A couple of years ago, I was preparing a talk on “What happened to warm mix asphalt?” and I remember getting stuck on the presentation outline in a daydream…
Once upon a time, technical asphalt conferences showcased countless WMA research findings from the lab and field. I happily added my master’s thesis to the knowledge pool when I researched material properties of HMA and chemically-modified WMA.
It is no surprise that there was so much excitement about WMA then, because there are many demonstrated benefits of using WMA including the potential to lower energy demand during production and construction, reduce emissions at the plant and the paver, increase allowable haul distances, reduce thermal segregation, use as a substitute for anti-striping additives, lower production and paving temperatures, improve compaction and the list goes on.
Two of these benefits of WMA that have long fascinated me are the lower production and paving temperatures of asphalt mix and improved compaction because of their potential impact on the performance and service life of our asphalt pavements. This goes back to our understanding of how asphalt binders age with time in the environment.
Asphalt binders are composed of organic molecules, so they react with oxygen from the environment. This reaction is called oxidation and it is as natural as the browning of an apple or banana when exposed to the air. Oxidation causes the asphalt binder to lose the smaller asphalt molecules, often termed “volatiles” and changes the structure and composition of the asphalt molecules – it becomes stiffer and more brittle. These changes make asphalt pavements more susceptible to cracking.
Even though apples turning brown is inevitable, we often use a few old-fashioned tricks to help slow down this process, and the most important thing is to reduce the apple’s exposure to air. The same principle can be applied, keeping in mind that an asphalt binder’s rate of oxidation depends on temperature and how much oxygen is available to react with the individual asphalt modules. As a rough rule of thumb for very thin films of asphalt, the rate at which oxidation occurs doubles for every 10oC increase in temperature. This increase is compounded, meaning that the rate quadruples for a 20oC increase in temperature. This behavior is illustrated in Figure 1.
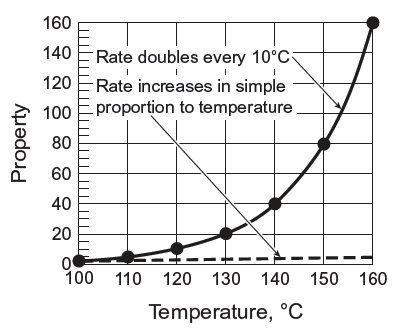
Figure 1: Effect of temperature on property change
This tells us two important things: (1) oxidation rate is highly dependent on a combination of temperature and time; and (2) oxidation is reduced if the access to oxygen is limited.
To discuss what we can use to reduce asphalt binder aging, we have to remember that there are two types of asphalt binder aging, the first is short-term aging, which occurs when the binder is heated to the temperatures used in the laboratory for asphalt mix designs and in the mixing plant during asphalt mix production, up to 350oF (177oC). During mix production, the asphalt binder has the most exposure to oxygen and high temperatures, with asphalt film thicknesses of just a few microns coating heated aggregates. The rate of aging is significantly faster at this stage.
The second type of aging occurs in-service. This is a slower rate of aging and varies depending on the asphalt pavement density, environmental conditions such as temperature, hours of exposure to sunlight and moisture. Laboratory tools used to simulate the short-term aging and long-term aging are respectively the rolling thin film oven (RTFO) and pressure aging vessel (PAV).
How well the asphalt binder performs depends on both its short-term and long-term aging conditions. What can we control from the short-term aging side during asphalt mix production and placement?
Short-term: Reducing production and placement temperatures
Laboratory testing of asphalt binder blends of PG 64-22 has shown that a reduction in short-term aging temperature of 50oF (10oC), reduces asphalt binder mass loss (loss of volatiles) by approximately 40 percent and asphalt binder aging rate by approximately 30 percent (Figure 2). If production and paving temperatures can be reduced, what would be the impact on the long-term performance of that asphalt pavement?
