Should you consider specifying it?
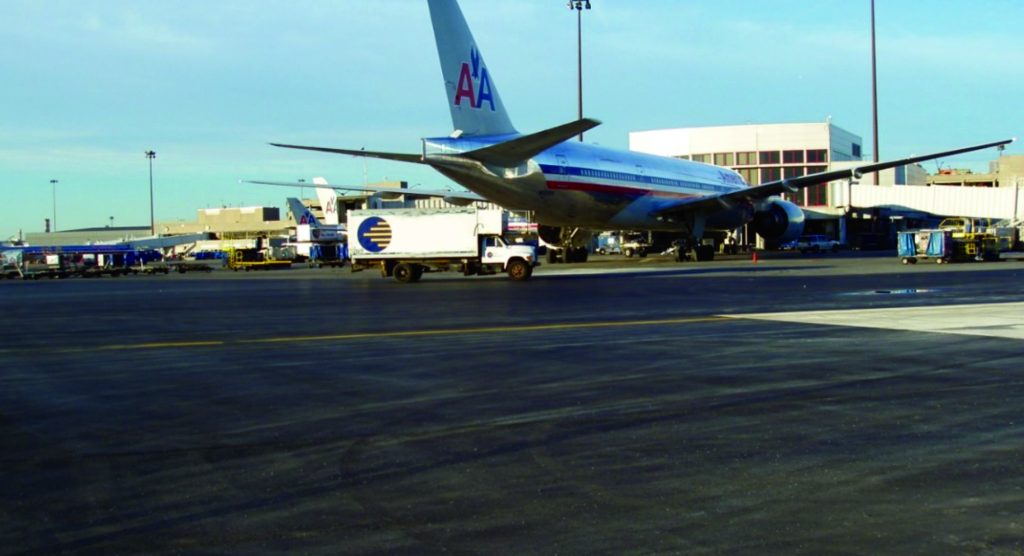
Before we delve into jet fuel resistant (JFR) asphalt pavements, perhaps a bit of review is in order.
According to the Asphalt Institute’s “MS-25 Asphalt Binder Testing” manual, asphalt cement “is the dark brown to black cementation material in which the predominant constituents are components that occur in nature or obtained in petroleum processing.”
With the adoption of the Performance Grading (PG) system in the mid-90s, came the dual requirements that asphalt cements resist rutting at higher ambient temperatures while remaining flexible enough to resist cracking during cold weather. While some asphalt cements can be expected to perform when the in-service temperatures and traffic levels are moderate, most asphalts cannot pass the PG requirements imposed by higher temperatures or loading extremes without additional modification. As a result, the term “binder” is now used to describe both the unmodified asphalts typically used on low volume local roads in temperate climates, as well as modified asphalt common in pavements exposed to higher temperatures and higher traffic volumes. Since the adoption of the PG system, polymer-modified have proven their long-term value. Consequently, mix designers have become more comfortable specifying higher levels of modification, especially polymer-modified asphalt (PMA) binders.
The problem
During the refining process to produce asphalt binder, all the lighter fractions (i.e., naptha, gasoline, diesel fuel, lubrication stocks, etc.) found in the typical barrel of crude are removed. Since they come from the same starting point (a barrel of crude) they are similar in nature, meaning that any of these lighter fractions when spilled on an asphalt pavement can literally act as a solvent to soften the binder, which can lead to permanent deformations and even failures.
Spills of aviation fuel and hydraulic oil can occur on airport parking aprons during servicing. Hydraulic oil can continue to leak while aircraft are moving in narrow channelized corridors leaving the terminal (a.k.a. alleyways) or standing in queues on taxiways waiting to takeoff. The conditions of extremely heavy, slow-moving or stopped traffic and the potential for leaks/spills make airfields highly susceptible to this type of distress.
To remedy this problem, coal tar sealers (CTS) have traditionally been used to protect asphalt pavements from fuel damage. Coal tar, as the name implies, is not a product of crude oil refining, but rather a by-product of burning coal in an oxygen-deficient oven to produce the coke needed to fuel the steel-making industry. The problem with CTS is the fact that it has a different coefficient of expansion than the PG binder it is supposed to protect. This difference in expansion and contraction over time and with temperature swings causes the CTS to crack in a tight-knit pattern referred to as “chicken-wire cracking.” This type of cracking, unless the CTS is routinely re-applied, exposes the underlying binder to the jet fuel spills and shortens the pavement’s service life. An additional, extremely dangerous hazard is the potential for Foreign Object Damage (FOD) to aircraft when sealers ravel off the pavement surface as it becomes more and more brittle.
The solution
The obvious solution is to make the entire depth of surface mixture fuel-resistant and eliminate the need for sealers that only protect the surface of the pavement. With this goal in mind, Associated Asphalt (AA) began in 2002 to address the issues of coal tar sealers with an effort to formulate a safe, environmentally friendly alternative using a highly Polymer-Modified Asphalt (PMA) binder.
According to Ron Corun, Specialty Products Manager, when AA started their research into JFR binders, a typical PG 76-22 binder at the time might have contained only 3% polymer when compared to the total weight of the binder used in an asphalt mixture. As the total polymer content approached 7.5%, some amazing results began to emerge. A mix using a PG 64-22 unmodified (no polymer added) binder, would lose 10% of its weight from a standard core sample when soaked 24 hours in jet fuel. A mix made with a standard binder grade PG 76-22 PMA binder would lose 5-6% of its weight after 24-hours. But a jet fuel resistant PMA, with 7.5% polymer would have a weight loss of less than 1.0%.
