A recently released report out of the University of Illinois Center for Transportation entitled “Performance of Interstate Rubblization in Illinois” summarizes the performance of rubblized pavements on the Illinois interstate system over the last two decades.
What is rubblization?
Rubblization is the process of fracturing the existing PCC (Portland Cement Concrete) Pavement (PCCP) into small, interconnected pieces that serve as a base course for a new asphalt overlay. Figure 1 shows a worn-out concrete pavement before and then after rubblization, on the right. By converting the slabs into a high-quality aggregate base, rubblization eliminates slab action and the possibility of any reflective cracking up through the new asphalt overlay. Other inherent distresses of PCCP are eliminated as well, such as D-cracking, alkali-silica reaction, slab rocking, pumping and curling. Rubblization also destroys the bond between concrete and any steel, making it suitable for any type of PCCP.
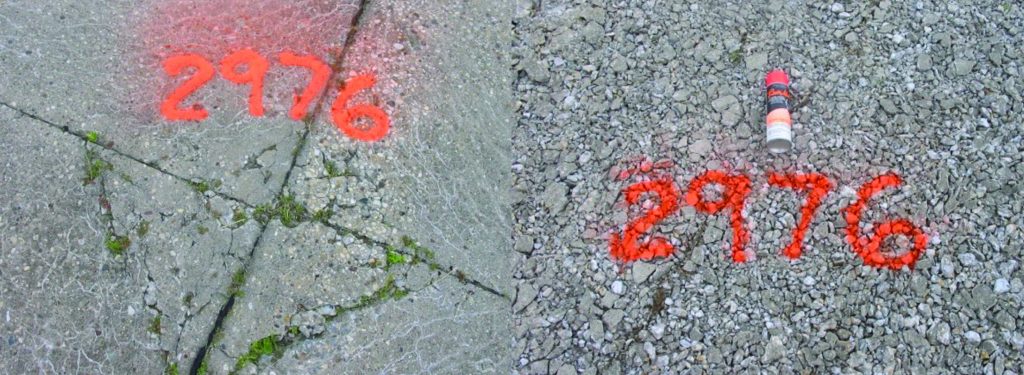
Rubblizing and overlaying with asphalt converts a failed rigid (concrete) pavement system into a new flexible (asphalt) pavement system. This process has multiple advantages relative to complete reconstruction. Since the concrete stays in place, there is no need to haul and dispose of the existing structure; no costs associated with the purchase and delivery of new aggregate base materials, which also conserves natural resources and is potentially good for the environment. Greenhouse gas emissions are drastically reduced due to less construction activity and less material production equipment usage and less truck travel. Because the subgrade is never exposed to weather delays, the construction time is expedited along with a corresponding reduction in lane closure time.
History of rubblization in Illinois
The Illinois Department of Transportation (IDOT) was an early adopter of the process. Their first rubblization section was on Interstate 57 in south-central Illinois as part of the Strategic Highway Research Program’s (SHRP) Long-Term Pavement Performance experiments. The “Specific Pavement Study 6 (SPS-6)” evaluated rubblization alongside traditional rehabilitations of patch and overlay, patch only and full concrete pavement restoration (CPR) such as patching and pavement grinding. The project located south of Champaign, Illinois, had two 500 ft. rubblization sections, one with a 6-inch hot-mix asphalt (HMA) overlay and the other with an 8-inch HMA overlay. The early success of this project led to six additional experimental projects by the end of the 1990s.
Early projects were built under traffic with “soft” barriers between the work lane and active traffic lane using a mill and inlay technique. Changing traffic conditions; increasing speed limits, higher volumes, and increased percentages of trucks would later result in the use of median crossovers and barrier walls to protect workers and travelers alike.
Performance data
The main source for performance data was IDOT’s asset management system, which has network-level summary information on surface condition, rutting and traffic. This well-established process collects pavement management data on the interstate system annually and assigns a Condition Rating Survey (CRS) on pavements. A CRS value between 1.0 (impassible) and 9.0 (newly completed construction) is assigned to each pavement in the system. As time and traffic accumulate the CRS will deteriorate. A value of 5.5 or greater represents an acceptable condition on the interstate system, below this value a surface restoration needs to be considered.
Data analysis
The data analysis included determining trends in rutting with structural traffic, CRS with age and design traffic with actual traffic served. Compounding the data analysis for the research team is the simple fact that asphalt mixes and cross-section details used by IDOT have changed over time. The use of rubblization pre-dates the SHRP’s Performance Grading system and the Superpave Mix design procedures, so the researchers grouped projects with like mixes together for improved trend line analysis. They were grouped by binder grade, and surface mix; type IL-9.5 or Stone Matrix Asphalt (SMA).
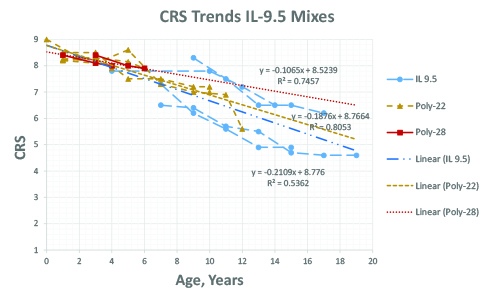
Figure 2 shows the CRS trends for projects that specified IL-9.5 mixes. AC-20/PG64-22 is a non-polymer mix that represents typical HMA mixes used prior to the full adoption of Superpave mixes in the late-1990s. IL-9.5 mixes utilizing polymer-modified PG70-22 and PG76-22 asphalt binders are grouped and represented by “Poly-22.” Likewise, IL-9.5 mixes utilizing polymer-modified PG70-28 and PG76-28 asphalt binders are grouped and represented by “Poly-28” in the graph.
