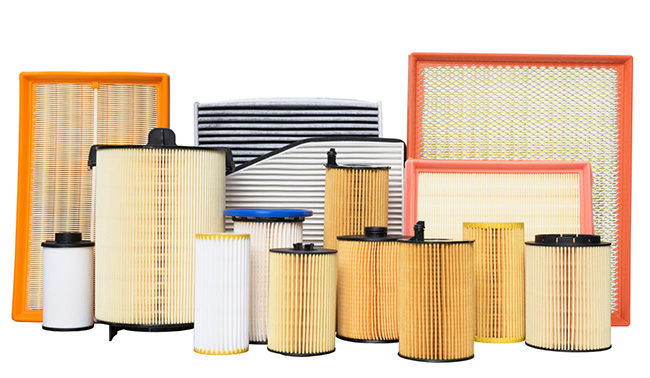
By Mike Anderson, P.E.
My life has started to revolve around filters. I have reminders on my phone to tell me to change my HVAC filter every 75 days. My refrigerator has a water filter reminder that shows up on the door panel. We built a pool this past winter, so now I clean the skimmer basket and big cartridge filter on a routine basis. My possessed robot vacuum (Lab Corner: Summer 2022 issue of “Asphalt”) has a filter and brushes that must be regularly cleaned…not that I want to get too close to it anymore.
The realization finally hit me that filters were becoming my obsession when my upright vacuum cleaner stopped working and I began troubleshooting the problem. “Clean canister?” Of course, I can see when it fills up. “Clean foam filter and cloth filter pad over motor intake fan?” A little dirty, maybe. I don’t clean them as often as I should, but I got it. “Clean HEPA filter over motor outflow?” Wait, what? “Clean or change every 2-3 months.” ??? I’ve had the vacuum for four years and didn’t even know that filter existed. Maybe I should have read the operations manual, but seriously, it’s a vacuum cleaner.
Filters do their job of keeping fine particles from getting in the way of our equipment performing properly. The PG asphalt binder specification also has filters to ensure that an asphalt binder can be properly characterized. Unfortunately, like my vacuum cleaner’s HEPA filter we don’t often think about those PG filters when grading our binders.
Because it isn’t in a nice table, asphalt technologists often miss reading Section 5 of AASHTO M320 (ASTM D6373) and M332 (ASTM D8239). That section is referred to as “Materials and Manufacture” and tells us what to consider when grading our PG binders. Thirty years ago those conditions were easily met by petroleum asphalt binders, even with typical elastomeric modification. Today, there are different materials, blend products and modifiers that may be added to our PG binders. So it is good to revisit those conditions and ask ourselves what do we need to consider?
Solubility
An often-overlooked part of the specification requirements is the solubility requirement. The test was originally proposed in 1903 by A.W. Dow as a way to ensure the quality of asphalts. At that time, Trinidad Lake asphalt was typically used and the amount of insoluble matter was known to be in a certain range. The specifiers wanted to use Trinidad Lake asphalt and therefore wanted a certain amount of insoluble material in their asphalt to provide a stiffening effect.
As the use of refined petroleum asphalts became much more prevalent, it was understood that they did not contain insoluble material like natural asphalts, such as Trinidad Lake asphalt, and the test was retained in specifications to ensure that the asphalt binder does not contain insoluble organic and inorganic matter that do not contribute to the “active cementing constituents” of the asphalt binder. In other words, adding filler to the asphalt binder to stiffen it is not really helping improve the quality of the binder and its ability to do its main job of cementing the rocks and sand together into a cohesive mixture. The requirement is that the asphalt binder be 99.0 percent soluble and, in the case of ASTM D6373/D8239, adds the caveat that any insoluble component shall be substantially free of fibers.
Isotopic behavior
Since we are on the subject, why is the requirement that the insoluble component is substantially free of fibers? Fibers that are used in asphalt typically have high aspect ratios – their length is much greater than their diameter or width. This can lead to anisotropic behavior – meaning that the way the fiber orients can affect the property that is measured. The PG specification assumes homogeneous materials, and therefore, isotropic behavior.
Particle size
Section 5.5 of AASHTO M320/M332 (Note 5 of ASTM D6373/D8239) states that the specification is not applicable for asphalt binders in which fibers or other discrete particles are larger than 250 µm (0.25 mm) in size. Testing an asphalt binder modified with particulate matter that is greater than one-quarter of the size of the least dimension means that the testing will be inherently more variable because the size of the particle impacts the test response. For DSR testing, the least dimension is a 1-mm gap when using the 25-mm parallel plate geometry. Thus a 0.25-mm maximum particle size is specified.
Violating one or more of these conditions doesn’t mean we can’t test the product that has insoluble material or fibers or particles greater than 0.25 mm; it just means that the product cannot be sold as a PG binder meeting AASHTO M320/M332 or ASTM D6373/D8239. It is those filters that help the specification perform properly for the user.
For questions or more information on the research, testing, and training services provided by the Asphalt Institute Laboratory, please contact Wes Cooper, Gary Irvine or me. We can help filter out what you need.
Mike Anderson is the Director of Research and Laboratory Services at the Asphalt Institute.