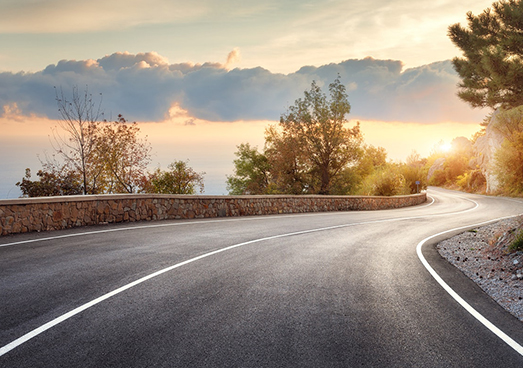
Asphalt pavements are the surfacing choice for about 94 percent of the roughly 2.75 million miles of paved roads in the United States. Asphalt is used to construct sub-base, base course and surface layers.
The largest consumption of asphalt binders in paving applications is for hot mix asphalt (HMA) and warm mix asphalt (WMA). WMA makes up 40 percent of the production of asphalt paving mixtures. For simplicity, HMA is used to imply either HMA or WMA herein.
According to the National Asphalt Pavement Association (NAPA), HMA production in 2017 was about 375 million tons. State highway agencies and other public agencies including cities and counties use about two-thirds of the total production of HMA. Private work (commercial and residential) accounts for the remaining one-third of the production. State highway agencies utilize about 45 percent of HMA production.
Incremental increases in pavement life or a reduction in the first cost for materials or pavement structural sections can result in substantial cost savings. For example, HMA production in the United States has historically ranged between about 350 million and 500 million tons on an annual basis. If pavement life can be increased by one year, an annual saving of billions will result.
Motivation for improving asphalt pavements
A substantial amount of the innovation associated with asphalt pavements has been stimulated by global and national events. Product availability, environmental movements and political interests have all influenced the advancement of asphalt materials. The in-place price of asphalt mixtures is significantly driven by the cost of the asphalt binder, fuel for heating materials, transportation costs and construction equipment fuel.
Availability of fuels and asphalt binders was also of great concern in the mid-1970s. Energy conservation and its availability were national and international concerns. Environmental concerns were also being addressed globally during this period for the first time. Inflation was significant. Price controls were implemented on several products. As a result of these driving factors, the 1970s and early 1980s witnessed a period of rapid technology development and deployment in the asphalt paving industry.
The first decade in the 2000s also witnessed significant crude oil and asphalt binder price increases. During this decade global warming became an additional item of concern throughout the world. The rapid inflation of goods and services has not followed the rapid increase in crude oil price during this decade, as occurred during the mid-1970s and early 1980s.
The Strategic Highway Research Program
Accompanying technology development was a general reduction in available funding for highway construction and rehabilitation and maintenance. Thus, the condition of the nation’s highways deteriorated. The primary performance problems documented in the early 1980s were rutting, water sensitivity of asphalt mixtures, transverse cracking and aging. These problems were recognized by agency and industry leaders.
This led to the formation of the Strategic Transportation Research Study (STRS) Committee in 1983. A variety of activities followed culminating in the Strategic Highway Research Program (SHRP) that defined the research program in 1986. A $50 million research and development program was developed with key research directed towards asphalt binders, asphalt mixtures, pavement performance and performance-based specifications.
Research results were available in the early 1990s and included the performance-graded (PG) asphalt binder specification, a new method for asphalt mixture laboratory compaction, as well as new test methods for mixture design. The effort associated with the implementation of SHRP was extensive and continues today.
Asphalt pavement technology changes
The technology associated with the use of asphalt binders in roadways has changed over the decades. While change in the asphalt paving industry is relatively slow, it has nevertheless been significant from an economic as well as environmental, health and safety points of view.
