In March 2019, the Asphalt Institute (AI) released its industry average life cycle assessment (LCA) report on asphalt binder produced in North America. The study was conducted by Thinkstep AG, an international consulting firm well-known for its expertise in sustainability and life cycle assessment.
Not to be confused with life cycle cost analysis (LCCA) that only examines costs, LCA is a science-based method to quantify the environmental impacts of products, accounting for burdens throughout the supply chain of a given product. LCA is governed by international standards ISO 14040 and 14044.
Background
Driven by green building standards (e.g., LEED, Living Building Challenge, IgCC) and other initiatives, the demand for accurate life cycle inventory (LCI) and life cycle impact assessment (LCIA) data has increased for products used in the construction sector, including pavement. Transportation agencies, such as the Illinois Toll Road Authority and the California Transportation Department, are starting to look at how they can use such information in their project plans and designs.
Therefore, the Asphalt Institute undertook this project to ensure the published LCI data on asphalt binder is as accurate as possible and representative of North American industry conditions. Along with aggregate, asphalt binder is the major component of asphalt mixtures.
The National Asphalt Pavement Association (NAPA) has an Environmental Product Declaration (EPD) program for asphalt mixtures (asphaltpavement.org/EPD). The declared unit and reported impact categories in AI’s study align with NAPA’s EPD program and associated Product Category Rules (PCR). NAPA plans to incorporate the new AI LCI datasets into their EPD.
Scope
The scope of the study was cradle-to-gate: including raw material sourcing and extraction, transportation to refineries, refining of crude oil into asphalt, transport to the terminal, and final blending of the asphalt binders at the terminal. Only those refinery processes associated with asphalt production were included in the assessment.
The final result is publicly available LCI datasets for four asphalt binder products:
• without any additives
• with 3.5 percent styrene-butadiene-styrene (SBS)
• with 8 percent ground tire rubber (GTR) blended at the terminal
• with 0.5 percent polyphosphoric acid (PPA).
Information was collected from twelve AI-member refineries (from nine companies) and eleven terminals (from four companies) in the U.S. and Canada for 2015 and 2016. The data represented 27 percent of annual production in the U.S. and Canada for 2016. Geographical and technical representativeness was assessed and considered to be good.
Allocation
Since asphalt is only one product stream in a complex multi-product system (refinery), it is crucial that the allocation methodology appropriately captures only that share of the total impacts of the system that can be attributed to the asphalt binder. For this study, the main material and energy inputs that needed to be allocated were crude oil input, thermal energy consumption (including associated emissions) and electricity.
Mass allocation was selected for the electricity because the density of products is directly related to the electrical demand for pumping the products. Energy content of the co-products (using the net calorific value a.k.a. lower heating value) was selected as the allocation methodology for crude oil input, as it accounts for the fact that the majority of co-products are used as fuels. The thermal energy demand for asphalt production was calculated based on the sensible heat of asphalt in the system, i.e., based on the temperature differential between the crude tank and the asphalt going to storage in combination with the specific heat capacity of the asphalt.
Finally, the total direct emissions of thermal energy production were allocated based on the ratio of thermal energy use (excluding recovered heat) calculated for asphalt production and the refinery’s total thermal energy consumption during asphalt runs only.
Crude oil slate
The production stage starts with the extraction of crude oil and delivery to the refinery. Crude oil was modeled based on Thinkstep’s crude oil supply model, which considers the whole supply chain of crude oil (i.e., extraction, production, processing, the long-distance transport and the regional distribution to the refinery) and forms the basis of all refinery product inventories in their GaBi databases.
Companies were asked to provide crude name, the region of origin, extraction technology and mode of transportation. In many cases, primary information on the extraction technology was not available, in which case it was selected and modeled based on the crude name. When the name alone did not provide enough information to select an extraction technology, it was modeled using the region of origin’s average crude slate mix as a proxy.
The resulting average crude oil slate for North American asphalt binder was used and represents a mix of conventional (primary, secondary and tertiary production) and unconventional (oil sands, in-situ) extraction technologies (Table 1).
AI member’s asphalt binder products are manufactured in Canada and the United States, with 85 percent of crude oil sourced from those nations.
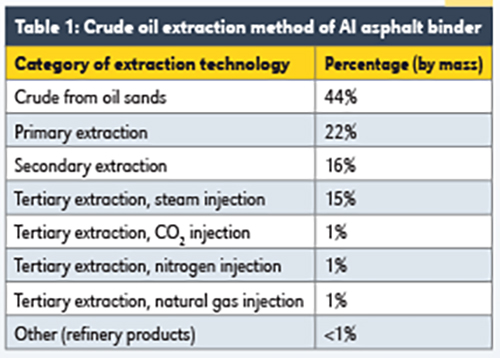
Asphalt production
Crude oil refinery activities begin with the input of crude oil. Crude is fed to the desalter where it is partially heated and mixed with water to dissolve salts. The water is separated and removed. The crude oil then enters the atmospheric distillation unit, where it is heated and distilled. All products lighter than heavy gas oil vaporize and the energy required for vaporization is fully attributable to those lighter products. The residue from the atmospheric distillation is introduced to the vacuum distillation unit. The atmospheric residue is heated and further distilled under a vacuum, vaporizing all gas oils and any remaining diesel, with asphalt remaining as a hot liquid in the bottom of the vacuum distillation tower.
