Asphalt mix design is a delicate process of choosing and balancing the appropriate aggregates, asphalt binder and their proportions to obtain an asphalt mixture that is deformation resistant, fatigue resistant, low temperature crack resistant, durable, moisture damage resistant, skid resistant and workable.
The quality of the asphalt mix and its ability to perform is evaluated through set parameters for aggregates, asphalt binder, recycled materials and volumetric properties such as: Air voids (Pa), Voids in Mineral Aggregate (VMA), Voids Filled with Asphalt (VFA), and dust proportion. The parameters are set because they have historically provided a good indication of a mixture’s probable performance.
To understand how to control asphalt mixes, in the lab and in the field, it’s important to first understand what these parameters are and how they can be impacted during mix production.
Air voids – The air voids are the small pockets of air between the asphalt-coated aggregate particles in the asphalt mixture. A certain amount of air voids is required in the asphalt mix to allow for additional compaction under vehicular traffic and to accommodate slight expansion of the asphalt binder as the temperature increases in the summer months. The air voids in an asphalt mix is related to the durability of the mix.
Voids in Mineral Aggregate – VMA includes the air voids in the asphalt mix, and the effective asphalt binder (not absorbed into the aggregate pores). VMA is also related to the mix durability. VMA specifications help to ensure there is adequate liquid binder in a mixture.
Voids Filled with Asphalt – VFA is the voids that exist between the aggregate particles that are filled with AC. In other words, it is the portion of the VMA that is filled with effective asphalt binder.
Dust proportion – This is the dust to effective binder ratio of the asphalt mix and can be correlated to mix workability or stiffness in the field. These parameters are connected so it is rare to change one, without impacting the other.
Now I’ll share four tips for controlling asphalt mix designs in the lab and in field production:
1. Aggregate and gradation selection
2. Aggregate specific gravity
3. Reclaimed Asphalt Pavement (RAP) aggregate properties
4. Control of fines
Tip 1 – Aggregate and gradation selection
Most of your challenges with asphalt mix designs in both the lab and the field can be minimized by having good control of the aggregates – because remember, they are the largest component of your asphalt mix making up about 95 percent by weight. A typical mix design consists of both coarse and fine aggregates. If a mix designer only uses one coarse aggregate and one fine aggregate in the mix, the options for adjusting the gradation will become very limited, which makes it extremely difficult to consistently meet the specification requirements.
Unfortunately, the number of coarse and fine aggregates used in the mix isn’t entirely up to the mix designer. Such things as the economics of the blend and the production plant capabilities in terms of the number of available cold feed bins all will need to be considered, especially if there are other components such as natural sand and recycled materials in the mix.
It is useful for the mix designer to communicate the importance of this flexibility to the mix producer. It allows more control for adjusting the gradation because you have more options for changing the percentages of the various aggregates to meet the target gradation or job mix formula (JMF).
Tip 2 – Aggregate specific gravity
Aggregate Bulk Specific Gravity (Gsb) is the ratio of the oven-dry mass of a unit volume of aggregate to the mass of the same volume of water. This includes both the impermeable and water-permeable void volumes to the mass of the same volume of water. The procedure for determining specific gravity for coarse and fine aggregate are AASHTO T 85 and AASHTO T 84 respectively.
For the purposes of appreciating this tip, I’ll give you a summary of the procedure for determining Gsb: In short, an aggregate sample is washed and soaked for 15 to 19 hours. The soaked sample is brought to saturated surface dry (SSD) condition carefully with a towel and/or a fan, without over-drying it. The sample’s submerged weight is carefully determined before drying once again to record the oven-dry weight. The recorded weights are used to calculate the bulk and apparent specific gravity and absorption of the aggregate.
Accurate determination of the Gsb is very important because, as shown in Equation 1, Gsb is used to calculate the VMA of the asphalt mix. However, due to the subjective nature of determining the SSD condition in both the coarse and fine aggregate Gsb test procedures, more often the Gsb is overestimated.
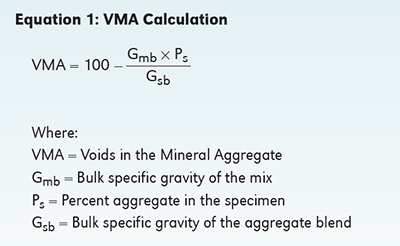
How can this happen?
In the Gsb test procedure, this happens when the aggregate is dried beyond the SSD condition, or when too much time passes between getting the aggregate to SSD condition and weighing it. These testing variabilities result in higher Gsb values that result in artificially high VMA values.
Use the Effective Specific Gravity (Gse) to check the validity of Gsb.
What is Effective Specific Gravity (Gse)?
Gse is the effective specific gravity of the aggregate, based on the aggregate volume including water permeable voids not filled with asphalt. This value is calculated from theoretical maximum specific gravity of asphalt mix.
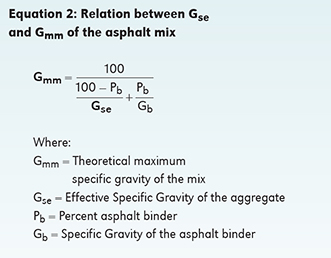
How can Gse help?
