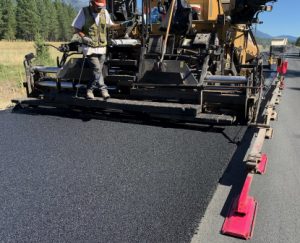
The earliest documented use of asphalt for road building was in 625 B.C. in the Babylonian Empire. Fast-forward to more modern times, in Europe, the first documented asphalt pavements were constructed in the 1830s. In the United States, we have been paving with asphalt since the 1870s. Thus, we are rapidly moving towards our second century of paving asphalt roads that resembles today’s pavements.
The point is that we’ve been doing this for a while. Moreover, we have been doing this well for a long while too. Beginning in 2001, the Asphalt Pavement Alliance has been recognizing long-lasting pavements through their Perpetual Pavement Award. To date,156 such awards have been given to 31 state departments of transportation with an average age of the pavement at the time of awarding of over 46 years. The oldest honored roadway at the time of the award was fully 91 years old! These pavements have performed and continue to perform extremely well.
Yet. despite this ever-growing list of long-life asphalt pavements, we, unfortunately, see examples of premature failures. The questions that commonly get asked when this happens are, “What went wrong?” and “Can it be avoided in the future?” Both are great questions whose answers should be determined to maximize the life of future pavements while minimizing future failures.
In no way do I propose to have all the answers to these questions in a single article. However, I do want to focus on five aspects of asphalt paving that I believe can get overlooked regarding their importance to the performance of a pavement. These five factors are naturally not the only things that should be considered to build high-quality pavements, but overlooking them or doing them poorly will result in poorer-than-optimal performance.
So, what are the five? I’m glad you asked. The five factors that I want to focus on are the mix design, lift thickness versus nominal maximum aggregate size, tack coats, longitudinal joint construction, and inconsistent construction density. Let’s deal with each of these one at a time.
1. THE ASPHALT MIX DESIGN
Every paving project has a mix design. It may be a project specific mix design, or it may be one that is used by the contractor on multiple jobs. Regardless, there are some factors about the mix design that I think we should acknowledge.
First, we commonly refer to the mix design as the “optimum” mix design. When discussing or thinking about the mix design, I think it is wise to ask ourselves, “optimized for whom”?
I think this is a fair question as the owner and the contractor will not likely have the same perspective on what constitutes an optimum design.
From the contractor’s perspective, they want a mix design they can successfully pave to meet the specification requirements of the project’s contract while still allowing them to be cost-competitive in their bidding process. What this tends to lead to are mix designs that maximize their cost-competitiveness, which might mean less binder, especially virgin binder. This isn’t the contractor’s fault. It is one of the ways they get their jobs.
From the owner’s perspective, the optimum design will be the one that is maximized for performance and durability. They try to get such a mix by devising project specifications that are designed to meet the demands of their facility while placing reasonable demands and constraints on potential contractors.
There tends to be a delicate balance between these two legitimate perspectives, typically regarding the amount of virgin binder in the mixture. In support of the case of the owner, more asphalt, to a certain point, can lead to greater durability. For the contractor, getting the job and being profitable means a keen awareness of mixture costs which is strongly impacted by the volume of virgin binder used in the mix. One of the ways to reduce the amount of virgin binder used is for the designer to incorporate recycled asphalt materials in the mix. These are not bad things in and of themselves as we as an industry continue to maintain good environmental stewardship. But as the amount of virgin binder decreases and is replaced by the recycled binder, the designer must properly account for this recycled binder and demonstrate that it is still a quality mix or utilize technology to ensure that they achieve a high-quality, durable product.
The balanced mix design philosophy, which has captured many of our DOTs, is trying to accomplish this – it allows more freedom for mix designers so long as laboratory testing of the mix provides the owner with assurances that it will provide good field performance. With a balanced mix design philosophy, the owner establishes the laboratory testing protocols which gives them the confidence they are buying a quality product. Innovation and performance coexist as the contractor’s mix designers seek ways to give them the cost advantage to generate successful bids and meet the performance testing requirements.
2. LIFT THICKNESS VERSUS NOMINAL MAXIMUM AGGREGATE SIZE
Structural design engineers are the experts on this focused portion of the asphalt world. They utilize a variety of inputs for traffic projections and materials to establish layer thicknesses for a pavement structure. Where thickness design becomes a part of this conversation it is the relationship that exists between a mixture’s gradation and the compacted thickness that is targeted.
While there is more to this conversation than just the nominal maximum aggregate size (NMAS) in a gradation and the compacted lift thickness, this relationship is relatively simple in how it relates to performance. Namely, the two primary goals during construction are density and smoothness. The ability to achieve good density is heavily influenced by the aggregate size/lift thickness relationship. Inadequate thickness for a given NMAS will work against densification. I like to say that the mix needs to have room to wiggle into place and thus densify. When that wiggle room is not present, then the mix fights densification. In more extreme cases fracturing of the aggregates can result. Fracturing leads to uncoated aggregate which can lead to moisture damage. Moreover, since it is harder to densify the mixture, lower density is a real risk compared to a more ideal size to lift thickness ratio.
