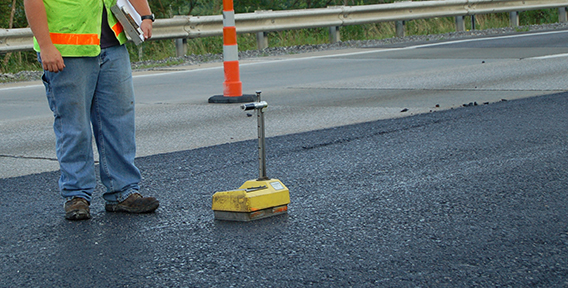
Like a multitude of other things, a good quality, long-lasting pavement costs money. The pavement design, materials, production, placement and compaction and a whole host of other secondary activities all add to the overall cost.
It’s only natural that when you spend a lot of money on something, you want to make absolutely sure that you’re getting what you paid for. Quality assurance is important because of the large amount of taxpayer money it takes to build pavements, so we want to make sure it’s money well-spent.
1.
The basics of quality assurance
Understanding some of the basic terms used in quality assurance will bring important insight to a well-rounded discussion of the topic. We’ll look at the three most commonly used terms, which are all defined in Transportation Research Board’s Circular E-C137, “Glossary of Transportation Construction Quality Assurance Terms.”
Quality assurance (QA) consists of all planned and systematic actions necessary to provide confidence that a product or facility will perform satisfactorily in service. QA includes the elements of quality control (QC), acceptance, independent assurance, dispute resolution, laboratory accreditation, and personnel certification.
Quality control (QC) is the system used by the contractor to monitor, assess, and adjust their production or placement processes to ensure that the final product will meet the specified level of quality. QC includes sampling, testing, inspection, and corrective action (where required) to maintain continuous control of a production or placement process. Basically, QC is work that the contractor does to ensure that they are providing a quality product.
Acceptance is the process whereby all factors used by the agency (i.e. sampling, testing, and inspection) are evaluated to determine the degree of compliance with contract requirements and to determine the corresponding value for a given product. In other words, it’s the work the agency does to ensure that they are receiving a quality product.
The focus on QA has resulted in a number of certification programs that provide training and/or certification that a laboratory, technician, or inspector has the ability to meet certain quality requirements and/or levels of proficiency. Examples include Asphalt Institute’s (AI) Mix Design Technology Certification (MDTC) program, National Binder Technician Certification (NBTC), and the upcoming Paving Inspector Certification (PIC) program. Also, AASHTO re:source (formerly AMRL) provides proficiency sample testing and laboratory accreditation on a national scale.
2.
Components of a quality control plan
Many agencies require the contractor to submit a written QC plan, outlining who will be responsible for the work, what exactly will be done to ensure quality work, and how test results will be documented and shared. Specific elements typically include:
• Names of QC personnel and the company organizational structure
• The duties, responsibilities, and authority of the QC personnel
• What qualifies the personnel (certifications, training, etc.)
• Laboratory equipment lists and calibration/verification information
• What exactly will be sampled (binder, aggregate, mix, etc.)
• What methods will be used to obtain the samples
• How often/how many samples will be obtained
• How samples will be reduced to testing size
• What tests will be run on the samples
• Criteria used to determine whether material meets specifications
• How out-of-spec materials will be corrected
• How test results will be documented and shared
AI’s MS-22, “Construction of Quality Asphalt Pavements” shows an example summary table of a QC Sampling and Testing Plan in Table 10.1.
Trial batches, which are a limited plant run before full production begins, are extremely helpful for contractor QC. Trial batches can be required or voluntary, but it is best if they are performed on every project, required or not. There are two main benefits of a trial batch.
First, trial batch samples indicate whether the asphalt plant is capable of producing mix that matches the design and meets specifications. This allows an opportunity to make any necessary plant or mix adjustments to get the mix in spec before project construction begins.
Second, it allows the contractor and agency technicians to ensure they get acceptably consistent results on a split sample from the trial batch. This allows time to reconcile any differences in testing before full production begins. You can avoid a lot of headaches if you get those things straightened out before the main work starts.
After the trial batch, a test strip proves that the contractor can successfully place the mix according to specifications. A test strip is done on a short length of pavement, typically 500 tons or 1000 feet. The test strip allows the contractor to fine-tune the procedures for obtaining proper compaction. Plus, it allows one more opportunity to sample and test the mix to make sure it’s still in spec before full production begins.
Usually, the contractor is limited to additional small test strips if the first one is unsuccessful until they prove that that can place the mix within specifications.
3.
Sampling methods for asphalt mixtures
We need a way to ensure that our samples are representative of the material used on the project. If the samples aren’t representative of the materials used on the project, there’s really no point in testing them.
