14). Using that information, the contractor settled on the following structural design for mainline and shoulder sections:
• Mainline over rubblized concrete – a total thickness of 8.75 inches of asphalt pavement
• Right shoulder over rubblized concrete – 3.5 inches of asphalt pavement over 5.25 inches of aggregate base
• Mainline over widening (new lanes) – 8.75 inches of asphalt pavement over a 3-inch asphalt treated drainage layer over an aggregate base (with variable depths of the base being cement treated)
The mainline asphalt pavement section consisted of 4 inches compacted thickness, 3.5 inches of intermediate of asphalt binder mix and 1.25 inches of asphalt surface mix. All three layers of asphalt pavement were constructed using a polymer-modified PG 76-22 binder.
The rubblization process
Rubblization (also known as fractured slab technology) is the process of fracturing an existing portland cement concrete pavement (PCCP) into small, interconnected pieces that serve as a base course for a new hot mix asphalt (HMA) overlay.
The rubblization subcontractor, Antigo, used their multi-head breaker (MHB) equipment to rubblize the concrete that stayed in place as a pavement base material and also to break up the existing concrete for removal. From March 2019 through March 2020, 158,000 square yards were rubblized, while 265,000 square yards were broken for removal and crushing to create aggregate materials used on the project.
Antigo used a combination of Badger Breakers and a vibratory “Z”-grid roller to perform the concrete rubblization. The project phasing required Antigo to mobilize equipment operators and/or equipment to the job site twenty-three times.
TDOT’s rubblization specification required a test section and test pit be constructed before beginning work to ensure the requirement for 3-inch maximum particle size on top and 12-inch maximum particle size throughout the existing concrete pavement. After some adjustments, Antigo was able to demonstrate that they could consistently meet the test strip requirements and were allowed to start the rubblization process.
As is typical in rubblization projects, the contractor was required to install edge drains to drain water from the existing pavement section before rubblization. In addition, an asphalt treated drainage layer was added under the new lanes in mainline pavement sections. The drainage layer and underdrains will facilitate the drainage of water that entered the pavement either from the bottom or top of the pavement.
Removal and processing of broken concrete pavement
By design, the contractor had to maintain a strict pavement elevation throughout the project to tie into existing structures on I-440 and also to maintain proper clearances under bridges going over the interstate. So, simply placing the new asphalt pavement on top of the rubblized concrete was not an option on much of the project. In those locations, the broken-up concrete would be removed from the roadway so a new full-depth pavement section could be built. This created a large amount of broken concrete that had to be dealt with. The question then was: “What to do with all of that concrete rubble?”
KIS solved the problem with an innovative solution of reprocessing and reusing the concrete rubble within the limits of the project. Where the elevation of the pavement needed to be adjusted, the broken concrete already fractured by the rubblization process was removed and stockpiled at a central crushing location within the project footprint. The broken concrete was then crushed to meet the size specifications for aggregate base materials. An estimated 215,000 tons of crushed concrete aggregate was produced and used as an untreated aggregate base layer and as a cement treated base material in construction of the new lanes where full-depth asphalt pavement sections were built.
There were many benefits in keeping the crushing operation within the confines of where the entire pavement structure needed to be removed. Kiewit estimates that this eliminated the need for approximately 24,000 heavily loaded trucks (over 300,000 tons of aggregate base materials) to import and export materials on to and off the project. This also reduced the wear and tear on surrounding roads and bridges and also offered significant safety benefits by eliminating the need for trucks to merge and exit from live traffic lanes. This also allowed for faster completion of the project and significant cost reductions.
Greenhouse gas emissions were reduced due to less truck travel and reduced need for the production of new aggregates.
Paving operations
Kiewit worked with their subcontractor Vulcan Materials to produce all 290,000 tons needed on the project. The bulk of the mixture came from two plants, with third plant being pressed into service when the accelerated project schedule called for more production. Overall, Vulcan’s two crews laid a total of 170,000 tons and KSI’s crew placed the remaining 120,000 tons.
Actual constructed thicknesses of mainline paving varied from a total thickness of 9.75” to 10.75” on rubblized concrete base and 12.25” to 13.25” on a crushed concrete base (with various depths at the top of the aggregate being cement treated) in new lane construction.
During preparation for paving, mixture placement and compaction, quality control and quality assurance procedures were in place to monitor the quality of the asphalt materials being placed. Substantial amounts of quality control testing were performed by the prime contractor and their subcontractors and quality assurance testing and inspection were performed by TDOT’s subcontractor HDR.
From a compacted density standpoint, over 2,500 cores were taken throughout the project to determine density for both the travel lanes and the longitudinal joints. An incentive/disincentive specification was used on the project to encourage the contractor to compact the asphalt mat to meet or exceed specified density in a consistent manner for both the mainline paving and along the longitudinal joints. One interesting aspect of the specification was that the measured density of both the joint and mainline density had to meet minimum density requirements to obtain an incentive for a given lot.
To expedite the completion of the project, the contractor submitted a cold weather paving and compaction plan and was allowed (in some cases) to pave outside of TDOT’s seasonal and temperature restrictions. This applied to base and binder layers only. TDOT closely monitored paving during cold weather and the contractor made good decisions on when (and when not) to pave in less-than-ideal situations without adversely impacting the quality of the in-place asphalt pavement.
Public relations
Anyone that has been around the rubblization of concrete pavements or aggregate crushing knows that these processes can be loud…very loud. And, because the location of the project is in an urban setting, TDOT knew that educating the public was essential. Almost all of I-440 is in a highly populated area consisting mostly of single-family homes, this was especially true of the western portion of the project. With many homes only separated from the roadway by relatively low walls, TDOT decided paving operations could be conducted both day and night, but rubblization and crushing operations were only allowed during the day.
TDOT also implemented a public relations effort to ensure that the public knew what to expect related to construction noise. They wanted to let them know what was causing the noise, how loud the noise would be and when they could expect to hear it. The effort included information on social media, radio, TV and even door-to-door activities.
This effort was effective and helpful in keeping the complaints to a minimum. By emphasizing the green aspects of the project that reused the existing pavement materials either in-place through rubblization or by reprocessing concrete rubble as an aggregate base within the confines of the project, TDOT wanted the public to know that they were being environmentally responsible. TDOT also was able to communicate the expected improvements in safety and traffic congestion with the new project. The message from TDOT was: “It is going to be noisy and will take some time, but it definitely will be worth it!”
Conclusion
The I-440 reconstruction project demonstrated using the benefits of the design-build approach to contracting as well as the advantage of using well-proven fractured slab technology to convert a worn concrete pavement to a high-quality asphalt pavement. The completion of the I-440 project was a big win for both the Tennessee DOT as they were able to reconstruct I-440 in a cost-effective and efficient manner and the traveling public as they can now enjoy a safer, smoother and long-lasting asphalt pavement.
Horan is an Asphalt Institute Senior Regional Engineer based in Virginia.