Asphalt pavement thickness design
Pavement thickness design concepts were developed based on soil mechanics principles in the 1930s. Two-and three-layer elastic solutions became available to predict deflections and stress and strains in pavement layers by the late 1950s. A linear elastic multilayered pavement analysis computer program was developed in the mid-1960s, first by Chevron Asphalt and then by Shell Oil shortly thereafter. Layered elastic programs have been utilized as a research tool since the 1960s and have been incorporated into mechanistic-empirical pavement design procedures.
In the late 1970s and early 1980s linear viscoelastic and nonlinear viscoelastic methods were introduced. Finite element approaches to pavement design were also developed during this period. The engineer’s ability to predict rutting in pavements and cracking has improved from these more advanced mechanistic methods.
Stresses, strains and deflections in pavements under a variety of loading and environmental conditions can be calculated by layered elastic, viscoelastic and other solid mechanics approaches. Fracture mechanics has been used to predict various forms of cracking based on calculated stresses and strains.
Layered elastic and finite element models to calculate stress, strain, deflection and permanent deformation require complex material characterization. For example, unstabilized subgrade, subbase and base material properties are stress-dependent and moisture content-dependent. Loading time and temperature are factors for asphalt-bound material properties. Asphalt-bound materials also change with aging time and with the presence of moisture. Proper characterization of pavement materials is time-consuming and has been a major issue associated with the implementation of more advanced methods of pavement design.
The theory available to calculate stress, strain and deformation is far more accurate than our ability to characterize materials. In addition, the correlation of these calculated parameters and their associated materials inputs with field performance needs to be further developed to determine robust failure criteria. This has been a difficult and challenging task.
The perpetual pavement concept developed in the 2000s is based on limiting the stresses and strains in pavement layers below critical threshold values. The use of engineering mechanics to predict these stresses and strains is a critical part of the development of this concept. Commonly accepted failure criteria for pavement rutting, based on maximum vertical compressive strain on the subgrade, and for pavement fatigue cracking, based on maximum horizontal tensile strains in the asphalt bound layers, are used to design perpetual pavements, in which, theoretically, an extremely large number of traffic loads can be carried by the pavement without rutting or fatigue cracking. In a perpetual pavement, the impact of the environment, loss of friction and the aging of the pavement are addressed by removing and replacing a thin layer of asphalt surface mixture every 10 to 20 years as distresses become evident at the surface.
Asphalt binders
Asphalt binders are complex materials of which mechanical properties are difficult to define and the chemical properties are extremely complex.
Asphalt binder technology has moved from the “chew” test in the early 1900s to advanced rheological techniques used by the polymer industry today. Key properties of asphalt binders include the health and safety aspects of the material as well as consistency over a range of temperatures, loading rates and durabilities. Various types of rheological, mechanical or physical tests are primarily used to characterize the viscoelastic properties of asphalt binders. Asphalt binders are liquids at elevated construction temperatures and brittle solids at temperatures common in the winter.
The needle penetration test was utilized to describe the consistency or stiffness of asphalt binders until about 1962 when many agencies progressed to viscosity-based systems. The PG system was developed in the Strategic Highway Research Program (SHRP) during the late 1980s and early 1990s and is used in the United States and other countries. Many agencies are now including the Multiple-Stress Creep Recovery system to classify asphalt binders.
The SHRP-developed PG specification system for asphalt binders was a significant advancement in the technology, although quality relationships between asphalt binder properties and pavement performance are elusive.
Asphalt binder manufacturing practices have fundamentally not changed over the years. However, fewer asphalt binders are produced directly during the refining process today. Today a significant number of asphalt binders are blends of refined asphalt binders and any number of materials or modifiers. These combinations of materials are used to economically adjust low-temperature and high-temperature properties of asphalt binders to meet the PG specification as well as to potentially improve the overall performance. This blending is more likely performed in terminals rather than in large crude oil refineries.
One of the most widely used groups of additives is polymers. Natural rubbers saw limited usage in the 1950s and styrene-butadiene random copolymers were utilized regionally in the 1960s for chip seals and for some asphalt mixtures. Styrene-butadiene-styrene (SBS) polymers introduced in the late 1970s and early 1980s are in relatively widespread use in many areas of the world. Chemical additives that improve the water sensitivity of the asphalt mixture were developed as well.
