But, that is the way we have always done it
In the last 50 years, some form of the following discussion has probably occurred thousands of times. I know because I asked the same question when I was starting in the industry.
Young engineer: “OK, so we design the mix at 4 percent air voids and construct it to 8 percent. I don’t get it.”
Experienced engineer: “Traffic will compact it to 4 percent. Or, at least, that is what I was told when I started in the industry.”
The concept of designing at 4 percent dates back at least to development of the Marshall method of mix design in the early 1940s. Today, most asphalt mixes are designed using the Superpave method. However, Superpave still carries the shadow of Marshall mix design in that the design air voids are 4 percent.
Before the Superpave method of design was developed, Marshall design was ubiquitous. OK, for those of you like me, who had never heard this word before, I will save you the time looking it up because I did the first time I heard it. Ubiquitous means commonly used, available everywhere.
Outside of the U.S., Marshall mix design is nearly a universal standard, everywhere except in France.
Superpave roots and LCPC
In the 1970s, after seeing the Texas gyratory compactor during a 1959 visit to the U.S., the French national highway agency, then known as Laboratoire Central des Ponts et Chaussées (LCPC), developed a mix design method based around a gyratory compactor they designed. In the LCPC method there is a range of allowable design air voids, but designs are typically done at 5 percent. Compaction on the road is targeted to 95 percent maximum density (5 percent in place air voids).
The Superpave method of mix design is built around the Superpave gyratory compactor. The origin of this device goes back to the Texas gyratory compactor but also incorporates French research from the development of the LCPC gyratory compactor. Considering the links to both compactors and to volumetric analysis, Superpave can trace its roots back more than 100 years to the Richardson method of mix design that was done in the late 1890s.
During the Strategic Highway Research Program, from which Superpave was developed, there was discussion about setting up Superpave in a similar fashion to LCPC, that is, design to 5 percent and compact to 5 percent. However, it was decided that for ease of implementation Superpave should be patterned after the Marshall method as much as possible and the idea was shelved.
Fast forward to the early 2010s. Why do we continue to live in the shadow of the Marshall method of design? Theoretically, it should be possible to adapt the French concept of 5 percent design and 5 percent construction, to Superpave. If Superpave mixes can be compacted to 5 percent air voids it should be possible to reduce the rate of asphalt binder aging and, if applied correctly, pavements should last longer with no additional cost. How is that for cost-benefit?
The first of three trial sections was built in 2013 and after five years the difference in performance was significant enough that INDOT contracted 12 Superpave5 projects in 2018.
What is Superpave5?
Superpave5 uses a design air void content of 5 percent instead of the current Superpave requirement of 4 percent. In order to maintain the same current minimum asphalt content, the VMA is increased by 1 percent from the current values contained in AASHTO M323.
Specifications for aggregate properties (fractured faces, Fine Aggregate Angularity, etc.) stay the same but gradation and design lab compaction effort (Ndesign) need to change.
A common myth is that laboratory compactive effort (Ndesign) will change asphalt content, but data does not support that. Three mixes designed at different gyrations each have the same asphalt content because each has the same VMA and air voids. Ndesign does impact rutting resistance. The 125-gyration mixture has higher stiffness and about 40 percent more rut resistance than the 75-gyration mixture.
In-place density also impacts rut resistance. A 75-gyration mixture compacted to 5 percent in place air voids has more rut resistance than a 125-gyration mixture compacted to 7 percent in-place air voids.
The research phase of Superpave5 determined how much the design gyrations should be reduced to allow in-place compaction to 5 percent voids and to ensure that rut resistance does not decrease. The answer? Fifty gyrations for all design traffic greater than three million ESALs and thirty gyrations for design traffic of less than three million.
So, the bottom line for Superpave5 rut resistance is that 50 gyrations for design, compacted to 5 percent in-place air voids will give the same or slightly greater rut resistance than a 100 gyration Superpave4 mixture compacted to 7 percent in-place air voids.
The promise of Superpave5 is resulting asphalt mixes that have at least the same amount of asphalt binder content, that are compactable to 5 percent in-place air voids and have at least the same amount of rut resistance. But, can they be built? And, do they age more slowly?
