Planning is imperative for any type of successful asphalt paving project. When it comes to defining a successful asphalt project, success can be measured not only by the feasibility and execution of the project but also by the long-term performance of the pavement constructed.
Pavement performance often is measured based on smoothness and overall condition. We offer these five rules of thumb in the planning and construction of an asphalt paving project to help maximize pavement smoothness and life.
1.
Each new lift improves smoothness by about 50 percent.
One of the great benefits of asphalt pavements is their inherent smoothness. No matter how well a pavement is designed and built, no matter how long that pavement lasts, roadway users will tend to call it “good” or “bad” based on the smoothness of the ride. Smooth pavements are simply more comfortable and safer to drive on. Additionally, engineers want smoothness because they know it saves money on fuel and maintenance costs for all classes of vehicles, benefiting every taxpayer. Smooth pavements require good workmanship and are facilitated by well-written specifications.
One of the main reasons for the inherent smoothness of asphalt pavements is the design of asphalt pavers. They consist of a tractor unit that provides mobility, and powers all the paver components, and a screed, which is basically a flat, heavy metal plate that establishes the pre-compacted thickness of the mat, provides some initial compaction uniformly across the entire width of the mat and produces a smooth texture and level surface. The “free-floating” screed uses a self-leveling action that produces smoothness in the mat. The screed is attached to the tractor unit at tow points on each side. These act as a hinge to allow the screed to float freely across the surface of the mat. This action averages out changes in the existing grade, resulting in a smoother surface in the new mat.
How much smoother? Our first rule of thumb says that, on average, the new mat is about 50 percent smoother than the surface upon which it is placed. More lifts tend to result in a smoother surface. The increase in smoothness will typically diminish with each lift, i.e., the first lift may increase the smoothness to around 75 percent, the second around 50 percent, the third around 30 percent, etc. As with many aspects of asphalt paving, this is one of several parameters that are interrelated. Specifying lift thicknesses that are too thin simply to create more lifts can be counterproductive to mat density, which brings us to our next rule of thumb.
2.
Asphalt lift thickness should be a minimum of four times the NMAS of the aggregate.
Obtaining proper roadway compaction is probably the most important operation in the paving process to achieve long-lasting pavements. The compaction process reduces air voids in the asphalt mat by reorienting the aggregate particles in the mix to pack more tightly together. However, if the size of the aggregate particles is too large relative to the mat thickness, it will be more difficult to achieve the required density without damaging the aggregate.
For dense-graded mixtures, the Asphalt Institute recommends a minimum lift thickness of four times the nominal maximum aggregate size (NMAS) of the mix. For mixes that are more finely graded, mat density can still be achieved with lifts that are a minimum of three times the NMAS. Superpave defines the NMAS as one sieve size larger than the first sieve to retain more than 10 percent of the aggregate. Superpave mixes are typically specified by their NMAS and binder grade, e.g., ½” NMAS with PG 64-22.
Therefore, the minimum lift thickness to facilitate mat density for a typical ½” (12.5 mm) NMAS Superpave mix would be 2”. A ½” NMAS mix that was on the fine side of the gradation would typically still work at a 1-½” lift thickness.
For many, the thought of making lift thicknesses too large might bring a concern about inadequate compaction throughout the lift. However, our industry colleagues at the National Center for Asphalt Technology (NCAT) have been doing some interesting work with thick lift paving for the South Carolina DOT (SCDOT). On the NCAT test track, good compaction was still achieved on pavements using up to 8” lifts. Thick-lift paving may be especially helpful in night paving where it is more difficult to keep the mix hot and where lane-closure time is a premium.
It should be remembered that changes in many asphalt parameters influence others. We mentioned earlier that attempting too many lifts to optimize smoothness may be detrimental to mat density. Conversely, thick lift paving could also be detrimental to mat smoothness.
3.
The typical application spread rate for asphalt mixtures is 110 lbs. per square yard per inch of thickness.