One aspect of representative sampling is splitting the project into distinct “lots.” TRB Circular E-C173 defines a lot as “a specific quantity of material from a single source which is assumed to be produced or placed by the same Splitting the project up into lots is important because we wouldn’t want to remove and replace the entire project when only one small part of it was bad. Another reason lots are important is that if we average the deviations in lot 9 with the rest of the lots, we might never notice a problem in that area since it was only a small part of the whole project.
We also need to understand the different ways in which lots are identified. They are generally measured in one of three ways. One is by time interval. Common time intervals are half day’s production, resulting in two lots per day, or a lot might be defined by a full day’s production.
Another is by quantity intervals. Common quantity intervals are 1,000 tons (i.e. one lot = 1,000 tons) up to 10,000 tons per lot, depending on anticipated production rates and/or the local specifications.
The third common lot measurement is by distance. For example, one lot might equal 1,000 feet, or maybe the agency specifies one lot is 10,000 feet.
Another key component of obtaining a representative sample of any construction material is the concept of random sampling. Random means that all parts of the lot of material have an equal chance of being included in the sample. Random sampling helps ensure that an unbiased sample is obtained.
We also need to understand that there are specific protocols for obtaining samples. For example, AASHTO R 97 and ASTM D 979 give the standard procedure for obtaining loose samples of mix and AASHTO R 67 and ASTM D 5361 give the standard procedure for getting compacted samples of mix from the roadway.
4.
Testing methods for asphalt mixtures
We test asphalt mixtures because we want to make sure that the mixture supplied by the plant is the same mix that was designed in the lab and approved for use on the project.
In testing, we should understand that asphalt test results are not always exactly the same from sample to sample or from lab to lab due to variability. Variability in test results comes from at least three areas: 1) the material itself is variable from spot to spot, 2) there is variability in the sampling process, and 3) there is inherent variability in the testing process itself.
Many different tests could be specified for project QA, but at a minimum, these basic tests will typically be specified:
1. aggregate gradation (AASHTO T 30, ASTM D 54444),
2. binder content (AASHTO T 308, ASTM D 6307, AASHTO T 164, ASTM D 2172)
3. lab-molded density (AASHTO T 312, ASTM D 6925)
4. roadway density (AASHTO T 166, T 275, or T 331, ASTM D 2726, D 1188, or D 6857)
To determine the aggregate gradation of asphalt mix samples, we need to have a way of separating the asphalt binder from the aggregate. Typically included in the separation process is a determination of the mix binder content. That’s predominantly done in one of two ways, either by ignition oven or by chemical extraction.
A potential point of confusion regarding density is the difference between lab-molded density and roadway density.
Lab-molded specimens are created in the lab from loose mixture sampled from the project using a Superpave Gyratory Compactor, a Marshall Compactor, or some other compaction device. Lab-molded density gives QA personnel information about the mix properties.
Roadway cores are cut from the roadway and then tested in the lab. Roadway density primarily gives information regarding the quality of compactive effort on the roadway. Roadway cores can also be used to verify that the mat thickness meets design requirements.
5.
Plant production quality control data analysis
Quality control of plant production generally involves three key areas:
1. verifying the job mix formula (JMF)
2. documenting and organizing the QC data that is generated daily
3. adjusting the production process when necessary
Job mix formula verification is, in essence, testing and analyzing field-produced mixture to make sure that what was designed in the lab is being faithfully reproduced in the field; that every design criterion that has been established in both the mix design and the specifications is being met.
When the plant first begins to try to duplicate the laboratory mix, it’s very common to see some differences, and some initial adjustments are almost always necessary.
Field-produced mixtures tend to have lower air void contents and VMA than the targets established in the JMF. A major reason for this is the large volume of aggregates handled in the field, the particles are tumbling over each other and abrading the angular edges that create VMA and air void space and allow the aggregate particles to pack together more tightly. Furthermore, the fine rock dust that gets abraded from the particles will fill the void spaces between the larger aggregate particles, taking up even more air void space.
Plant operators typically need to make slight adjustments to the percentages of each material being fed into the drum to bring the mix volumetrics back into specification.
Spreadsheets are very helpful when it comes to documenting QC results and for quick review and comparison. Spreadsheets should be thoroughly vetted to make sure there are no calculation errors before putting them into production. Cells with formulas should be protected so the technician can’t accidentally type over it.
They should include cells for all of the raw test data and should also perform checks on the robustness of the data. For example, AASHTO T 30 gradation includes a requirement that the sum of the of the measured masses from the sieving operation checks within 0.2 percent of the total dry mass after washing. Data checks based on summing masses or percentages can make it easy to identify mistakes or typos in the spreadsheet.
Another great way to document, review, and compare QC results is through the use of control charts. Control charts plot data for a specific mix parameter as they are run. They make it easy to spot trends. For example, if binder content data points were all below target, a plant adjustment would need to be made to bring the binder content up. If the binder contents were trending downward, the plant operator should be notified. Maybe a filter in the binder line is slowly clogging, resulting in less binder being added over time.