They can be built! Three trial projects were constructed in Indiana, one each in 2013, 2014 and 2016. Average density for the standard Superpave4 mixes was 92.5 percent, 91.8 percent and 93.3 percent respectively (7.5 percent, 8.2 percent and 6.7 percent air voids.) For the Superpave5 mixes, the average density was 95.9 percent, 94.7 percent and 95.5 percent (4.1 percent, 5.3 percent and 4.5 percent air voids.) In each of the three projects, the rolling train was kept the same for the Superpave5 as for the Superpave4. The laboratory research was based on equalizing the amount of field compaction for Superpave5 mixes and the trial projects were used to confirm that higher density can be achieved with the same field compaction.
Field performance
The first trial section was built in 2013. It was evaluated five years after construction in 2018. The 2013 trial project had 13,400 AADT and 19 percent heavy trucks. The project called for milling and replacing two lifts of HMA. The Superpave5 trial consisted only of the surface mixture. The Superpave5 trial section is 2.2 miles long in the southbound lane. The adjacent 2.2- mile length in the northbound lane was used to compare Superpave4. The surface mixture was a 9.5-mm Nominal Maximum Size surface mixture. Cores were taken between the wheel paths at three locations in the Superpave4 mixture and three locations in the Superpave5 mixture.
Permeability of the cores was measured in the lab and the relationship between permeability and in-place air voids is typical. When in-place voids are slightly higher than 7 percent permeability increases rapidly. Note that the distribution of in-place air voids for the Superpave4 cores (5.5 to 9.0 percent) overlaps with the Superpave5 distribution (3.0 to 7.1 percent.)
The first question was, “How much has the asphalt binder aged?” In the original construction both the Superpave5 and Superpave4 contained PG70-22 with 20.2 percent of asphalt binder replacement from post-consumer asphalt shingles. (As a side note, today asphalt shingles are limited to 3 percent. In 2013, the specifications allowed up to 7 percent shingles).
As part of the 2018 evaluation, the asphalt binder was recovered from each location. The average of the three Superpave4 sample locations was PG 100.0-16.2. For the three Superpave5 sample locations, the average was PG 94.0-21.0. Asphalt binder in the Superpave5 sections was 6°C less aged on the high-temperature grade and 4.8°C less aged on the low-temperature grade.
In the last few years, a new asphalt binder parameter has been identified that relates to environmental cracking. Delta Tc is the difference between the low-temperature grade as identified by stiffness, S, and slope, m. A value of -3 or greater has been identified as not susceptible to cracking. Between -3 and -5 there is a risk of cracking and less than -5 is considered prone to cracking. The average delta Tc for Superpave5 is -3.6 and for Superpave4 is -8.3.
Pavement condition data was collected with an automated van. Cracking, rutting and smoothness (IRI) was collected. There was no difference between the smoothness of the two sections, both were very smooth with an IRI of 53 and 47 inches per mile. Reflective low temperature cracking occurred in both sections, 341 and 299 ft. per 100-foot section. Average rut depth is 0.14 inches for the Superpave5 and 0.13 inches for the Superapve4. Both are basically the same.
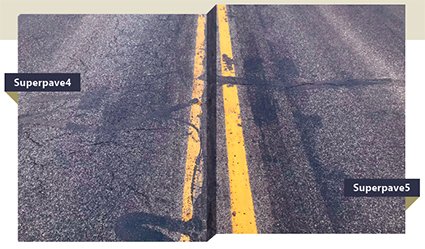
The main performance difference is surface cracking. The Superpave4 section is covered with extensive block cracking about 12 to 18 inches in size. The Superpave5 section has almost none. This observation is consistent with the delta Tc of the asphalt binder. The photo above shows Superpave4 on the left side and Superpave5 on the right side. Block cracking is visible between the low-temperature transverse cracks across the road on the left side (Superpave4 section.) There is no block cracking on the right side (Superpave5 section.)
INDOT moves forward
The research project set design parameters for Superpave5. The oldest of the trial sections demonstrated the benefit of reduced aging and reduced cracking. In 2018 INDOT contracted for 12 projects to include Superpave5 allowing a cross section of contractors in Indiana to gain experience designing and constructing Superpave5 mixtures. And in January 2019 INDOT made changes to their standard specifications calling for all asphalt mixtures to be designed using Superpave5 specifications. These specifications will apply to all INDOT projects after September 2019.
And so, the answer is “yes.” We can slow the aging of asphalt binder in our mixes to reduce cracking, maintain rut resistance and do so at no additional cost.
Huber is the Associate Director of Research at The Heritage Research Group in Indiana.