Now that the number of lifts and the size of the mixtures for a project are identified, it is critical to develop planned quantities based on the area that is going to be paved. Getting quantities accurately calculated and published in bidding documents is important in the planning and budgeting for a given project. A good rule of thumb to help establish the total amount of tonnage needed is to use a spread rate of 110 pounds per square yard per inch. To understand how this rule of thumb is applied, see the following example.
A project is planned for two lifts of asphalt mixture on two miles of pavement that is 24 feet wide. The cross-section will consist of 2.5 inches of a ½” NMAS intermediate lift and 1.5 inches of a 3/8” HMA surface mix. How much total tonnage of each mix should be estimated to be used for the project?
Equation 1 can be used to calculate the total tons.

For this example, let’s start with the calculation of project area. The project area equals two miles in length and a width of 24 feet. Converting the area into square yards is shown in the following:

Apply Equation 1 now that the total area is calculated, the total tons of intermediate mix placed at 2.5 inches can be calculated:

Likewise, the total number of surface HMA tons for the example project would be:

It is important to understand if any local variations exist in the rule of thumb. For example, the Illinois Department of Transportation uses a spread rate of 112 pounds per square yard per inch of thickness. The Tennessee DOT (TDOT) primarily uses a spread rate of 106 pounds per square yard per inch of thickness as the yield rate for a majority of their dense-graded asphalt mixtures.
Another item to be mindful of is the practicality of the rule of thumb when specialty-type mixtures are used. For example, in their specifications, INDOT uses a Material Adjustment Factor (MAF) to account for variations in the weight of a given mix versus planned quantities and laydown rate. This is typically applied to steel slag Stone Matrix Asphalt (SMA) mixtures where the higher specific gravity of the steel slag particles drives the overall weight of the mixtures to be higher, however, it can also be applied to traditional dense-graded mixtures. The increased unit weight of the mix (based on the maximum specific gravity of the mixture) requires an adjustment so that thickness and quantities are not compromised. For more information on how this practice is specified, please refer to INDOT’s 2020 Construction Specification section 401.05.
The opposite effect can also be applied to mixtures that would have a lower yield. In open-graded friction courses (OGFC) or open-graded drainage layers, air voids could be in the 15 to 20 percent range. This results in a mixture with a lower unit weight and lower resulting yield. For example, TDOT uses a spread rate of 88 pounds per square yard inch for their OGFC mixtures to reflect the higher air void content. INDOT uses 100 pounds per square yard inch in practice to reflect the higher air void mixtures of its open-graded drainage layers.
4.
Set the screed height 1.25 times the final planned compacted thickness.
Have you ever wondered how the paving crew sets the screed height to achieve the planned final thickness while also obtaining sufficient density? During the laydown process, the asphalt mixture undergoes a minimal amount of compaction from the vibratory screed. The mix is struck off in an uncompacted or loose state. There needs to be enough material placed in the loose state to allow for mix consolidation during the compaction process to achieve the specified density, while simultaneously attaining the desired final compaction thickness. To achieve this balance, the paving crew typically uses the rule of thumb to add 25 percent of the final compacted thicknesses to set the screed height.
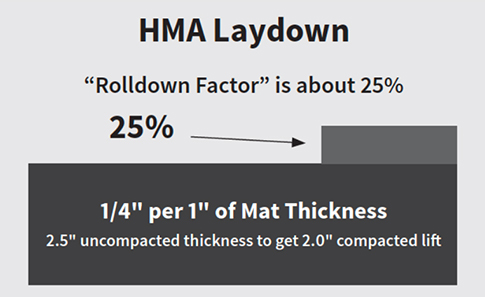
Typical Roll Down Factor
In other words, the crew can multiply the final compacted thickness by 1.25 to calculate and set the screed height. Table 1 shows a range of set screed heights based on typical compacted lift thicknesses used.
