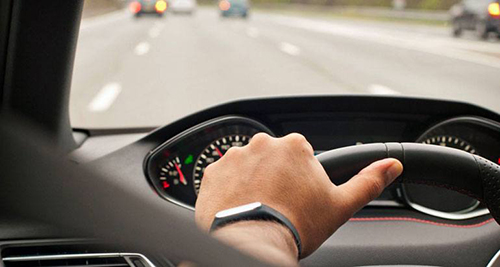
Despite being recognized as a laid-back person, friends and family will tell you that I am not a patient or forgiving driver. It is not a trait I am proud of, but to state a well-known and – according to Dr. Sheldon Cooper – meaningless tautology, it is what it is.
Being a professional engineer and knowing I have continuing education requirements to maintain that P.E. designation, it bothers me that in the U.S. we can grant someone a driver’s license as a teenager and then say “Congratulations, you know all you need to for the rest of your life. No need to ever review the rules or demonstrate your skills again. Go drive and annoy Mike as much as possible.”
I’ve had one situation happen to me so often that I found a PDF of the Kentucky Driver’s Manual online and read the relevant part to make sure I wasn’t wrong (I wasn’t, by the way). I won’t get into the details here, but it got me to thinking about how we all can fall into the trap of being too comfortable with a practice, thinking we know how to do something that we’ve done for a long time without realizing that we’ve overlooked, misunderstood or misinterpreted the proper procedure and didn’t bother to check it out.
To combat this complacency a good friend and colleague devotes a day every year with their company’s lab staff to read and discuss the AASHTO standards. I understand there may be doughnuts and pizza involved which certainly helps with the comprehension of asphalt testing methods and practices, if not blood sugar levels. The point of this is that standards can change, and people sometimes develop bad habits by skimming past sections and not recognizing their importance. By meeting regularly, the technicians can take the time to review the standards in-depth and maybe avoid bad practices and mistakes simply from misunderstanding.
I’ll share an example in our lab recently that is more of a case of overlooking the importance of an item than any misunderstanding.
AASHTO R 78 is the standard for low-temperature recovery of residue from asphalt emulsions. The basics of the practice are that we spread the asphalt emulsion in a thin film and then subject it to a period of conditioning in a forced-draft oven operating at 60°C to remove the water, leaving us with a residue that we expect to be similar to what we see on the road. Simple enough, right? What could go wrong?
Our technician saw the requirement in AASHTO R 78 that we needed to use a forced-draft oven meeting the requirements of a Type IIA oven in ASTM E145. We had an oven in the emulsion lab that we routinely used that had a circulating fan in the back. That should work; it was a forced draft oven. What we didn’t consider was that an E145 Type IIA forced-draft oven had a minimum and a maximum number of air changes required. Missed that.
As it turned out, we discovered that our oven of choice wasn’t forcing the draft enough, with less than half of the required minimum number of air changes per hour. In a procedure where the goal is to remove water from a sample at a certain time at a certain temperature the amount of airflow is probably pretty important. The solution was simple…there was another oven in the adjoining lab that had a much higher rate of air changes per hour, within the required range, and we started using that when performing the practice.
Did the lack of sufficient forced draft circulation matter? We’re still investigating but we do know that before the change in ovens we were observing consistently lower G* values when we performed DSR testing than we expected. The working hypothesis is that there may have been moisture remaining in our residue samples when we used the older oven due to the lack of sufficient circulation.
Mistakes happen in the lab. We know that physical errors can lead to variability and that practice helps develop proficiency and minimize physical errors. Taking the time to thoroughly review the standards on a routine basis and participate in continuing education can minimize mental errors. Now, if I could just convince Kentucky drivers of that.
Mike Anderson is the Director of Research and Laboratory Services at the Asphalt Institute.