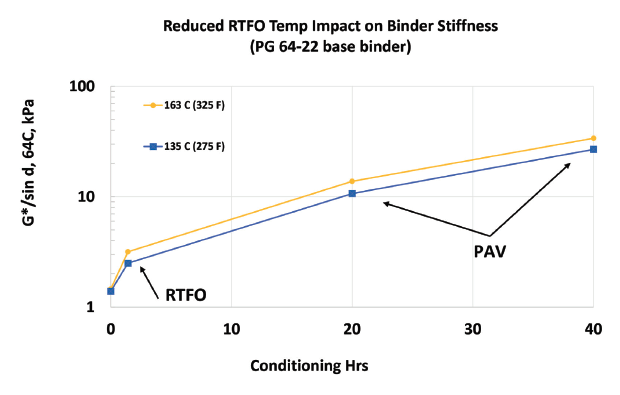
Figure 2: Example of asphalt binder hardening rate with time and temperature for PG 64-22 (Source: Ingevity)
To answer that question, we need to consider testing that estimates the performance of appropriately conditioned asphalt mix samples. Ingevity recently shared performance testing data from TSIT Engineering that compares the rutting (permanent deformation) and cracking performance of dense graded asphalt mixes that addresses this. The various asphalt mixes, listed in Table 1, were produced at the conventional production temperatures (i.e., HMA) and at lower temperatures (i.e., WMA) using two chemical warm mix additives.
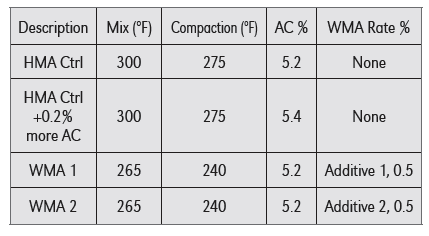
Table 1: Asphalt mix parameter used in TSIT testing of HMA and WMA
HMA vs WMA: Rutting performance
The Hamburg Wheel Tracking device was used to evaluate the rutting performance of the HMA and WMA mixes and showed no significant change in the WMA rutting performance as compared to the HMA. Interestingly, the 0.2 percent increase in AC for the HMA showed more potential for rutting than the control HMA and WMA mixes (Figure 3).
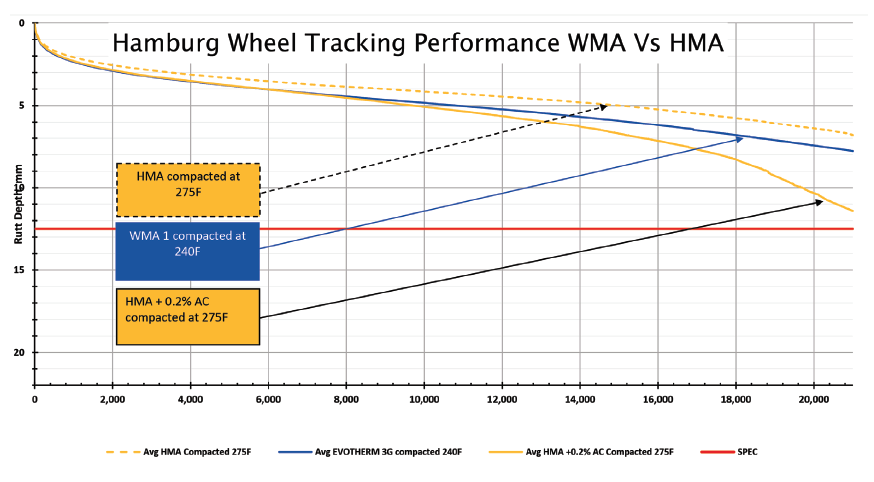
Figure 3: Hamburg Wheel Tracking Performance of HMA and WMA
HMA vs WMA: Cracking Performance
From a cracking standpoint, TSIT used the Indirect Tensile Cracking Test (IDEAL CT) to determine the cracking tolerance index of the asphalt mixes at intermediate temperatures. IDEAL-CT results have been correlated with field performance in terms of fatigue, reflective and thermal cracking with field data collected from the Federal Highway Administration’s accelerated load facility (ALF).
The test results from TSIT Engineering showed better cracking performance when the mixes were produced as WMA, and when 0.2 percent more AC was added to the HMA (Figure 4). Statistically though, the HMA with 0.2 percent more AC was equivalent in cracking performance compared to the control HMA, and on the average WMA mixes showed better cracking performance by having a higher CT index.
