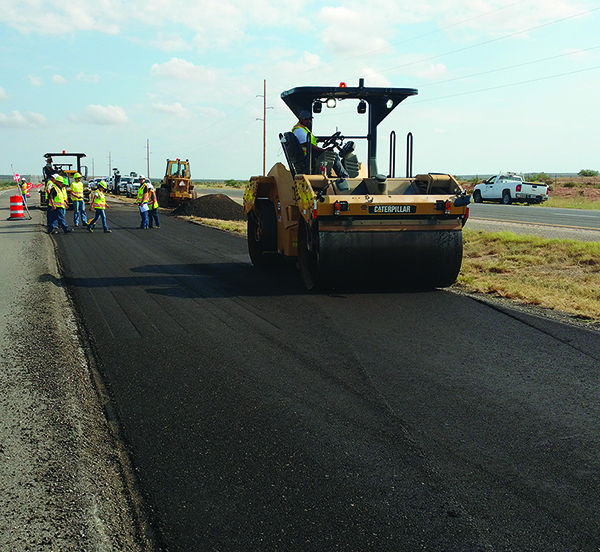
Based on positive responses from past events, a third International and Western States In-Place Recycling Conference was held in conjunction with the Rocky Mountain Asphalt User/Producer Group’s Annual Meeting in the fall of 2018.
One of the presentations at this event was made by James Gallegos, New Mexico Department of Transportation (NMDOT) Materials Engineer, on a cold in-place recycling (referred to as cold in-situ recycling in New Mexico) project on U.S. Highway 285 in southeast New Mexico. This project is an example of the information from those past conferences reaching the project level.
New Mexico’s history with cold in-place recycling
The state of New Mexico has a long history of cold in-place recycling (CIR) beginning in the early 1980s. Until 2000, CIR projects were commonplace in New Mexico with over 150 total or about 10 annually. These historical projects were 100 percent reclaimed asphalt pavement (RAP) with a milling depth between 2- 5 inches. Four inches was the most common depth, to which an overlay was applied. Following AASHTO thickness design procedures, a layer coefficient of 0.35 was assigned to the recycled layers. A minimum of 15 years of service was expected from these sections.
R. Gordon McKeen published an evaluation of 45 of these projects in 1996. Very favorable results were reported in terms of construction and maintenance costs, environmental impacts, and most importantly performance compared to both mill and inlays as well as simple overlays. Yet, despite this very positive history, only sporadic use of CIR has occurred in New Mexico since 2000.
A re-recognition of the positive history of CIR occurred within NMDOT after a 2014 conference. A committee was formed of NMDOT and industry personnel with the stated goal of developing a special provision for future CIR projects.
The special provision “Cold In-situ Recycling (CIR) of Existing Surfacing – Section 415-A” was produced and subsequently approved in 2017 by NMDOT. Transition to a standard specification was accomplished in the “2019 Standard Specifications for Highway and Bridge Construction.”
Key items of the Section 415-A
A laboratory mix design was submitted to the NMDOT by the project contractor for CIR projects. Some of the crucial items that must be included in this mix design are as follows.
NMDOT requirements for this design include that specimens be compacted utilizing a Superpave gyratory compactor (SGC) using 6-inch diameter molds with a compactive effort of thirty (30) gyrations. The gradation of the millings shall all pass an inch and a quarter sieve, and the resulting gradation shall be determined as per AASHTO T11 and T27 procedures. The mixture is required to have a minimum of 45 psi (310 kPa) indirect tensile strength as tested under AASHTO T283, modified to exclude the freeze cycle. Conditioned specimens are soaked in a water bath at 77±2°F for 24 hours. The minimum tensile strength ratio is established at 0.70. A raveling test is required according to ASTM D7196 with a maximum of 2.0 percent loss. Good coating of the RAP as per AASHTO T59 shall also be determined. Bulk specific gravity, maximum theoretical specific gravity and laboratory air voids are determined utilizing AASHTO T331, AASHTO T209 and AASHTO T269. These values are for information only during the design development. A recycling agent is required with the option to use either portland cement concrete or lime slurry as a substitute.