Asphalt mixture design
Asphalt mixtures contain both asphalt binders and graded aggregates with or without other additives and modifiers. These mixtures are designed and constructed to minimize distresses. Asphalt mixtures harden with age and may be sensitive to the presence of moisture.
Asphalt mixture properties change dramatically with test temperature and rate of loading. Thus, materials should ideally be characterized over a temperature range and loading rate that simulates the asphalt mixture in service.
Mixture design methods
Mixture design methods are used to establish optimum combinations of asphalt binder and aggregate. The Hveem and Marshall methods were primarily developed in the 1930s and 1940s and were named after public agency pioneer engineer/technologists from California and Mississippi, respectively. These test methods continue in use today.
The Hveem and Marshall approaches to asphalt mixture design allow the asphalt mixture to be designed to resist permanent deformation or rutting while providing some consideration for durability of the mixture. Volumetric design parameters were also part of the design for both methods. Mixture design parameters include asphalt binder content, aggregate gradation and air void contents.
SHRP developed more fundamental mixture property tests in the late 1980s and early 1990s to address rutting, cracking, aging and water sensitivity. This mix design system became known as Superpave.
A significant number of cracking tests have also been developed over the years. These tests include the repeated load beam tests (fatigue) developed in the late 1950s and the “overlay tests” first developed in the 1970s for several forms of indirect tension, direct tension, flexural tests and several notched beam types of samples.
The asphalt mixture performance tester (AMPT) was developed in the last decade and is now associated with the American Association of State Highway and Transportation Officials (AASHTO) mechanistic-empirical pavement design method. This test provides parameters to predict rutting and cracking as well as provide stiffness information for pavement thickness design purposes. The equipment was developed to be a compact and user-friendly test method based on lessons learned from the SHRP program.
Balanced mix design concepts, while not new, wisely promote various means to design mixtures that perform better. They attempt to design mixtures that will both resist rutting and cracking distresses.
Mixture types
Dense-graded mixtures are the most widely used asphalt mixture today. A gap-graded mixture, stone mastic asphalt or stone matrix asphalt (SMA), was developed in Germany. Today it is used in several U.S. states. Improved resistance to rutting and cracking as well improved durability and friction can be achieved with SMA mixtures.
Open-graded or porous friction courses have gained widespread acceptance in some states. These types of mixtures reduce “splash and spray” from traffic, reduce tire-pavement noise, reduce the potential for hydroplaning and can be designed to provide excellent friction.
Several concepts have been developed to reduce, slow down or eliminate reflection cracking from an old asphalt or portland cement concrete (PCC) pavement after treated with a new asphalt mixture overlay. A satisfactory “interlayer” to reduce, slow down or eliminate reflection cracking in most climates has not been developed.
Additives and modifiers for mixtures
Much like how asphalt binders have benefited via modification, asphalt mixtures have also utilized several additives to assist mixture performance. These include hydrated lime, portland cement and liquid anti-strip agents to improve the water sensitivity of the material. By the early 1990s, hydrated lime was widely used following slow growth in the 1980s. Portland cement has been used as an antistrip agent in a few states since the 1980s. Another additive now found in some mixtures is fibers. They have been used in a few specialty patching mixtures, for some types of open-graded mixtures and stone mastic asphalt mixtures and dense-graded mixture as well.
Warm mix additives were introduced to the United States paving industry in the early 2000s, having been developed in Europe the previous decade. NAPA and the Federal Highway Administration are largely responsible for advancing the technology stateside.
Warm mix technologies include wax-based products, chemical systems and foaming techniques. Warm mix allows for reduced mixing and compaction temperatures for asphalt mixtures which affords a variety of benefits. Known benefits of WMA include reduced emissions, improved worker conditions, reduced fuel usage for mix production and benefits to the construction operations. The construction operations benefit from improved compaction, extending the construction season, increasing the paving day and longer haul distances.