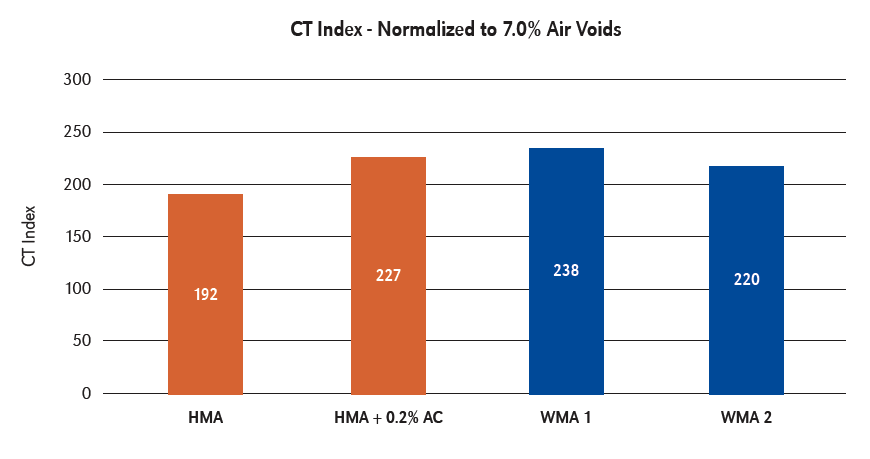
Figure 4: Cracking Tolerance (CT) Index of HMA (Orange) and WMA (Blue) mixes. (Source: Ingevity)
HMA vs. WMA: Low-temperature evaluation
To evaluate the low-temperature performance of the HMA and the chemically modified WMA mixes, the asphalt binders were extracted and recovered from the mixtures after short-term aging, to determine their PG high and low failing temperatures (i.e., the PG true grade). The PG low temperatures result in Table 1 show better low-temperature performance for the WMA mixes compared to both HMA mixes. The high-temperature impact is minimal and confirmed by the HWT rutting results.
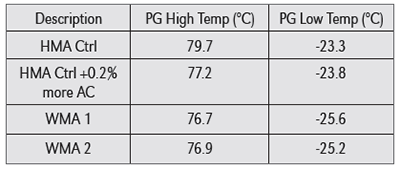
Table 2: Mixture Extraction and Recovery Binder Evaluation of HMA and WMA
These performance test results show overall improved performance when the asphalt mix is produced warm versus hot. Additionally, increasing the binder content in HMA by 0.2 percent compared to the HMA control did not provide a statistically significant difference in the cracking performance, however, the WMA provided better cracking performance and equal or better rutting resistance than the HMA with 0.2 percent more asphalt binder.
Long-Term: Limit access to oxygen
Now let’s consider what can be controlled in-service to limit asphalt binder aging and improve mix performance. Since the majority of the in-service aging is in the hands of Mother Nature, we can’t easily control things like environmental conditions, hours of sunlight, moisture exposure, effects of ultraviolet radiation, etc. What can be controlled is the access to oxygen, by reducing the amount of air in the in-place mat. This can be achieved during the final step in the construction of asphalt pavement – the compaction process – where the freshly placed asphalt mat is compressed (or densified) to reduce the in-place air voids in the mat.
Chemically-modified WMA mixes have been shown to provide better and more consistent compaction than HMA. The WMA additives enhance the lubricating properties of the asphalt binder and allow the mixes to remain workable at even lower temperatures. WMA also remains workable for a longer period than HMA because it doesn’t lose heat as quickly to the environment since there isn’t as big a difference between the WMA temperature and the ambient temperature.
New Brunswick Department of Transportation and Infrastructure (NBDTI) recently compared core compaction results for HMA and chemically modified WMA projects completed between 2017 and 2019 with PG 58-28 and PG 58-34 asphalt binders. The core compaction results for the HMA projects ranged from 92.5 to 93.0 percent and the WMA project ranged from 93.5 to 94.5 percent.
There are many other studies that show the direct relationship between compaction and pavement performance and confirm that obtaining optimum density through the compaction process is essential to long-term pavement performance. Two such studies conducted by Washington and Colorado DOTs have are highlighted in Figure 5, where both conclude a reduced service life when compaction levels drop below 93 percent (7 percent in-place air voids). The presence of air will prematurely oxidize and age the asphalt binder.
These compounding benefits of WMA to effectively limit the rate of oxidation during asphalt mix production and placement and increasing in-place density to limit long-term access to oxygen, has government agencies looking for ways to specify WMA for all contractors to use it. New Brunswick Department of Transportation and Infrastructure adopted WMA for 100 percent of their asphalt paving projects in 2019 after almost 20 years of successful usage.
Wakefield in Asphalt Institute Regional Engineer based in Canada.
Link to full-sized article and images