Field verification
With the favorable results in the lab, AA began working with the Port Authority of New York and New Jersey (PANYNJ) to provide JFR binders for a 450-ton test section on Taxiway GG at LaGuardia Airport scheduled to be paved in late 2002.
Prior to allowing this first-time use of JFR mix, PANYNJ wanted mix verifications for resistance to rutting and cracking. AA went back to the laboratory and used both an Asphalt Pavement Analyzer and Flexural Beam Fatigue test to measure the cycles to failure to confirm the mix design was in that sweet spot; where the mix is not too stiff and brittle (prone to cracking), while remaining flexible without being susceptible to rutting.
The JFR binder graded out to be PG 94-22 on the Performance Grading system and when tested, the results showed both goals were met:
• After 8,000 cycles in the APA, rutting was well under 2mm at 1.6mm
• In the Beam Fatigue cycles to failure, the JFR went 45,000 cycles for a ratio of over 10-1 when compared to a regular PG 82-22.
A pavement condition survey conducted 16 years after completion in 2018 showed Taxiway GG still performing well. In fact, the survey found Taxiway GG was the only pavement at LaGuardia not showing signs of rutting.
New specification
Until recently, JFR binder mixtures were not a part of the Federal Aviation Administration’s (FAA) P-401 standard specifications for asphalt mixtures. To get approval for the use of a non-standard specification, an airport needed to submit a “Modification of Standards” request to the FAA Regional office for approval before an airport’s design consultant could specify the use of JFR mixtures on an FAA project.
Despite the need for this extra step, the FAA approved at least six major airfield projects during the 12-year period from 2002 to 2014. In July 2014, FAA issued an updated Advisory Circular #150/5370-10G that included a new specification item P-601 Fuel-Resistant Hot Mix Asphalt Pavement. After version 10G was issued, JFR became a standard specification and could be routinely specified by designers and five more major projects have been completed using JFR, including at least one Department of Defense (DoD) project.
While the DoD and FAA specifications are remarkably similar, they are still two different stand-alone specifications. Having said that, the Tri-Services (Army, Air Force and Navy that make up the DoD engineers) have followed the successful deployment of FR mixtures over the years. In July 2018, a parking apron at Hurlburt Field AFB in the Florida Panhandle was paved using a JFR mixture based on the FAA’s P-601 specification. Monitored and evaluated very closely by the U.S. Army Corps of Engineers the pavement has shown excellent performance.
On December 21, 2018, the FAA issued another updated Advisory Circular #150/5370-10H that renumbered item P-601 Fuel-Resistant Hot Mix Asphalt and changed the name to P-404 Fuel-Resistant Asphalt Mix Pavement. By renumbering and renaming, FAA effectively moved the JFR spec, now just FR, from the section of the specification covering surface treatments (P-600’s) to the asphalt pavement section of the specification (P-400). This move allowed pavement designers to consider FR mixtures a structural component, as opposed to being just a “surface treatment” of the pavement. This also allows the use of the much stiffer FR mixtures in the intermediate courses, or lower layers, of the pavement to address the deeper stresses caused by the heavy, slow-moving aircraft.
After a history of proven performance, the DoD on November 1, 2020, followed the FAA’s approach and updated its own United Facilities Guide Specification UFGS 32 12 17.19 to include “Fuel Resistant Asphalt Paving for Airfields – Surface Course.” The specification can be found on the DoD’s Whole Building Design Guide website.
Cost/benefit
At what cost? When comparisons are made between actual project unit prices of regular P-401 and P-404, the FR mixtures will generally be 25% higher. The main reasons for this difference are the need for two-to-three times more polymer modification, coupled with the need for 1.0-1.5% more binder in the mix.
However, an increase in P-404 mixture costs affects only one pay item on any given project – the surface layer. The cost of all the other items necessary to build an airfield project like milling, patching, electrical, striping, etc. are all unaffected and remain the same. Plus, FR mixtures eliminate the need for the initial application of CTR and all future re-applications over the life span of the asphalt pavement. In other words, for the typical airfield project, the overall cost increase will only be in the 5-7% range.
In October 2019, the National Center for Asphalt Technology (NCAT) at Auburn University released a research document entitled “Report 19-08: Mix Design Strategies for Improving Asphalt Mixture Performance.” In the report, NCAT advocated for a longer pavement life by designing asphalt mixtures with outstanding rut resistance balanced with overall crack resistance.
The report went on to suggest the three main mix adjustments to provide the greatest improvement in pavement performance:
• Use more polymer-modified asphalt
• Increase the asphalt content by lowering the design air voids
As adopted, the FAA’s and the DoD’s specifications utilize all three of the mix adjustments NCAT recommends for a longer pavement life. The FR mixture specifications combine a highly polymer-modified asphalt binder with a mix designed at a higher asphalt content that is then compacted to lower in-place air voids in the field. This combination provides improved fatigue (cracking) resistance and durability, which results in longer pavement life and lower life cycle cost, with the added benefit of being fuel resistant.
Not just for airside anymore
The bus lanes on the landside of the Boston Logan airport are also exposed to heavy, slow-moving, channelized traffic in vehicles that seem to constantly leak fuel and oil. Following the success of their airside projects, Boston Logan decided to use an FR mixture on their bus lanes in front of the terminal.
Jones is an Asphalt Institute Senior Regional Engineer based in Ohio.