
For as long as people have worked at things, they have been coming up with rules of thumb to make their work easier. We offer these five handy rules of thumb for asphalt mix designers.
1
For every 0.3% binder, the air voids change about 1%
During the mix design process, trial batches often result in air voids (Pa) somewhat near the target value, but not actually at the target value. If the trial VMA (voids in the mineral aggregate) is below the minimum, simply increasing or decreasing the binder content to meet the target air void content is not enough. The aggregate component would have to be adjusted, typically by changing the relative proportions of each aggregate. However, if the VMA meets minimum requirements (by at least 0.5% or so), Pa can be adjusted by simply adding or removing binder from the mix until the target is reached. The question is, how much is enough?
Although the relationship between percent binder (Pb) and theoretical maximum specific gravity (Gmm) is perfectly linear, the relationship between Pb and Pa is not. As Pb increases in an asphalt mixture, Pa decreases for two reasons: 1) the binder takes up volumetric space in a compacted specimen that was once occupied by air and 2) the binder acts as a lubricant to allow the aggregate particles to shift more closely together during compaction. Working in the designer’s favor is the fact that this relationship is fairly linear in the design range of a mix design, flatting out as there becomes less space available for aggregate movement.
For most dense-graded mixes, the rate of change tends to be about 0.3% binder to 1% air voids. Increasing Pb by 0.3% decreases Pa by about 1% and decreasing Pb by 0.3% increases Pa by about 1%. For example, let’s say the target lab-molded air void content is 4.0% and our first trial using 5.0% binder results in an air void content of 5.3%. The first trial has sufficient VMA, so we probably won’t need to change the aggregate structure. Using our handy rule of thumb, we’d select a binder content of 5.4% for trial #2, expecting our air voids to decrease about 1.3% to the target of 4.0%.
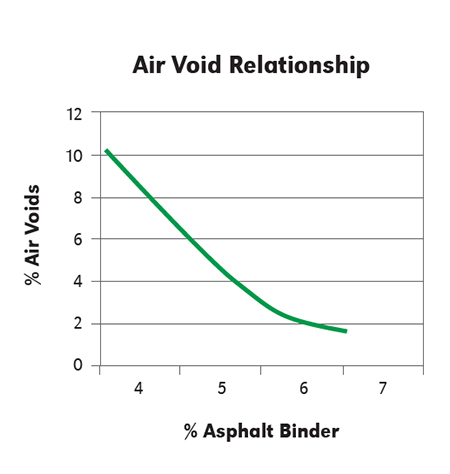
2
When using RAP in the lab mixing process, increase the oven temperature for virgin aggregate by 0.9°F (0.5°C) for every 1% RAP used
In an asphalt mixture with no reclaimed asphalt pavement (RAP), virgin aggregates are batched, combined, and placed in an oven overnight at the appropriate mixing temperature. Since RAP contains asphalt binder, it cannot be heated in the same manner without affecting its properties. However, we still must make sure any moisture in the RAP has evaporated before we weigh it out and mix it. To mitigate the effect of extended high heat on the RAP binder, we’ll have to heat the RAP in smaller batches at lower temperatures. Generally, it is recommended that the RAP be batched separately in no more than 1,000 to 2,000 gram batches and heated for no more than two hours at 230°F (110°C). This is sufficient time to heat the RAP and remove any extraneous surface moisture. Higher temperatures and longer heating times have been shown to change the properties of some RAP materials.
To compensate for the introduction of the lower-temperature RAP material, the virgin aggregate should be heated above the mixing temperature so that the material equilibrates to the mixing temperature. Although actual mix temperatures vary, a good rule of thumb is to increase the temperature of the virgin aggregates by 0.9°F (0.5°C) for every percent of RAP used in the mix. For example, in a mixture using 25 percent RAP, the mixing temperature of the virgin aggregates should be raised by 25 x 0.9°F = 22.5°F (12.5°C).
The mixing temperature of the virgin asphalt binder should not be adjusted.
To mix each sample, the pre-batched virgin aggregate at the adjusted temperature is added to a mixing bowl (or bucket mixer) and the heated RAP (no more than 230°F (110°C)) is added and quickly mixed with the virgin aggregates. A crater is formed just as in the normal mixing process, and the virgin asphalt binder at its standard temperature is added in the appropriate amount and the mixing process is started.