The hot asphalt passes through heat exchangers alongside other refinery feeds, mostly in the crude and vacuum distillation units, to return heat to the process, before going to asphalt storage.
While process-specific electricity, thermal energy, water usage and emissions would have been preferred, these data points were not available. Therefore, refinery-level data were collected for site-wide consumption of electricity, thermal energy, and water as well as direct emissions and allocated to the asphalt product as described earlier.
Asphalt terminal
The processes within each refinery were vertically aggregated first and then combined into one production-weighted average. This average asphalt production process then provided the input of asphalt to the average terminal process.
At the asphalt terminal, hot liquid asphalt is stored, additives (GTR, SBS, or PPA) are mixed or milled into the asphalt, and the asphalt is then stored. The terminals consume electricity (mainly used for milling) and thermal energy (used for storage). Terminals can be either co-located with the refinery or off-site. For the study, all participating companies were located off-site. Inbound transportation from the refinery to the terminal is a production weighted average of the distances and modes collected from the companies.
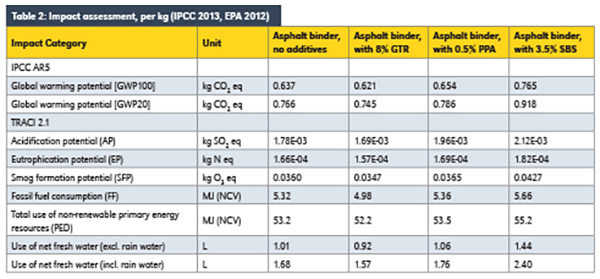
Results
The reported impact categories represent impact potentials, i.e., they are approximations of environmental impacts that could occur if the emissions (a) followed the underlying impact pathway and (b) met certain conditions in the receiving environment while doing so. In addition, the inventory only captures that fraction of the total environmental load that corresponds to the chosen functional unit (relative approach). Results are therefore relative expressions only and do not predict actual impacts, the exceeding of thresholds, safety margins, or risks. Table 2 presents the total cradle-to-gate environmental impact results for all four products.
Figure 1 presents the relative results of asphalt without additives leaving the terminal, broken down by crude oil extraction and transport refinery operations, and terminal operations (including transport to the terminal).
A critical review of the completed study report was conducted by a panel of three outside experts. Their findings were that:
• the approach, described in the report, used to carry out the LCA is consistent with the ISO 14040:2006 principles and framework and the ISO 14044:2006 requirements and guidelines,
• the methods used in the LCA are scientifically and technically valid as much as the peer-reviewers were able to determine without having access to the LCA model and the data collection information,
• the interpretations of the results reflect the limitations identified in the goals of the study, and
• the report is transparent concerning the study steps and consistent for the purposes of the stated goals of the study.
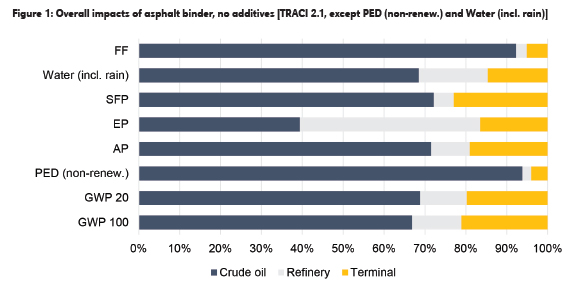
Conclusions
The extraction of the crude oil is the primary driver of all potential environmental impacts, due most significantly to the use of crude oil from oil sands or crudes extracted via a tertiary method. At the refinery itself, electricity is the most significant single driver of impact followed by on-site thermal energy generation and associated direct emissions. Terminal operations can contribute up to 20 percent of potential environmental impacts without additives, driven primary by thermal energy and inbound transport of the asphalt.
This study achieved its goals in creating an LCI that fairly represents the asphalt binder industry in North America. By combining the primary data collected from participants with the secondary data available through the Gabi database, the Asphalt Institute and Thinkstep have created the most accurate and representative LCI data for the region available at the time of the report publication. Updates to these datasets are expected on a periodic basis.
Dr. Buncher is the Director of Engineering for the Asphalt Institute.
References
ISO. 2006. ISO 14040: Environmental management – Life cycle assessment – Principles and framework. Geneva: International Organization for Standardization.
ISO. 2006. ISO 14044: Environmental management – Life cycle assessment – Requirements and guidelines. Geneva: International Organization for Standardization.
EPA. 2012. Tool for the Reduction and Assessment of Chemical and other Environmental Impacts (TRACI) – User’s Manual. Washington, D.C.: U.S. EPA. https://www.epa.gov/chemical-research/tool-reduction-and-assessment-chemicals-and-other-environmental-impacts-traci.
IPCC. 2013. Climate Change 2013: The Physical Science Basis. Genf, Schweiz: IPCC.
More information on AI’s LCA Study, including the final report and LCI datasets, are available at asphaltinstitute.org/engineering/lca-study-on-asphalt-binders/