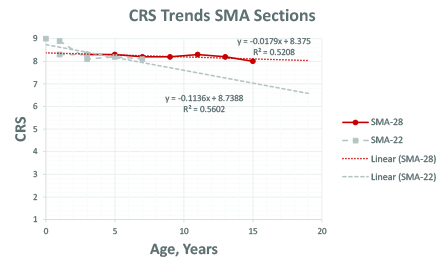
Figure 3 presents the CRS trends for SMA projects using the same PG grades as defined above compared with age from original construction. Most notably are the SMA-28 data trends which are extremely flat over the early life of the pavement. The researchers go on to point out that there are very few rubblization projects that were paved with an SMA using a PGXX-28 binder, and one of them is a Long-Life research project on I-70 that specified the use of SMA-28 in the entire asphalt pavement thickness. For this reason, the researchers added a trend line shown in Figure 4 using only the last three data points as likely a better predictor of future performance.
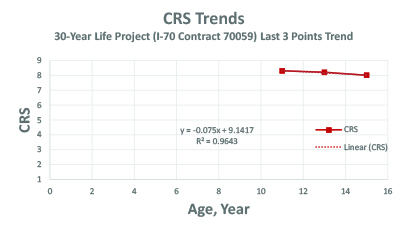
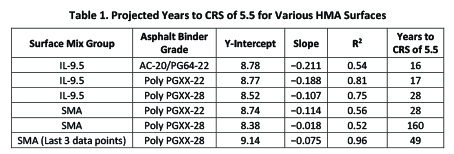
Table 1 summarizes the slope and simple linear regression analysis. This information was used to predict the number of years to a CRS service level of 5.5. The researchers go on to point out that these “predictions” are a rather simplistic approach and, “at best”, merely provide a ranking between the various HMA mixes and not a true prediction of time to the end of service life.
Rutting trends
For rutting trends, the researchers used all available rutting data without separating surface mix types or PG grading. Traffic counts of passenger vehicles as well as single-unit and multiple-unit trucks were converted to 18,000 lbs equivalent single axle loads (ESALs) for flexible pavement and presented in Figure 5 as rut depth versus ESAL. Using a logarithmic regression trend line, a traffic value of 100 million ESAL would result in an average rut depth of only 0.22 in. While this would be considered exceptional performance, such a projection far exceeds the dataset, currently 31.6 million ESALs.
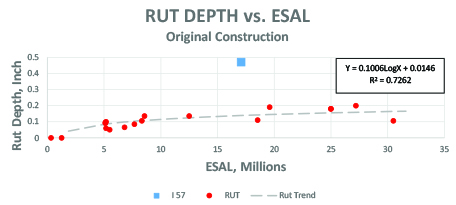
Study findings
As a result of this study, several findings were made as to the current state of the practice of rubblizing design, construction, and performance in Illinois, as follows:
• Overall, rubblization is providing good to excellent performance and exceeding design expectations.
• The design process is conservative. Fatigue cracking has not been observed in the original rehabilitation, which is providing service beyond the design traffic. Overlays that result in no additional structure (mill and fill) are not experiencing fatigue cracking.
• Rutting is not excessive in the sections rehabilitated using rubblization and is similar to full-depth HMA.
• The selected asphalt surface mix greatly impacts the CRS performance of the section, with SMA and softer PGXX-28 grade mixes providing increased life over traditional IDOT PGxx-22 grades and IL-9.5 surfaces.
Report recommendations
While rubblizing has demonstrated good to excellent performance to date, the data suggest that key policy and materials selection choices can greatly and consistently improve performance.
The following are recommended to achieve this end:
• Select SMA with PGXX-22 or IL-9.5 with PGXX-28 for the surface mix to increase performance at limited additional cost. These combinations showed trends of an approximately 50% increase in life over traditional IL-9.5 with PGXX-22.
• Limited data suggest that SMA with PGXX-28 could increase pavement life even more and could be the ultimate surface for HMA over rubblized pavement. Additional sections using this combination should be utilized to verify this trend, evaluate cost, and adopt as practical.
• Current IDOT pavement-selection procedures analyze rehabilitation activities over a period of 45 years to compare PCCP to full-depth HMA pavements to determine the lowest life-cycle cost. When rubblization is considered, the same maintenance models are used for rubblization and HMA pavement as for full-depth HMA. Currently, the maintenance models use a life of 15 years for the HMA surface, resulting in resurfacing at years 15 and 30 in the life-cycle calculation. The data in this report would indicate that the 15-year life used in the current selection process is based on the performance of the older mix designs using AC-20 or PG64-22 mixes. As more advanced surface mixes using SMA or PGXX-28 asphalt grades are adopted, improved pavement performance is expected. This will precipitate the need to update the selection models to reflect the improved performance of these mixes.
In closing, I think Antigo Construction, Inc. President Matt Shinners says it best when he ties rubblization and perpetual pavements together. “The recently published (ICT) report verifies what many have known for several years – asphalt overlays on rubblized concrete pavements are performing very well in Illinois on its interstate system.”
“Don’t just take my word for it, the report uses actual Illinois DOT pavement management system data to make a clear determination that these pavements are significantly exceeding their design expectations. I suggest that Illinois now has many miles of perpetual pavement that will only require occasional mill and fill,” added Shinners.
Jones is an Asphalt Institute Senior Regional Engineer based in Ohio. He began his tenure with the Asphalt Institute in 2001.