Asphalt mixtures and pavement thickness design
The perpetual pavement concept mentioned previously is an extension of the “full-depth” concept promoted by the Asphalt Institute in the 1960s. Properly designed perpetual pavements design their respective layer’s mixtures to address their specific and unique requirements. The bottom layer’s mixture will have high asphalt binder content, smaller maximum size aggregate and low air void content to provide good fatigue resistance and resistance to the presence of moisture.
As the intermediate or middle layer requires relatively high stiffness values, it can be a lower-cost asphalt mixture with high percentages of RAP or RAS, having a lower asphalt binder content.
The surface course materials should be resistant to rutting and the presence of water, have good friction properties and be resistant to thermal or low temperature cracking. An optimum asphalt binder content and a binder that is not too soft or hard is important for this mixture. A relatively thin layer (1-inch plus or minus) of an open-graded or porous friction course can be used to obtain high friction, reduce hydroplaning and reduce traffic tire-pavement contact noise. Dense-graded or SMA mixtures are other appropriate options depending on circumstances.
Asphalt pavement recycling
For over 70 years the asphalt paving industry has proudly recycled existing pavement materials for pavement rehabilitation, reconstruction and maintenance. The most common form of recycling is hot central plant recycling, with nearly 80 million tons of RAP used on an annual basis. Significant national research and implementation efforts advanced by the state departments of transportation and the Federal Highway Administration resulted in recycling technology development and deployment in the mid-1970s when all forms of recycling grew in popularity following the oil embargo. As a result, substantial savings in pavement construction, rehabilitation and maintenance have resulted from recycling asphalt pavements. Refinement and improvement to these technologies continue today.
Preventive maintenance and management systems
Optimization of the type and timing of rehabilitation and maintenance operations has saved significant amounts of money associated with providing safe and efficient transportation on the nation’s highways. This is best done with maintenance management and pavement management systems developed in the 1960s. These systems have become increasingly more sophisticated and can provide forecasts of funding needs through optimization techniques.
Today’s sophisticated management systems provide predictions of future pavement conditions based on design, construction, current conditions and maintenance data. Moreover, they incorporate funding parameters in association with other economic factors to allow engineers to better optimize their roadway systems. This tool allows them to plan both current and future activities to accomplish the optimization.
Accelerated pavement testing
Several full-scale test roads have been constructed over the years in the United States to improve the future of pavements. The 1950s saw regional test roads in Maryland and Idaho and it culminated with the AASHO Road Test constructed and operated in the late1950s and early 1960s for both asphalt and portland cement bound pavements in Illinois. Flexible and rigid pavements continue to be tested on the MnRoad facility as they have been since the early 1990s in Minnesota. WesTrack was constructed in Nevada in the early 1990s for asphalt bound pavements, and the National Center for Asphalt Technology (NCAT) Test Track was constructed in Alabama in the 2000s, also for asphalt bound pavements. The NCAT Test Track remains in service today.
Other forms of accelerated pavement testing have been used throughout the world. Large-scale equipment has been developed to test small pavement sections placed under field construction conditions. This equipment has been utilized in several countries including France, Spain, China, Japan, South Africa and the United States.
Construction equipment for asphalt pavements
Equipment manufacturers have also advanced the asphalt paving industry with major innovations in the 1970s. At the hot plant, the introduction of drum plants for the production of hot mix began. Drum plants have continued to be refined, now being offered in various configurations including parallel flow, counter flow and double drum options. Today’s drum plants are also very capable of handling large quantities of RAP.
The Clean Air Act of 1970 stimulated the use of baghouse and wet washer systems on HMA plants to improve air quality. The baghouse is now the primary tool used to meet air quality standards in the developed countries.
To take advantage of the high production of drum mix plants, mixture storage silos were developed and attached to these plants. These storage silos allowed mixture to be produced at high production rates, stored and loaded into trucks at a different rate.