3
Pba increases by about 1.0% with every 0.060 to 0.070 difference in Gse and Gsb
One of the parameters every mix designer must consider is the binder absorption (Pba) of the mix. This fundamental property is established by two aggregate specific gravity determinations: Gse, the effective specific gravity, and Gsb, the bulk specific gravity.
As shown in the image, the bulk specific gravity volume includes the volume of the aggregate and the volume of water-permeable pores in the surface-dry aggregate. The effective specific gravity volume includes the volume of the aggregate and the volume of water-permeable pores in the surface-dry aggregate minus the volume of the asphalt-permeable pores. The relationship between the two, as shown in equation 5.27 in Asphalt Institute’s MS-2 “Asphalt Mix Design Methods” manual, allows us to calculate the percentage of binder absorption in an asphalt mixture.
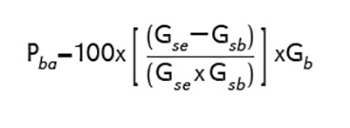
Note that for complete accuracy, the equation cannot be as simple as Pba = Pb – Pbe, because Pba is expressed as a percentage of the total aggregate weight, while Pb and Pbe are expressed as a percentage of the total mix weight. In the equation, multiplying by the specific gravity of the binder (Gb) makes that conversion.
The rule of thumb takes advantage of the fact that as the difference between Gse and Gsb increases, the absorption must also increase. Pba will increase by about 1.0% with every 0.060 to 0.070 difference in Gse and Gsb.
The word “about” is important because the rate of increase will change depending on the magnitude of specific gravity values. To help visualize this truth, looking at extreme cases is often helpful. For example, a difference of 2 between 100 and 98 is 2% of 100, but the same difference of 2 between 4 and 2 is 50% of 4.
Using a typical Gse value of 2.700, if Gsb is also 2.700, then there is no absorption of the binder and Pba = 0. A difference between the two of 0.070 means that Gsb is 2.630. Assuming a Gb of 1.01, Pba = 0.996%, or 1.0% shown to one decimal place.
Again, assuming Gb = 1.01, if the mix uses lower specific gravity aggregates like Gse = 2.500, then a difference between the two of 0.060 means that Gsb is 2.440 and Pba = 0.993%, or 1.0% shown to one decimal place.
This rule of thumb is handy for the designer, because they will have a good estimate of how much binder is lost to the absorption of the aggregate when they are selecting and testing aggregates.
4
The “Limited” Rule of 92
The useful temperature interval (UTI) conveys the maximum to minimum viscoelastic temperature range, expressed in °C, in which a binder is expected to perform properly while in service. For example, if a binder has a performance grade (PG) of 64-22, it has a UTI of 64 – (-22) = 86 °C. Historically, the Rule of 92 states that if the UTI is less than 92, the binder is unmodified; if the UTI is exactly 92, the binder is likely modified; if the UTI is greater than 92, the binder is modified.
We prefer to use the Rule of 92 with more caution and recommend that you do the same. In fact, we will name so many exceptions to the Rule of 92, it may be best to just call this the “Limited” Rule of 92.
The first thing we’d like to highlight is that the Rule of 92 is intended to be applied to conventional PG asphalts graded in 6°C increments as opposed to the binder’s true grade (TG) expressed to the nearest tenth. For example, if a binder is designated as a PG 64-22, it means that neither the high nor low ends of the grade reached the next 6 °C increment, such as a PG 70-22, PG 64-28, or PG 70-28. However, the binder could have a TG of 69.9-27.9 and still be considered a PG 64-22. This PG 64-22 has a UTI less than 92, but its TG of 69.9-27.9 clearly has a UTI greater than 92. Just remember, the Rule of 92 is meant for the PG and not the TG.
It should also be cautioned that the Rule of 92 is intended for PG asphalts that are not blended with RAP or other hard binders, such as air-blown asphalts or refined hard pen asphalts. There are numerous examples of RAP-blended asphalts containing no modification with UTI above 92. For example, an unmodified 30% RAP blend may have a composite binder PG after blending of 82-16, which results in a UTI of 98. The rule simply isn’t reliable for RAP blends or other blends containing hard pen asphalt, so you will want to avoid using the rule in those applications.
