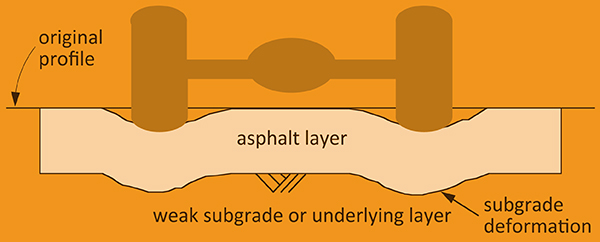
The majority of pavement distresses fall into two major categories: rutting and cracking. Both of these distresses have been around since the dawn of asphalt pavement construction.
The Marshall mix design procedure was developed over 80 years ago and attempted to account for these distresses using a stability test to deter rutting, along with a flow parameter to reduce cracking. As any experienced mix designer can attest, it is very easy to design a mixture that will not rut. This can be accomplished through the use of a dry mixture with a very hard binder. Rutting will no longer occur, at the cost of increased cracking.
At the other end of the spectrum, the use of a large amount of soft binder will prevent the mix from cracking, however, increased rutting will be observed. Modern balanced mix design concepts have shown the potential to do a much better job of optimizing mixture characteristics than the Marshall Method, but performance can still suffer. The reason for this is that the keystone of pavement performance, minimizing pavement distress, is established during the initial project design – well before the project is bid and mixture designs are developed.
Understanding the applicable pavement distresses is critical when designing an asphalt overlay project.
Rutting
Rutting is a load-related distress. A roadway cannot rut without traffic loads. There are two basic types of rutting, plastic deformation (rutting confined in the mixture) and structural rutting (rutting in the subgrade).
Structural rutting is where depressions or troughs appear in the wheel path of the lane with the subsidence occurring in the subgrade or other underlying base layers. These ruts are often accompanied by longitudinal and /or fatigue (alligator) cracking. The presence of structural rutting suggests that the aggregate base and existing pavement thickness are insufficient to carry the current traffic loads. The pavement may have been adequate 20 or 30 years ago, but something has changed.
The most common causes of structural rutting are an increase in traffic volume or the roadway layers below the pavement have become saturated or weaker. If the structural rutting does occur, do not expect a simple 1.5-inch overlay or mill and fill project to provide long-lasting service. Thorough testing and evaluation of the causes must be taken into account to develop a rehabilitation that will provide sustainable service.
Plastic deformation or rutting within the mix is much less of a problem today than in the past. Superpave aggregate criteria, Performance Graded (PG) binders, better mix design procedures and attention to quality control on the project have become standard practice. This has all but eliminated the unstable mixtures that plagued our industry in the 1980s.
However, when these standard practices are overlooked, rutting can and will occur. Specifiers can require a laboratory wheel tracking specification to assure a stable mixture is produced. The most common test requirements use a Hamburg Wheel Tracking Test (HWT) or Asphalt Pavement Analyzer (APA).
If an agency struggles with adequate aggregate availability, rutting resistance can be obtained by increasing the PG Binder grade to a level that will achieve adequate resistance to rutting for the aggregates available.
Economics quickly become a factor when the designer evaluates the cost of hauling in quality aggregate versus the cost of increasing the PG binder grade (increased polymer modification). Laboratory loaded wheel testing is essential in making these engineering decisions.
Specifying the recommended volumetric requirements and assuring they are achieved in the field is also essential to assure the mixtures produced and paved in the field prevent rutting in the mix.
Pavement distress initially identified as a mixture problem can also be caused by other, more unapparent circumstances. Stripping of the asphalt binder from the aggregate can occur in underlying pavement layers, creating the appearance of plastic flow in the surface mix. This is easily identified by obtaining cores from the roadway during or before the preparation of project plans. Moisture sensitivity specifications and testing using AASHTO T-283 are necessary in order to ensure stripping does not occur. It is important to remove unstable, rutted or stripped material prior to overlay as these pavement layers will continue to create problems in any new surface installed.
