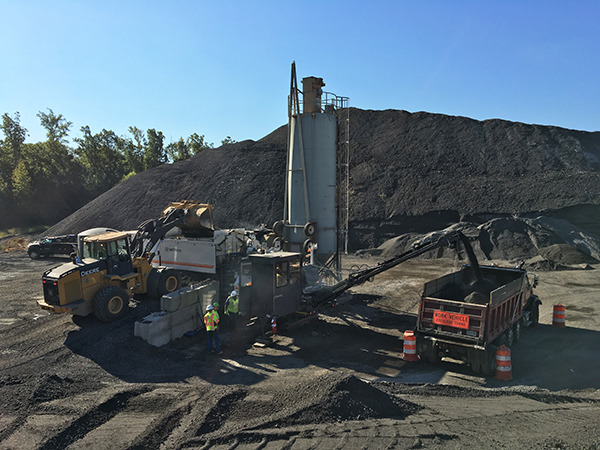
The primary source of reclaimed asphalt pavement (RAP) is existing asphalt pavement that has been removed from the roadway using cold milling equipment and then stockpiled for later use. The Virginia Department of Transportation (VDOT) uses milling as a major component of its asphalt pavement rehabilitation strategy.
For the past two years (2018 and 2019), VDOT awarded contracts totaling more than 2.6 million square yards of asphalt pavement milling each year. Even though VDOT allows the use of high percentages of RAP to be incorporated during the production of new asphalt mixtures (averaging 26.5 percent in a recent NAPA survey), the quantity of stockpiled RAP is too much to be used in conventional hot plant mixture applications alone. Much of what is not included in new mixtures remains stockpiled at contractor facilities.
It has been estimated that contractors have more than 10 million tons of stockpiled RAP in Virginia with the majority of large RAP stockpiles in or near urban areas around the state. Some individual stockpiles exceed several hundred thousand tons of RAP.
Even though RAP is a valuable source of aggregate and binder that can be reused to replace virgin materials (resulting in significant cost savings), contractors are faced with a dilemma of how to manage ever-growing RAP stockpiles.
VDOT and the asphalt paving industry have worked together to address the issue by using cold central plant recycling (CCPR) to create pavement structures containing high percentages of RAP from existing stockpiles or from RAP that is removed from and then returned to the same project. Both VDOT and the Virginia Asphalt Association (VAA) have been pleased with the results of several large projects that have been completed using CCPR around the state in recent years.
“Through the use of this asphalt mix on a number of high-profile, high-volume interstate roadway applications, cold central plant recycling material is proven to be a well-performing, sustainable and cost-effective pavement material for Virginia,” says David Lee, VAA Vice President.
“Given Virginia’s continued RAP storage issues and the industry’s commitment to environmental stewardship, usage of this material will only grow,” Lee added.
During the last eight years, VDOT has contracted for the placement of nearly 550,000 tons of CCPR.
What is Cold Central Plant Recycling?
CCPR is the process in which a bound pavement layer is produced at a centrally-located mobile plant using RAP from an existing stockpile or millings from an ongoing project, either emulsified asphalt or foamed asphalt and sometimes an active filler such as cement. Processing the RAP materials may be as simple as screening the RAP to remove oversized chunks or it could include crushing, screening and fractionation to create separate coarse and fine RAP stockpiles. After production, the CCPR material is loaded onto trucks and hauled to the project for placement using conventional paving and compaction equipment.
There are a number of advantages for using CCPR compared to non-recycling approaches:
• 20-50 percent reductions in cost compared to conventional hot plant recycled mixtures due to reduced virgin materials and hauling costs
• As much as 50 percent reduction of greenhouse emissions
• Reduction of the size of existing RAP stockpiles
I-81 near Staunton
In 2011, VDOT awarded a contract to reconstruct a portion of southbound I-81 near Staunton using pavement recycling techniques. This two-lane section of interstate carries more than 7,000 trucks per day. The right lane was rebuilt using two pavement recycling techniques: full-depth reclamation (FDR) and CCPR.
FDR is used to produce a stabilized foundation by combining the upper portion of the subgrade, the aggregate base and the bottom of the existing asphalt layers into a blended material. The CCPR was produced using two percent foamed asphalt and one percent cement. Structural testing soon after construction showed that the structural layer coefficient for CCPR was only slightly less than that for asphalt mixtures.
Since 2011, performance monitoring by VDOT has shown that the combination of CCPR and FDR has worked well on a high truck volume roadway. The international roughness index (IRI) of the right lane has remained at less than 45 inches/mile and rut depths are only about 0.1 inches over the last nine years.