An optimized emulsion content is determined based on an initial dosage from a balance of these properties (indirect tensile strength, tensile strength ratio, raveling test and RAP coating test) and a 1,500-foot field test strip. Other items determined by the test strip include the roller pattern and the target density as defined by the number of passes where density is maximized in the wet material. This target density shall then be achieved ±3%. Careful control of the milling depth and the addition of water and recycling additive during mixing are required.
Five pay items have been established for CIR projects in New Mexico. Two items, area milled for CIR and any areas of CIR that need repairs, are paid for based on square yardage. Three items, the recycling and sealing emulsions as well as the recycling additive, are paid for based on the tonnage used.
U.S. Highway 285
In 2018, the NMDOT contracted with Fisher Sand and Gravel – NM Inc. to employ CIR technology to over 11 miles of U.S. Highway 285 north of Roswell, New Mexico. Only the southbound lanes were a part of this project.
The average annual daily traffic is about 3,500 vehicles with a design equivalent single axle loading of over 4.5 million. CIR was selected for this project as it offered a solution that would meet the structural needs of the roadway while minimizing the opportunity for reflective cracking due to having most of the existing cracks obliterated by the recycling process.
Site evaluation of the section included the collection of a total of 41 cores, approximately one every 1/4-mile. These were measured for their thickness and evaluated for stripping, air voids, the mixture type, delamination/tack coat and the asphalt was recovered for further testing. Core thicknesses ranged from about 7.5 to 12 inches of total asphalt. Twenty-one of the cores showed moisture damage. Cracks that were cored showed mid to full-depth cracking. A visual distress survey was also performed which identified transverse, longitudinal and isolated areas of block and alligator cracking.
The final design cross-section was set as a 4-inch CIR section, overlayed with 3.5 inches of Superpave III mix with a PG 70-28 binder, topped with a 5/8-inch rubberized open-graded friction course with a PG 70-28R+ binder. Workers milled and removed 3-1/8 inches of existing pavement prior to the recycling process. This value was adjusted subsequently in the field to two inches due to thinner than expected locations.
Coughlin Company served as a subcontractor to Fisher for the CIR portion of the project. HollyFrontier supplied the CIR emulsion. Three percent by total weight of mix of CIR emulsion with a base grade of PG 64-22 was recommended by the approved mix design. It was anticipated that 2.0 percent water and 0.75 percent of Type IV cement recycling agent would be added as well. No field changes to mix design were needed as the test section went well.
The CIR section was subsequently placed by Coughlin and properly compacted. The compaction train for the CIR consisted of two 14-ton double-drum steel wheel rollers for initial breakdown, followed by two 16-ton pneumatic rollers in the intermediate position and a 14-ton double-drum steel wheel roller operating in static mode for the finish rolling. The rolling pattern established was: breakdown – four passes, intermediate – eight passes, and finish – one pass. The rolling pattern remained relatively unchanged throughout the project and the average density obtained was 99 percent of the test strip density. The tack coat material was a SS 1H emulsion diluted 50/50 and applied at a rate of 0.10 gallons/square yard and allowed to break prior to paving with the Superpave III. The paving process went very well and no issues were noted. Substantial project completion was October 2018 and project closeout occurred in November. In terms of costs, the CIR amounted to about 30 percent of the total paving cost or about 18 percent of the cost of the total project.
CIR future in New Mexico
The return of CIR technology adds one more outstanding tool in MNDOT’s arsenal for the maintenance/rehabilitation of their asphalt pavements. Excellent historical experiences with this technology as well as wise recognition of recent improvements have NMDOT looking to once again use CIR more frequently.
Currently, there are several CIR projects scheduled for the 2019 and 2020 seasons. The rebirth of CIR in New Mexico is destined to prove itself once again in the Land of Enchantment as it did in the 1980s and 1990s. Welcome back!
Gallegos is a Materials Engineer for NMDOT. Johnson is an Asphalt Institute Senior Regional Engineer based in Montana.
A 2016 “Asphalt” magazine article on the state of in-place pavement recycling contained information on the history of asphalt pavement recycling, current in-place recycling technologies and a summary of a 2014 international conference on the subject. Read it here.