Much of the discussion on this topic ended for many following the excellent work done by a team from the National Center for Asphalt Technology on NCHRP Project 9-27 (NCHRP Report 531) that explored the relationship between the percentage of air voids, lift thickness and permeability in asphalt pavements. In this work, the research team explored changes in these relationships as lift thickness went from three to five times the NMAS.
Problems can arise from misinterpretation of this work. The largest ratio explored by this research was a 5:1 relationship of lift thickness to NMAS. Many have concluded that this is the largest such ratio that can be successfully constructed and densified. This research did not conclude that! On the contrary, an increasing body of work is showing that very thick lifts can be constructed with excellent density.
3. TACK COATS
I am passionate about tack coats. The reason for this is the very clear relationship between the bonding of pavement layers and performance. Good bonding leads to good performance. Poor bonding leads to poor performance. These statements are not debated. What does get debated is how to achieve a proper bond.
There is way more than can be properly covered in a single article on tack coats, let alone one where tack coats are one of five subtopics. Therefore, my comments are going to be brief for now. At the Asphalt Institute, we maintain an entire webpage on this topic. For more than the following information, please go to asphaltinstitute.org/engineering/tack-coat-information/.
Let me acknowledge that tack coats have been a pain for contractors. They take time to cure which can create difficulties within the paving process and they can track off the surface they are sprayed upon defeating their purpose and frustrating the contractor.
But these are areas that work by many Asphalt Institute members has led to innovations that address both curing time and tracking. Even more traditional materials can be used well. Regardless of the material chosen, complete bonding is needed. To achieve structurally adequate bonding, a uniformly applied application to a clean, dry surface is needed. Enough glue is needed to get a structurally adequate bonding that comes from the residual asphalt. The Asphalt Institute recommends the following residual rates to accomplish this:
Surface Type | Residual Rate (gsy) gallons per square yard |
New Asphalt | 0.020 – 0.045 |
Existing Asphalt | 0.040 – 0.070 |
Milled Surface | 0.040 – 0.080 |
Portland Cement Concrete | 0.030 – 0.050 |
4. LONGITUDINAL JOINTS
Longitudinal joints have been recognized as a potential weak point for asphalt pavements for a long time. This critical location is prone to lower density than the rest of the pavement. A multitude of research has shown that as density decreases, so does pavement life. In fact, for every one percent decrease in pavement density, about ten percent of pavement life is lost. Moreover, data on longitudinal joints indicates that they are commonly two percent or more lower than the rest of the pavements. This suggests they will have at least twenty percent less life than the rest of the pavement.
However, once again there is some very good news for this portion of the pavement. Diligence and technology can reduce or eliminate the typical density falloff at the joint. Reductions in permeability provide great assistance in maintaining consistent life spans for the joint and the rest of the pavement. Void reducing asphalt membranes have a growing positive track record of improving performance. Surface-applied sealers also seem to provide benefits of longer life. Reheating a joint before paving an adjoining pull has also shown significant improvements to joint density. Intelligent compaction technology can also benefit the joint as it helps roller operators apply consistent densification energy to the entire joint.
Given the importance of joint density, the increased investment is small given the improvement in the life of the pavement. Regardless of the technology used, the agency and the contractor should establish a plan for how to build and compact the joint to achieve the desired specification.
5. INCONSISTENT DENSITY
As was just stated in the last section, losing density is very harmful to a pavement’s life. Density is the single most important construction factor when it comes to pavement durability. Increasingly, agencies are seeking higher density minimums than were historically sought. They are doing this seeking greater life with less maintenance. This is good for our industry. But if the density isn’t consistent then performance will also be inconsistent.
Therefore, a key to consistent performance is consistent density. Consistent density is achieved by consistently placing the mix so that it isn’t segregated either physically or thermally and by having roller operations uniformly densify the mat. This is one of the most noteworthy benefits of intelligent compaction. Roller pass mapping with pass counts in intelligent compaction is a very good means of helping a contractor get consistent densification energy into the asphalt.
Advanced technology is also coming into play with this factor. Namely, ground-penetrating radar (GPR) is increasingly finding acceptance within DOTs. Alaska and Minnesota are two examples of states that now have significant histories with this technology. Moreover, AASHTO now has a provisional specification for the use of GPR: PP 98-19. In short, GPR technology allows the scanning of the freshly rolled mat while it is still warm. If potentially low-density spots are found, there is the opportunity to apply corrective action and thus bring the density up.
WRAPPING IT UP
Many factors come together when a pavement is constructed. More factors than the five discussed in this article are important to the construction of a future Perpetual Pavement Award-winning road.
A well-thought-out mix design that is optimized for both performance and bid-strength can be achieved while also allowing for mixture innovation. Building a pavement that allows for good construction densification by being adequately thick for the gradation used will greatly assist in achieving excellent density. Building a structurally sufficient bond between any and all of the pavement layers via good tack coating practices is yet another key to performance. Paying attention to the longitudinal joint including giving due consideration to newer technology helps minimize this suspect location from being a problem long-term. And similarly, working to achieve highly consistent density across the mat will also pay dividends for long-term performance.
The asphalt industry has done a great job building and maintaining reliable and cost-effective pavements. Paying attention to all of the factors that produce these assets is good for our economy and our environment.
Johnson is an Asphalt Institute Senior Regional Engineer based in Montana.