NCAT Test Track sections
Following the successful completion of the I-81 project, VDOT sponsored the construction of three test sections in 2012 at the National Center for Asphalt Technology (NCAT) Test Track that included CCPR.
Two sections included CCPR over an aggregate base while a third included CCPR over an FDR foundation (Section S12) and under an AC layer. A TRB paper published by David Timm, Brian Diefenderfer and Benjamin Bowers in 2016 showed that even after 20 million equivalent single axle loads (ESALs), the test sections were all performing well as evidenced by no observable cracking at the pavement surface. Specifically, Section S12 (containing both CCPR and FDR) had longitudinal strain values so low, the authors stated the test section was behaving like a perpetual pavement.
“Overall, the three VDOT sections on the NCAT Test Track performed well with no surface cracking and very little rutting after heavy trafficking. This is an encouraging sign that the use of CCPR (along with high-quality surface mixes like stone matrix asphalt (SMA) can be used successfully by VDOT on high volume, heavily loaded roadways,” said Dr. David Timm of NCAT.
I-64 project
In 2017, VDOT awarded a construction contract to widen and rebuild both directions of a portion of I-64 near Williamsburg. Different pavement cross-sections were used on the original I-81 project and the NCAT test sections. Experience and findings from research helped VDOT optimize the structural design for the I-64 project.
The work on this 7.1-mile portion of the interstate (known as Segment II, the second of a three-part corridor widening/rehabilitation sequence) began with adding a travel lane and a new left shoulder that included a cement-stabilized foundation and CCPR.
After adding these two new lanes, the traffic was shifted to them and the existing pavement was reconstructed. The reconstruction was accomplished by removing the old deteriorated jointed concrete pavement.
Next, the existing foundation was reclaimed using an FDR process and then CCPR was added using a design similar to the widened lanes. The CCPR material was made from 85 percent RAP from existing stockpiles and 15% #10 crushed virgin aggregate which was needed to improve the gradation of the mix. Foamed asphalt and Portland cement, at quantities of 2.5 and 1 percent respectively, were used to produce the CCPR.
The CCPR plant was located adjacent to the contractor’s asphalt plant and had its own stockpile of RAP that was processed so that 100 percent of the material passed the 1-inch sieve. The CCPR plant was fed using a front-end loader where hoppers were filled with RAP and #10 virgin aggregate. The CCPR plant used internal weighing processes to meter the correct quantities of RAP, #10s, foamed asphalt and cement. The CCPR material was produced at a rate of about 200 tons per hour. After production, the CCPR material was directly discharged into dump trucks for hauling to the project. The haul distance was approximately 35 miles.
The design thickness of CCPR was six inches. To achieve this, the loose CCPR was placed at approximately 7.25 inches, with depth checks performed daily to confirm thickness. The CCPR was placed using a conventional paver screed (the screed was not heated). The required density (98 percent of the mix design density), verified by a daily modified Proctor test, was achieved with approximately 8 passes of a double steel drum. Density testing was completed using a nuclear density gauge operated in the direct transmission mode.
The decision on when to place the first layer of surface mixture on the CCPR was made primarily on achieving a reduction to 50 percent of the optimum moisture content. The CCPR layer was usually ready after a few days. The timing was such that several days of CCPR production could be surfaced with the first lift of SMA at once. The final surfacing layer of SMA was then placed. Generally, the contractor found that the required density on the SMA placed on top of the CCPR was easier to achieve due to the stiff foundation from the underlying CCPR layer.
“The CCPR product is a very efficient use of RAP and with over 155,000 tons placed on I-64 Segment II and another 65,000 tons placed so far this year on I-64 Segment III with no issues. The use of CCPR provides a way for contractors to reduce the RAP stockpiles and a cost-efficient method of construction that uses recycled material,” said Craig Rayfield, QC Manager for Allan Myers.
With one segment of I-64 widening projects completed and work on the second segment during the 2020 construction season underway, cost comparisons suggest that the use of CCPR (in conjunction with the use of the 12-inch thick FDR layer) will result in an approximately 35 percent reduction in cost resulting in approximately $15 million in savings when compared to a structurally equivalent non-recycling structural design.
The takeaway: Using the cold central plant recycling process that produces asphalt bases containing high percentages of stockpiled RAP has been a success for VDOT, asphalt pavement contractors and Virginia taxpayers.
Diefenderfer is a Principal Research Scientist at Virginia Transportation Research Council.
Horan is an Asphalt Institute Senior Regional Engineer based in Virginia.