Another common problem often identified as mixture rutting is not a mixture problem at all. Newly constructed pavements showing pavement displacement are often caused by saturated layers in the subgrade or base. This saturated condition is usually caused by rainfall before paving or other subgrade drainage issues that must be repaired before completion of the project by removing the pavement and drying the lower layers or solving the underlying drainage issues.
Cracking
Pavement cracking has replaced rutting as the most concerning pavement distress to pavement owners. Reduced binder content along with the rapid expansion of recycled binder use has increased cracking distress. There are three major types of cracking that must be understood to design and construct an asphalt surface with a respectable lifespan. These are thermal cracking, reflection cracking and fatigue cracking.
Thermal cracking traditionally appears as relatively straight cracks that are perpendicular to the centerline of the roadway. Thermal cracks are relatively uniformly spaced, ranging from less than 50 feet apart in a northern climate to well over 1,000 feet in more temperate climates. Thermal cracking is a non-load related distress and will appear regardless of traffic loading. Rapid daily temperature changes build up stress in the pavement. If the pavement cannot dissipate those internal stresses quickly enough, the stress will exceed the pavement strength and the pavement will crack. As pavements age and become more brittle they have less ability to “relax”, resulting in an increase in thermal crack frequency.
This pavement behavior is directly related to the binder grade used in the mix. Attention to binder grade selection is the most effective way to minimize thermal cracking. The success of the low-temperature parameters of the PG Binder grading system are well documented and verified in the results of modern crack testing procedures. The selection of the appropriate binder grade to prevent thermal cracking must be considered during the project development stage and not left to the contractor during the post-letting mixture design phase.
Reflection cracking is caused by stresses generated from lower pavement layers that are transmitted to the surface of the pavement. When an overlay is placed on a cracked pavement (HMA or PCC), imperfections from below will appear in the overlay. How soon these imperfections appear depends on the severity of distress in the lower layers, overlay materials utilized, pavement thickness and the climate of the region.
Severe thermal cracking in asphalt pavement and all PCC cracks and joints will telegraph to the surface of a new overlay. The thinner the overlay the faster they will appear. The longest-lasting solution is to eliminate the source of the reflection cracking. Aged asphalt pavements showing severely deteriorated thermal cracks are a good candidate for full-depth reclamation. Portland cement pavements must be cracked and seated or rubblized to eliminate reflective cracking.
If the underlying source of distress cannot be eliminated, overlay material selection and design can reduce the severity of reflection cracking. Durable mixtures that perform well in laboratory cracking testing will perform better when the mixtures are placed on already cracked surfaces. Durable mixtures will maintain crack integrity and resist both finger spalling and pothole development. Polymer modified mixtures allow polymer modified joint sealer to perform better.
Fatigue cracking, often referred to as alligator cracking, is the result of repeated bending under wheel loads. Fatigue cracking occurs when traffic loads exceed the capacity of the pavement structure. Loss of substructure support, insufficient thickness, reduced pavement strength and poor construction practices (insufficient pavement density) can all lead to increased fatigue cracking and reduced pavement life.
The loss of pavement support can be minimized by maintaining proper drainage and conducting maintenance activities to reduce the infiltration of water into the pavement structure. Maintaining the integrity of the pavement foundation is essential, especially on relatively thin pavement sections (4” or less.)
Mixture properties can also impact fatigue cracking. Flexible pavements must be durable enough to endure millions of load repetitions throughout its life. Insufficient asphalt content, excessively stiff binders, segregation and poorly compacted lifts can all accelerate aging and contribute to reduced fatigue life in the pavement.
When asphalt pavements suffering fatigue cracking are overlaid, special attention must be considered during the project design. The in-place strength of the existing pavement section must be evaluated to establish the overlay thickness or the distressed areas removed and replaced prior to placing a simple overlay or mill and fill. It is important to understand that a fatigue-cracked pavement is essentially a failed pavement section that needs rehabilitation. Overlooking the condition of the existing pavement can lead to a significantly reduced lifespan of a new overlay.
In conclusion
Understanding pavement distress is essential throughout the initial design, construction and rehabilitation of flexible pavement systems. Diligent engineering to address pavement distress will maximize pavement life and the rate of return for the taxpayer.
Blow is an Asphalt Institute Senior Regional Engineer based in South Dakota.