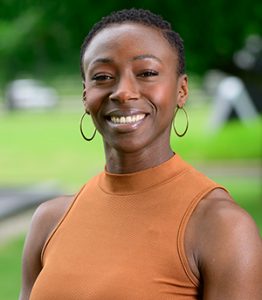
Last fall, I circulated a survey to Canadian agencies with the purpose to gain insight into agencies’ needs and where my focus should be placed when planning educational programs, technical publications and providing technical assistance.
One of the questions asked owners to rank the most common pavement distress observed in asphalt pavements in their network, with 1 as the most common, and 8 as the least common distress. The results started coming in first from the Atlantic provinces: New Brunswick, Nova Scotia, Prince Edward Island (PEI) and Newfoundland and Labrador and I noticed that the top three most common pavement distresses were:
1. Raveling / Aggregate Loss
2. Longitudinal Joint Cracking
3. Reflective Cracking
It piqued my interest because early fatigue cracking has been on our radar in Canada for a while, but raveling is not a pavement distress that I often hear discussed. So, let’s talk about it.
What is raveling?
Raveling occurs when the top layer of aggregate breaks free from the asphalt binder in the asphalt pavement. This causes the pavement to slowly start disintegrating from the top-down. It starts slowly. However, once the pavement begins to disintegrate at the surface and is not maintained, it will progress throughout the asphalt layer of the road surface.
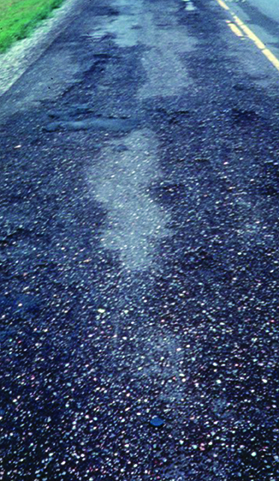
What causes raveling?
Raveling tends to occur in older, asphalt pavements that have become brittle over time due to oxidation. However, raveling can also be caused by:
• Insufficient compaction
• Cold or wet weather paving
• Poor aggregate quality
• Insufficient amount of asphalt binder
• Overheating of asphalt mix
• Excessive use of reclaimed asphalt pavement (RAP)
• Dust coating on aggregate particles that make it difficult for asphalt to bind to the aggregate
Preventing asphalt raveling
Since several factors contribute to raveling, it is critical to evaluate the potential cause and mitigate each one as necessary. Importantly, following best practices for achieving adequate compaction will go a long way to prevent raveling.
For example, lift thickness plays a critical role in preventing raveling because it relates to compaction. A minimum lift thickness of three to four times the nominal maximum aggregate size should always be maintained. This allows enough room for particle reorientation and proper compaction to occur. If the lift is designed or placed too thin there will be insufficient room for the aggregate to reorient itself in a dense configuration that is impermeable to water. Moisture has a damaging effect on asphalt pavements.
And while we’re talking about moisture, paving in moist or wet weather is never recommended, yet it is sometimes necessary, especially in the Atlantic provinces where the asphalt paving season is very short. In these situations, extra measures must be taken such as tarping trucks to minimize exposure of the asphalt to moisture, and cooler temperatures will require modification to compaction methods to compensate for a quicker cooling of the mix. This is particularly important during the cool, wet fall and early spring months.
Lastly, regular preventative maintenance, rather than repairing asphalt after it has already started to ravel, will ensure that asphalt pavement service life is preserved.
Wakefield is an Asphalt Institute Regional and Research Engineer based in Canada.