The Rule of 92 is also not useful for confirming the absence of a modifier. Although the original Rule of 92 states: “below 92, the asphalt is unmodified” – there is not a solid basis for that assumption. The definition of a “modifier” conventionally refers to polymer modifiers, i.e., SBR latex, SBS, SEBS, polyolefins, ethylene copolymers, reactive elastomeric terpolymers; crumb rubber, PPA and others. These modifiers used in relatively moderate-to-high dosages tend to expand the UTI by increasing the high-temperature PG with minimal impact to the low-temperature grade. However, ANY of these modifiers can be added in lower dosages without exceeding a UTI of 92. For example, Alabama Department of Transportation’s (ALDOT) 804.02 binder specification states the following for a PG 64-22 (UTI of 86): “a minimum of 1.5% (polymer) solids” must be present either from “modifying a PG 58-22 or blending from a PG 76-22” to create a PG 64-22. This is, by definition, a modified binder with a UTI below 92.
One last exception is that the definition of a “modifier” seems to have expanded in recent years. Does the definition now include other additives that also “modify” asphalt, such as re-refined engine oil bottoms (REOBs), rejuvenators, warm mix additives, anti-strip additives, and age-resistant additives among others? If the term “modifier” includes these other types of additives, the Rule of 92 is not useful in detecting all of them.
In summary, many of us have heard of this rule before, and hopefully, this information gives us a little more awareness of its limitations. The best potential application of the “Limited” Rule of 92, in our opinion, is to detect the addition of conventional modifiers, added in moderate-to-high dosages to virgin PG asphalts.
5
For every 20% RAP, the necessary virgin binder content goes down about 1%
The basis for this rule is that asphalt binder makes up approximately 5% of the weight of an asphalt mixture, including RAP mixtures; therefore, if 20% RAP is included in a mixture, it follows that 20% RAP x 5% binder on RAP = 1% RAP binder in the mix. That’s where the “1% virgin binder replacement per 20% RAP” rule comes from. This can be a handy rule of thumb, but we recommend a little bit of nuance when applying this rule, as we’ll explain.
First of all, the actual Pb in a virgin or RAP mixture is normally not exactly 5%. The actual binder percentage may range from 4% < Pb < 8%, depending on the mix type (dense, OGFC, SMA), aggregate gradation, nominal maximum aggregate size, design gyrations, and other factors. However, 4.5% ≤ Pb ≤ 6% is the more common range for a RAP stockpile and a good approximation for binder content in most RAP mixtures. Taking 20% of this range (4.5% to 6.0%) gives a binder replacement range of 0.9% to 1.2%. As you can see, assuming 1% is still not a bad rule of thumb considering the amount of potential variability in binder percent.
Perhaps a more impactful consideration of the “1% binder replacement per 20% RAP” rule of thumb is that it assumes RAP binder is 100% effective at coating virgin aggregates and blending with virgin binder. This assumption is not fully agreed upon among asphalt technologists. For example, previous research by Georgia Department of Transportation (GDOT) engineers led to a specification reducing the allowed RAP binder contribution from 100% to 60%. Under GDOT’s specification, known as the corrected optimum asphalt content (COAC), the 1% rule would become the 0.6% rule. In other words, for every 20% RAP, only approximately 0.6% virgin binder is replaced. Other agencies have implemented modified versions of COAC, including SCDOT, which has a 75% allowance for RAP binder contribution – in which case, the 1% rule would become the 0.75% rule for every 20% RAP.
In many cases, the 1% rule will result in fairly reliable “quick math” without too much concern about material variability or specifications. However, just use it with caution and remain aware that these factors may impact assumptions regarding RAP binder replacement.
Rules of thumb should never be used to cut corners. We should always strive for top-quality work. But these five rules of thumb should be handy tools to help the designer understand and make decisions that might make it easier to arrive at their target: a mix design that not only meets specification requirements but will also result in a quality pavement that lasts a long time.
Gierhart is the Asphalt Institute Deputy Director of Engineering based in Oklahoma.
Allen is an Asphalt Institute Regional Engineer based in Florida.