The first cold milling machine was developed in 1974 and demonstrated to a Federal Highway Administration Expert Task Group meeting on recycling in Las Vegas that year. This equipment allowed for the economic removal of asphalt mixtures from the roadway and quickly became a must-have tool for roadway rehabilitation. It is one of the most useful equipment pieces for pavement rehabilitation and recycling.
The 1970s witnessed a significant development in equipment for both cold in-place and hot in-place recycling. Improved pulverization equipment, portable crushing and mixing equipment were developed during this period for cold in-place recycling (CIR). Improved heating, mixing, laydown and air quality control equipment was developed for hot in-place recycling during the 1970s and early 1980s. These complemented the improved engineering of asphalt emulsions used with CIR.
Vibratory compactors were developed in the late 1970s and became common for asphalt paving in the 1980s. These compactors or rollers allowed for more efficient compaction of asphalt paving mixtures. In addition, the roller widths became greater, which contributed to the improved efficiency of the compaction operation. Intelligent compaction systems are now the next step in the evolution of compaction equipment.
The materials transfer device was developed in 1989 and affected the market in the 1990s. These devices allow for storage of the asphalt mixture (about 25 tons) at the laydown site, remixing, which reduces aggregate segregation and promotes temperature uniformity. Nonstop movement of the paving machine, which improves the smoothness of the riding surface, is more easily accomplished with this tool as well.
Wrap up
Flexible asphalt pavements have been serving the driving public for well over 100 years. Advancements over time have been relatively steady. During the past 50 years, much has changed while much has also stayed the same.
Asphalt binders have gone from being mostly a product from their respective refineries without modification, to now being blends of materials from various refineries, commonly with different modifiers within them to enhance performance and meet today’s more robust specifications. These specifications have changed too. Going from very empirical grading methods to more fundamental processes which also attempt to take into consideration local environmental conditions.
The mix design process has taken a leap forward with the advent of Superpave supplanting older methods which were developed generations before. Today they are moving even further as balanced mix design concepts are potentially better engineering mix design properties beyond traditional volumetric data.
Recycling technologies grew in popularity in the 1970s and 1980s. While their usage decreased for some years, they are again growing in popularity once more. Moreover, additional products from outside the paving industry have been and are being incorporated into mixtures. Crumb rubber from waste tires and asphalt shingle waste are two prime examples of materials that can be used successfully in asphalt pavements.
Equipment manufacturers have and continue to develop better options for the production, construction and maintenance of asphalt pavements. Continuous flow drum plants, vibratory rollers and cold milling machines are three major examples on the equipment side. Advanced automation continues to be developed and implemented. Higher and more consistent quality pavements are the end goal of these advancements.
The engineering of pavement structures has also advanced from relatively simple empirical design procedures to more advanced mechanistic approaches. Advanced computer programs are now commonplace, and designs are further optimized via the incorporation of layer-specific design parameters.
The future for asphalt pavements continues to be bright. Evidence of asphalt’s ability to provide tremendous long-lasting service is seen in the 156 perpetual pavement awards issued by the Asphalt Pavement Alliance to date. But more can and should be done.
Much more can be said about where challenges are seen for our industry’s future, but that is a discussion for another day. To quote an ad campaign from 1968, “You’ve come a long way baby!” While certainly true that asphalt has come a long way, it is readily capable of meeting future challenges with the gusto and success it has enjoyed in propelling our country and the world forward.
Dr. Jon A. Epps completed his Ph.D. from the University of California at Berkley in 1968. Generally speaking, asphalt mixtures were designed, produced and constructed with means and methods that were then decades old. Asphalt binders were rarely modified and largely single-sourced, unblended products in 1968. Construction equipment was still much like it had been at the end of World War II.
Dave Johnson was introduced to asphalt materials in 1990 when dramatic changes were being developed and implemented due to the Strategic Highway Research Program. The modification of binders was increasingly common. New laboratory tools for both binders and mixtures were being adopted across the nation.
Much of this article is an adaptation of Dr. Epps’ 2019 TRB Thomas B. Deen Distinguished Leadership and 2020 AMAP Hall of Fame presentations, coupled with Johnson’s perspective.