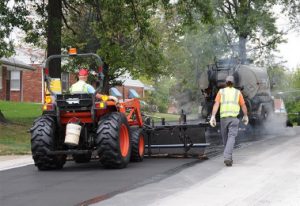
For over 40 years, geosynthetics have been used in road construction to extend pavement life. Geosynthetics provide soils and aggregate segregation, subgrade stabilization, moisture barriers to prevent subgrade deterioration and reinforcement of the pavement surface.
Geosynthetics used in road construction include fabrics, grids, and composites that can reduce reflective and alligator cracking of the pavement surface when correctly installed.
Fabrics
Fabrics have been around the longest and primarily serve as a moisture barrier and stress absorbing interlayer to mitigate reflective cracking. They are woven or non-woven primarily from polyester, polypropylene, and fiberglass.
Non-woven fabrics are needle punched and / or heat bonded in the manufacturing process to improve field application. This creates a fuzzy surface on one side to enhance bonding to a tack coat and the other side is resistant to wear and delamination from foot and equipment traffic during construction.
Woven fabrics are more suited for subgrade applications requiring material separation, stabilization, and filtration. The most critical aspect of using a fabric as a surface course interlayer is ensuring the application is performed correctly with the proper equipment, techniques, and conditions so the fabric lays flat, fully bonds to the surface, and there are no wrinkles or heat shrinkage.
Grids
Grids have become more common within the past 20 years in paving systems due to their potential to mitigate cracking. They are made from knitted or woven sheets consisting of fiberglass or polyester filaments.
Grids come with square or rectangular openings from ¼” to 2” wide and provide a higher level of stiffness and superior tensile strength when compared to fabrics. These materials are ideal for areas with weak subgrades or where chemical stabilization of the soil is not possible due to potential subgrade reactions. Grids are also used as a surface course interlayer.
Composites
Composites consist of a fabric and grid that are laminated together. The fabric provides the moisture barrier, absorption of asphalt, and continuous bonding while the grid contributes crack resistance with increased stiffness and tensile strength.
When a geosynthetic layer is used as a surface course interlayer, a tack coat is applied to the road surface that has been milled or prepared otherwise for an overlay or chip seal. Tack coat application rates are specific to the type of system being used. The residual emulsion application rates should be increased by about 2/3 if using the bar rate to account for the water in the emulsion. In some cases, the manufacturer will impregnate the geosynthetic with an adhesive so it will bond without a tack coat.
Geosynthetics come in a variety of widths and forms and one of the key advances has been the equipment designed to handle these materials from trailer unloading through application. Rolls are attached to special unwinding equipment that is mounted to the rear of a distributor truck or front of a tractor or front-end loader.
Mounque “Monk” Barazone founded the Geotextile Apparatus Co. in 1980 and has been a pioneer in this industry from the time he developed the first pieces of equipment to safely remove fabric rolls from a trailer and unwind them while working on a sewer project in Chicago. He continued to refine this technology and was issued six patents for his applicators. His work continues today with equipment manufacturing sites in California and Ohio and ongoing development work to optimize application of new materials being introduced.
When working with a geosynthetic, it’s important to work with the manufacturer to specify the right material and to ensure correct installation procedures are being used. Some key factors to consider are:
• Surface preparation requirements and environmental conditions for application
• Minimum overlap thickness on longitudinal and transverse joints
• Tack coat application rate.
• Minimum compaction requirements for hot mix overlays
• Whether it can be milled and used as recycled content in future work.
• Repair techniques to correct imperfections during installation
Manufacturer claims vary regarding the extent of benefits when geosynthetics are properly applied. In general, claims are related to:
• Reductions in construction material costs
• Improved reflective and alligator cracking with thinner overlay thicknesses
• Increased service life of the road
• Reduced maintenance costs
In summary, consideration of geosynthetics can be given when designing a paving system for an extended life cycle and reduce total costs. The wide range of geosynthetics on the market can be used throughout the different parts of the paving system from the subgrade through the surface course. Attention should be given to materials that are approved by the governing agency over the project and the manufacturer should be consulted to ensure correct usage and installation.