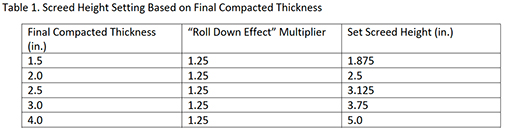
Like the previous section, roll down rates are different for open graded mixtures. When gap graded or open graded materials are being placed, a roll down factor of 15 percent is more accurate.
5.
Each extra one percent density results in 10 percent extra service life.
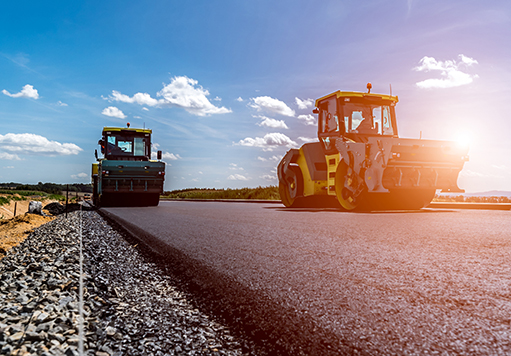
Mat density is firmly correlated to pavement longevity. As part of the Federal Highway Administration’s (FHWA) Asphalt Pavement Technology Program strategic direction on extending pavement service life through enhanced field compaction, NCAT conducted a literature review (NCAT Report 16-02, Enhanced Compaction to Improve Durability and Extend Pavement Service Life: A Literature Review). Decreasing in-place air voids in the asphalt mat was shown to have several benefits.
As noted, many asphalt mixture characteristics are interrelated. Things that improve one characteristic often diminish another. For example, adding extra binder tends to increase fatigue resistance, but can decrease the mix’s rut resistance. However, increased compaction density is something that helps both fatigue and rut resistance. NCAT reported that an extra one percent mat density was estimated to improve fatigue performance by at least 8.2 percent, and all the way up to 43.8 percent. Additionally, that same one percent increase in mat density improved rut resistance by up to 66.3 percent. Overall, the rule of thumb is that an extra one percent mat density conservatively results in 10 percent extra service life.
An extra one percent mat density is achievable. There are a host of considerations that can facilitate achieving this goal. Agencies can promote higher density through their materials, construction and quality assurance specifications. For example, finer gradations are inherently less permeable and more compactable. Specifying or even just allowing warm mix asphalt (WMA) tends to make it easier to achieve higher density in the field. Also, many states are implementing or researching ways to increase in-place mat density. As part of FHWA’s in-place pavement density program, 26 states participated in 29 demonstration projects to determine if it would be possible to obtain at least one percent increase in in-place pavement density. Most were successful using a variety of tactics.
Other agency specifications relating to:
• base density requirements
• lift thickness vs. NMAS
• minimum laydown temperature, and
• requirements related to ambient conditions for paving
are all items in which uniform requirements for all contractors can even the playing field and promote higher mat density. Each of these is beyond the control of the contractor’s roller operator and cannot be addressed by compaction best practices alone.
As one might expect, there are several best practices that are within the control of the contractor and roller operator and may not be addressed fully by agency specifications. The contractor can select the number and type of rollers necessary to facilitate good compaction. The roller operator can select the number of passes, sequencing, and roller speed that will optimize mat density. The paver operator can choose to limit the paver speed so that the rollers are not left behind, causing the uncompacted mix between the rollers and the paver to cool and make compaction more difficult.
Smoothness and density are good indicators of long-term project performance. Calculating asphalt mix yield and ensuring the final desired thicknesses are important metrics in the field to be communicated between the contractor and agency to ensure there are no overruns or underruns on planned quantities. Ensuring that sufficient asphalt lift thickness is achieved while obtaining sufficient density maximizes the opportunity for the pavement to perform structurally and functionally as planned by the agency.
Planning for the next successful project
Using these rules of thumb during the planning and paving processes can be helpful in achieving the desirable goal of building sustainable, smooth and high-performing asphalt pavements.
Gierhart is the Asphalt Institute Deputy Director of Engineering based in Oklahoma.
Wielinski is an Asphalt Institute Regional Engineer based in Ohio.