You can evaluate the quality of the Gsb determination by using the Gse calculation as a reference. Gsb and Gse each use the same mass of the oven-dry aggregate, but they use different volumes. Since Gse has a smaller volume than Gsb, in no case should Gsb ever be greater in magnitude than Gse
Gse > Gsb
Tip 3 – Reclaimed Asphalt Pavement (RAP) aggregate properties
Ok, let’s take it a step further and add RAP in the mix. When we add RAP, we’re adding aggregate and binder components that will impact the mix volumetric properties and so we must measure the RAP properties to be able to control it in the mix.
Before the use of VMA as a mix design property, the gradation of the RAP aggregate was the main aggregate property that was determined. Since VMA requires knowledge of the combined aggregate Gsb, it is important to also accurately determine the RAP aggregate specific gravity (Gsb-rap).
So how do we determine Gsb-rap?
There are a few methods of determining Gsb-rap. One method uses the RAP aggregate that is obtained after performing a solvent extraction or ignition oven procedure. The extracted RAP aggregate is split into coarse (plus 4.75mm) and fine (minus 4.75mm) fractions then the Gsb-rap is determined of each size fraction.
The advantage of this method is you get a direct measure of Gsb-rap. The disadvantage is that the extraction (or ignition oven) procedure can change aggregate properties. It’s also possible for the sample to still contain asphalt or solvent, making it difficult to accurately determine Gsb-rap.
Another method uses the RAP as is (unextracted), to determine the maximum theoretical specific gravity or Gmm of the RAP. If the asphalt binder content of the RAP is known or determined, then the effective specific gravity Gse of the RAP aggregate can be calculated (Equation 2) and used instead of the Gsb.
The advantage of using Gse is it’s easy to determine Gmm, and it’s one of the most repeatable tests we have. So, it makes Gse measurements of RAP more repeatable than Gsb. However, a big disadvantage of using Gse instead of Gsb is that because Gse is always higher than Gsb, it artificially raises the VMA value of the mix.
A third method is a combination of the first two methods:
1. Determine Gmm of RAP (ASTM D2041)
2. Determine asphalt content of RAP
3. Calculate Gse of RAP (Equation 2)
4. Assume asphalt absorption, Pba, based on experience with materials
5. Calculate Gsb of RAP aggregate
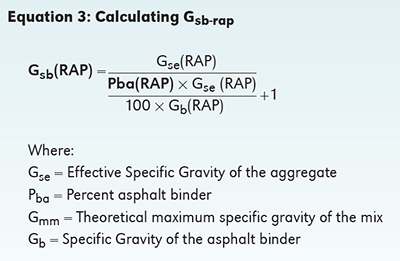
One advantage of determining Gsb-rap this way is that it is still easy to determine the Gmm and asphalt binder content of the RAP to calculate the Gse (RAP). A disadvantage to this method is that the accuracy is highly dependent on how well the percentage of absorbed asphalt could be estimated.
Determining the right Gsb-rap is important because an artificially high value has the potential to decrease the effective asphalt binder content in the mix, and thus reduces durability of the mix.
Tip 4 – Control of fines
By far the most common reason for adjusting a mix design during initial plant production is to adjust the air void content and VMA. The main reason for this is aggregate degradation. Degradation occurs during handling in the field and includes transport from stockpiles to aggregate bins, batching from bins to aggregate belt, heating in the drum or hot bins, mixing and so on. This generates a significant amount of mineral filler or dust, and this increase in dust during production typically results in a decrease in air voids. If air voids decrease, VMA will also decrease unless the asphalt content is changed.
When air voids decrease, many will address the problem by reducing the asphalt binder content slightly, which will increase the air voids. However, this will typically result in a decrease in VMA since the total asphalt binder content (and effective asphalt binder) has been reduced, which will again decrease the pavement durability.
It is recommended that low air voids and VMA be corrected during field production by adjusting the aggregate proportions. For fine dense-graded asphalt mix, air voids and VMA can be increased by increasing the proportion of fine aggregate. It is important again to maintain the required air voids while increasing the VMA in order to prevent rutting in the mix.
The Bailey method is an excellent tool that can be used to predict the changes in VMA and voids as aggregate gradation changes. This method can be used for troubleshooting Superpave mixes during field production.
Bringing it together
The asphalt mix design is produced in a laboratory under calibrated and controlled conditions to meet the required mix parameters. However, we recognize that it is only the first step and that almost all mix designs will vary in their mix properties during production due to variability in aggregate stockpiles, and aggregate breakdown. The key is understanding which parameter needs to be adjusted to ensure the proper change is made to maintain the quality of the asphalt mix.
Did you know?
In a mix with 25 percent RAP, an error of 0.04 in the Gsb-rap can affect the calculated VMA of the asphalt mix by nearly 0.5 percent. This can be the difference between an acceptable and marginal mix!
Wakefield is an Asphalt Institute Regional Engineer based in Canada.
References
[1] Asphalt Institute, “MS-2 Asphalt Mix Design Methods”, Seventh Edition, 2014
[2] Brown ER, Lord B, Decker D, Newcomb B. “Hot Mix Asphalt Tender Zone”. National Center for Asphalt Technology (NCAT) Report 00-02. April 2000.
[3] Chadbourn B, et al. “The Effect of Voids in Mineral Aggregate (VMA) on Hot-Mix Asphalt Pavements” Minnesota Department of Transportation, Report No. MN/RC- 2000-13, September 1999
[4] National Cooperative Highway Research Program (NCHRP), “A Manual for Design of Hot Mix Asphalt with Commentary”, NCHRP Report 673, Transportation Research Board, 2011