An agency perspective
Cold in-place recycling (CIR) is a pavement rehabilitation process in which a distressed asphalt pavement is milled to a specified depth, the reclaimed asphalt pavement (RAP) is pulverized and mixed with a stabilizing agent (emulsified or foamed asphalt) and the resulting recycled material is paved and compacted across the roadway.
A CIR “train” of equipment is typically comprised of a water tanker, an asphalt tanker, a recycling unit, a paver and rollers. The old pavement is essentially repaved without ever leaving the roadway. This eliminates the amount of construction traffic removing old materials and delivering new paving materials to the job site.
Throughout the entire process, there is no heat applied to the material – another environmentally friendly benefit compared to traditional processes. CIR is typically covered with a single or multiple-lift asphalt mixture when completed. In low-volume applications, a chip seal or cape seal is often used as a final surface layer. The CIR process is a proven technology used on all types of pavements, including rural highways, urban city streets and even high-volume interstates.
John Senger has been the Engineer of Pavement Technology for the Illinois Department of Transportation (IDOT) since 2016. Among Senger’s numerous responsibilities, he provides pavement design, rehabilitation and preservation strategy support to the district and central office engineers and reviews and updates pavement-related specifications, including those related to CIR.
Illinois has had a strong CIR presence on local agency projects for over ten years with a few IDOT experimental projects for technology evaluation. Starting in 2019, more CIR projects have appeared in their rehabilitation strategy.
Why does an agency like IDOT specify CIR in their rehabilitation projects? Senger replied, “IDOT’s network is comprised of about 85 percent composite pavements, with a large majority of those containing numerous overlays. The department has invested a lot of resources in the current pavement structure and CIR offers a cost-effective way to revitalize the existing HMA in the roadway. CIR also provides a great option for ‘rebuilding’ low ADT (average daily traffic) roadways that will never get reconstructed due to funding limitations. This treatment is environmentally friendly, cost-effective with a relatively quick return to traffic.”
Illinois State Route 91 near Dunlap, Illinois was one of these projects Senger describes. The project specified a 4-inch CIR treatment followed by a 1.5-inch HMA surface for approximately four miles. CIR is typically used on pavements with distresses including, but not limited to, raveling, potholes, longitudinal and transverse thermal cracking and edge cracking.
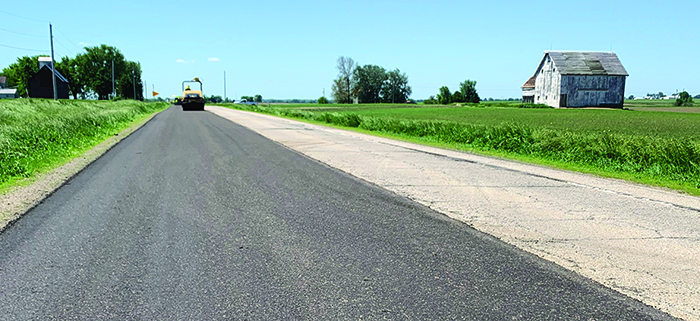
The photo above shows the construction of the CIR mat adjacent to the untreated existing lane. All the cracked, distressed pavement is pulverized, mixed with asphalt emulsion, placed through a paver and compacted to a specified density for performance. Traffic can drive on the CIR mat shortly after construction. The CIR pavement carries traffic as it releases moisture and attains final cure allowing for the HMA pavement surface construction to complete the rehabilitation process.
As with many new technologies, designers and inspectors are curious to know “How do CIR pavements perform?” IDOT’s first CIR project was constructed in 2010 and comprised of a 3.5-inch CIR treatment on a 3.8-mile section of US 24. The original pavement was in very poor condition. IRI measurements for this section averaged 273 in/mi. IRI stands for International Roughness Index which is a measure of pavement smoothness with typical values for newly paved projects between 25 and 50 in/mi. Pavements with values in the 125 to 200 in/mi range are candidates for rehabilitation.

Senger and his team have been tracking the performance of this first CIR project and shared data recently at the 2021 Ohio Transportation and Engineering Conference. The chart above shows the pavement condition rating of the CIR project as compared to composite projects across the state. IDOT employs a pavement condition rating system ranking with 9.0 being the best condition and 1.0 as the worst. This CIR project is maintaining a pavement condition rating just below seven after ten years. This is outperforming typical composite pavements (HMA overlay on PCC pavements) which generally score between five and six after ten years of life. Currently, the pavement’s smoothness is measured at 70 in/mi. and is showing some low severity cracking.
CIR may be part of the solution when it comes to identifying ways to make pavement rehabilitation and materials more sustainable. Organizations are exploring how to advance asphalt recycling technologies like CIR to positively impact the carbon footprint of asphalt pavement. Agencies are not too far behind.
When asked whether sustainability and material reuse are factors in selecting treatment options, Senger replied, “Yes. Geometrics, constructability and drainage also play a factor. IDOT has yet to develop or implement any type of LCA (Life Cycle Analysis) process, but we are always looking for ways to help the environment.”
Senger added, “One day the department may adopt an LCA (Life Cycle Assessment) process that will help govern and guide rehabilitation and reconstruction decisions. Currently, the variability in the analysis concerns me. Tweaking certain inputs can greatly influence the outcome of the analysis and we try to create a level playing field for all treatments and pavement types as much as possible.”
How can the paving industry and associations play a role? Developing a strong, accurate and reliable LCA database for asphalt materials may be critical to help agencies specify not only cost-effective, performing pavement materials, but also more sustainable options for a net zero carbon emission future.
Wielinski is an Asphalt Institute Regional Engineer based in Indiana.