It’s very important that QA test data is quickly reported and analyzed. The contractor needs to be notified in time to make any necessary corrections to bring the mix or process back into specification. It is much better to address problems in a timely manner and have a good quality roadway because of quick corrective action than to simply assess pay deductions for problems that were discovered too late to be addressed.
6.
Placement quality control data analysis
The primary quality factors for placement of the mix include temperature, compaction, thickness, and smoothness.
Because the way an asphalt mixture behaves and performs depends so much upon temperature, there are several places regular temperature checks need to be made during the QA process.
One of the areas in which this is important is the ambient and/or the existing pavement surface temperature. Asphalt in a mass in the truck retains its temperature very well, but once the mix is placed in a comparatively thin mat across the roadway, it will begin to lose temperature relatively quickly. The thinner the mat, the more quickly it will lose heat. Hot mix asphalt (HMA) needs to be hot to be workable enough to compact properly. If the ambient temperature or existing surface being paved is cool, it only exacerbates the temperature loss. Minimum surface temperature specs might be as low as 40°F for thicker mats or warm mix asphalt (WMA), and up to 70°F for some specialty mixes.
At the plant, the mix temperature should be checked at the discharge chute to ensure that the mix has not been overheated. If the mix runs too hot, it will prematurely age the mix, making it more brittle and susceptible to cracking. Typical maximum discharge temperature specifications might be up to 350°F for mixes with modified binder and 325°F for mixes with unmodified binder.
Another important location is the temperature of the mix immediately behind the paver. The mix needs to be hot enough or workable enough to be compacted to the target density by the rollers. The rollers may not be able to properly compact a mix that is too cool. Most specifications say that the mix here should be no less than 250°F. Also be aware that if the contractor is using WMA, this minimum temperature will probably be lower.
The final area the inspector should monitor several times throughout the day is the temperature by which to finish compaction operations. Once the mix reaches a certain temperature, not only will further rolling not help achieve further density, but it may actually harm the pavement by breaking aggregate. Remember that the function of the finish roller is simply to iron out any remaining wrinkles in the pavement and make it smooth, not to gain further density. Typical specifications say that compaction operations should be complete by the time the mix reaches 180 degrees Fahrenheit.
Generally speaking, compaction quality is controlled by both the QC and acceptance personnel. Roadway cores are the “gold standard” for density determination, but density gauges are used for a much quicker in situ density estimation. Density gauges are excellent tools to determine when the density increases. However, the magnitude of the density measured is not necessarily accurate unless it is correlated in some way with roadway cores.
QC personnel use quick results from a density gauge to initially direct compaction operations. Acceptance personnel usually cut cores from randomly-selected areas of the pavement, which are then tested and compared to density specifications. QC personnel will compare the core results with the density gauge results in some way to establish either a formal or informal correlation. QC personnel then direct ongoing compaction operations using correlated density gauge results.
7.
Acceptance tests and acceptance criteria
Agency specifications have generally moved away from “method” specifications and toward some type of “end-result” specifications. End-result specifications move away from the agency defining the processes of construction and toward the testing of the mixture and pavement for conformance to the specification. In other words, they don’t tell you exactly how to do everything, they instead define what good quality looks like, and then test to see if the contractor reached that pre-defined level of quality. The agency then either 1) accepts the work if it meets specifications, 2) applies some type of pay adjustment if it doesn’t quite meet specs, but stays within acceptable quality limits, or 3) rejects the pavement if it doesn’t meet certain basic quality expectations.
That shifts the responsibility from the agency toward the contractor, but it also allows the contractor to take initiative to find better ways to get the work done and end up with equal or better-quality pavements.
The criteria that are most commonly measured on a project can be split into two main areas: criteria that tell us about the quality of the asphalt mixture itself and criteria that tell us about the quality of the placement work during construction.
The mix criteria that are typically measured include the aggregate gradation, the percent binder content, the percent air voids and the Voids in Mineral Aggregate or VMA. Many specifications add multipliers to some asphalt mixture pay factors to place focus on criteria deemed more important to the longevity of the mix.
The placement criteria that are typically measured include the percent roadway density, the pavement smoothness, and the pavement thickness.
In some situations, the cost or difficulty of obtaining a usable sample prevents direct testing of the roadway, and compaction quality needs to be assessed in a different way. Thin lifts, leveling courses, open-graded friction courses and non-uniform lifts are often assessed using a method specification.
Typically, the method spec will include requirements, like documenting that:
• a certain number, type, and size of rollers were used
• the rollers completed a given number of passes over each section of the roadway
• the compaction took place within the required temperature range
• the surface was rolled until it was free of roller marks
As you can see, there are many areas of action which are necessary to provide confidence that a product or facility will perform satisfactorily in service. Now more than ever, agency budgets are being strained to the limit, but a good QA program can help ensure that our asphalt roads are smooth, quiet and last a very long time.
Gierhart is an Asphalt Institute Senior Regional Engineer based in Oklahoma.